Gibt's das auch in Grün?

Synthetische Stickstoffdünger sind aus der modernen Landwirtschaft nicht wegzudenken. Sie steigern die Erträge der Ernte und sind relativ kostengünstig herzustellen. Das Problem: Sowohl die Gewinnung des Stickstoffes als auch die anschließende Weiterverarbeitung sind nicht gerade umweltfreundliche Prozesse. DLR-Forscherin Dr. Lena Klaas vom Institut für Future Fuels möchte das ändern. Im Team arbeitet die promovierte Physikerin im Projekt SESAM an einem neuen Verfahren für die sogenannte Luftzerlegung.
Reiner Stickstoff ist ein wichtiger Rohstoff für die chemische Industrie, zum Beispiel für die Herstellung von Düngemittel. In Zukunft könnte er auch für die Dekarbonisierung der Schifffahrt interessant werden. Wie wird Stickstoff klassischerweise gewonnen?
Luft besteht zu 78 Prozent aus Stickstoff, zu 21 Prozent aus Sauerstoff und zu einem Prozent aus weiteren Stoffen. Wenn wir den Sauerstoff aus der Luft entnehmen, bleibt quasi Stickstoff zurück. Das Verfahren nennt sich Luftzerlegung. Aktuell nutzt man hauptsächlich die kryogene Luftzerlegung. Dabei wird die Luft verflüssigt und langsam wieder erhitzt. Weil jedes Gas einen unterschiedlichen Siedepunkt besitzt, kann man die Gase so voneinander trennen.
Sie und Ihr Team haben im Projekt SESAM ein thermochemisches Verfahren entwickelt, um hochreinen Stickstoff zu gewinnen. Wie gehen Sie vor?
Kernstück von SESAM ist der von uns entwickelte Reaktor, in dem die Luftzerlegung stattfindet. Darin befindet sich ein Reaktionsmaterial, das Sauerstoff aufnehmen und wieder abgeben kann, ohne dass sich seine Struktur verändert. Wenn wir es erhitzen, gibt es Sauerstoff ab wie ein Schwamm, den man trocknet. Wenn unser „Schwamm“ trocken ist, kühlen wir ihn ab. Jetzt leiten wir Luft in den Reaktor. Das Reaktionsmaterial – der trockene Schwamm – nimmt daraus den Sauerstoff und zurück bleibt Stickstoff, den wir aus dem Reaktor ableiten. Dann erhitzen wir unser Material erneut, es wird wieder Sauerstoff freigesetzt und der Prozess beginnt von vorn.
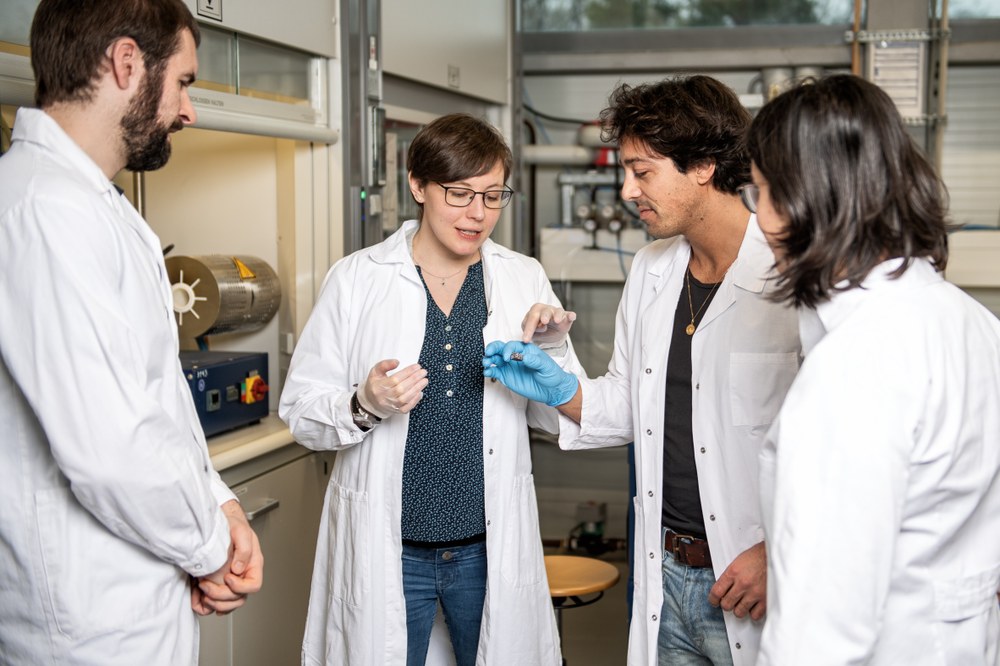
Das klingt nach einem besonderen Material ...
