AIMM