Absolut! Die Materialfamilie nennt sich Perovskite. Dabei handelt es sich um Keramiken, die alle denselben Bauplan haben, aber äußerst vielfältig sind. Um uns für eines zu entscheiden, haben wir zunächst eine computerbasierte Vorauswahl getroffen. Neben physikalischen und chemischen Parametern war uns auch wichtig, dass das Material ungiftig und preiswert ist. Außerdem sollte es nicht unter menschenunwürdigen Bedingungen abgebaut werden, wie es bei Kobalt häufig der Fall ist. Die Materialien, die sich als vielversprechend herausstellten, habe ich dann im Labor getestet. Wir haben uns letztendlich für ein Perovskit-Granulat aus Calcium, Strontium und Mangan entschieden.
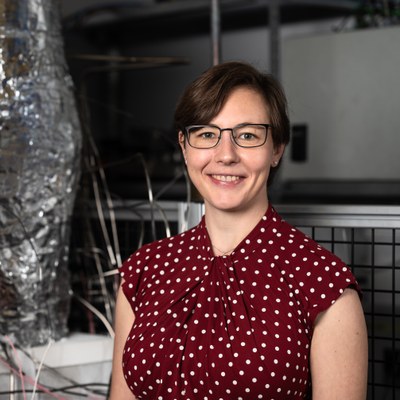
Ein entscheidender Vorteil ist, dass wir kleinskaliger produzieren können. Idealerweise könnte der Dünger dann in Zukunft direkt an den Orten hergestellt werden, wo er gebraucht wird.
Im Grunde führen Sie mit SESAM also ein neues Verfahren zur Luftzerlegung ein. Was sind dessen Vorteile?
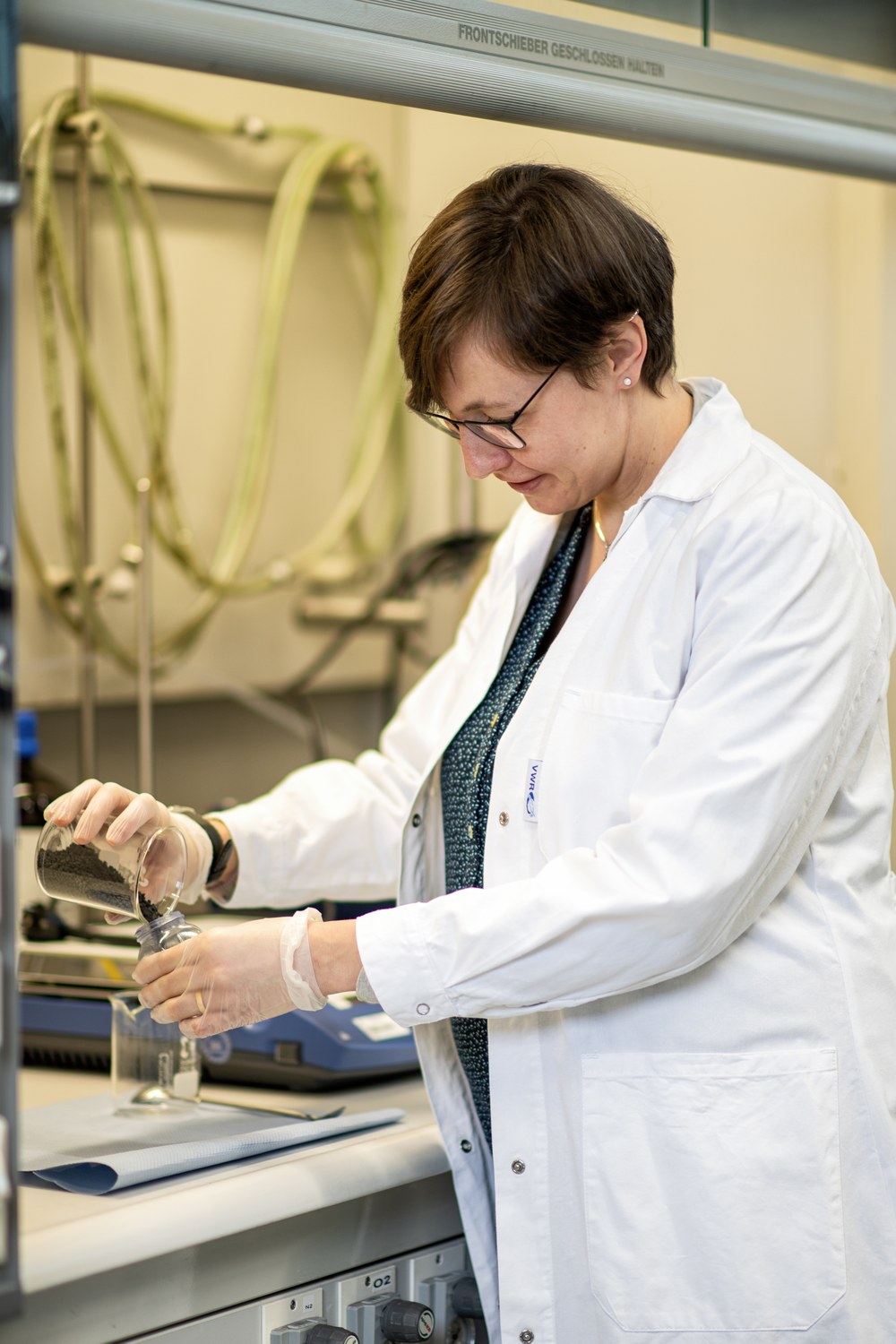
Ein entscheidender Vorteil ist, dass wir kleinskaliger produzieren können. Idealerweise könnte der Dünger dann in Zukunft direkt an den Orten hergestellt werden, wo er gebraucht wird, und zwar von Anfang bis Ende. Damit würden Emissionen und Verluste wegfallen, die momentan noch während des Transports von Ammoniak oder Dünger entstehen. Ökonomisch ist unser thermochemischer Prozess wahrscheinlich aktuell noch teurer, weil er noch nicht etabliert ist und wir ähnlich viel Energie brauchen wie die kryogene Luftzerlegung. Theoretisch wäre es natürlich möglich, aus nachhaltigen Quellen produzierten Strom auch für die kryogene Luftzerlegung zu verwenden – momentan passiert das aber nicht überall.
Die Weiterverarbeitung von Stickstoff zu Ammoniak und schlussendlich Düngemittel ist ein sehr energieintensiver Prozess. Ließe sich dieser auch grüner gestalten?
Das Ziel ist es natürlich, das komplette Verfahren CO2-frei zu bekommen, also sowohl die Luftzerlegung als auch die sich anschließenden Verfahren zur Herstellung von Ammoniak und zur Gewinnung von Salpetersäure. Beides wird für die Herstellung von Dünger gebraucht. Wir haben uns zunächst mit dem Beginn dieser Kette beschäftigt. Für unseren Prozess werden Temperaturen von bis zu 900 Grad Celsius benötigt. Wenn ich diese Wärme mit Sonnenenergie gewinne, kann ich schon mehrere Tonnen CO2 einsparen.
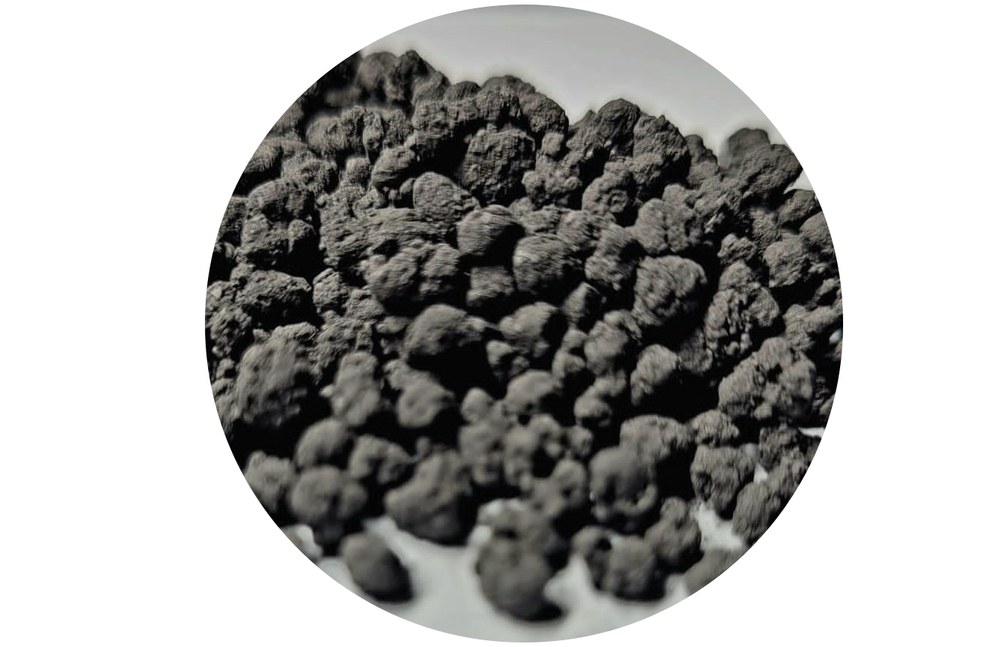
Solarenergie ist in Deutschland ja nur eingeschränkt verfügbar. Gibt es hierfür Alternativen?
Mitarbeitende von Thyssenkrupp, die mit uns im Projekt SESAM zusammengearbeitet haben, kamen auf die Idee, statt Solarenergie beispielsweise Industrieabwärme zu nutzen. Daraufhin haben wir unser Reaktordesign so angepasst, dass wir Luft als Heizmedium nutzen.
Gab es etwas im Projekt, das Sie überrascht hat?
Ja, wir waren die Ersten, die gezeigt haben, dass ein solcher thermochemischer Prozess kleinindustriell funktionieren kann. Für die Ammoniakherstellung wird hochreiner Stickstoff mit einem Luftanteil von unter 10 ppm benötigt, also zehn Sauerstoffteilchen auf eine Millionen Stickstoffteilchen. Wir haben die Luft vorgereinigt und dann durch unseren Reaktor laufen lassen. Herausgekommen sind wir bei 1 ppm, also zehnmal besser als unsere Erwartungen.
Und wie geht es jetzt weiter?
Ganz aktuell ist unser nächstes Projekt gestartet: Wir nehmen unseren thermochemischen Prozess noch einmal unter die Lupe und weiten das Materialscreening aus. Vielleicht finden wir ja ein Material, das sich noch besser eignet. Hierfür arbeiten wir mit dem DLR-Spin-off ExoMatter zusammen. Thyssenkrupp ist auch wieder dabei. Für dieses Projekt konnten wir das Unternehmen FGK gewinnen. Außerdem haben wir die Solarwärme bislang nur simuliert. Jetzt wollen wir den Prozess in unserem kleinen Sonnenofen laufen lassen. Darauf freue ich mich sehr.
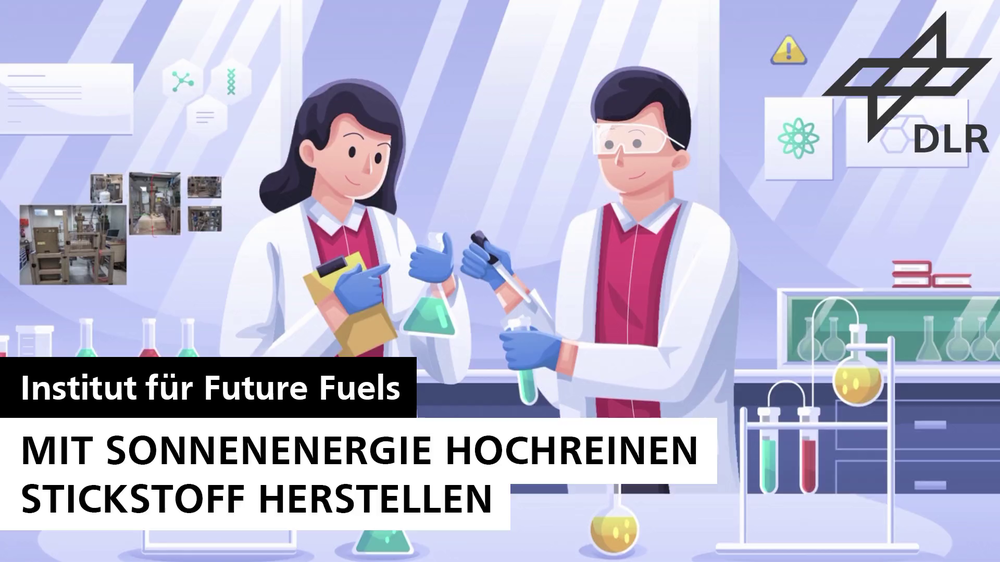
Video: DLR-Projekt SESAM – mit Sonnenenergie hochreinen Stickstoff herstellen
Für die Wiedergabe dieses Videos auf Youtube.com ist Ihre Zustimmung zur Speicherung von Daten ('Cookies') erforderlich. Unter Datenschutz-Einstellungen können Sie Ihre Wahl einsehen und verändern.
Die Fragen stellte Julia Heil. Ein Beitrag aus dem DLRmagazin 175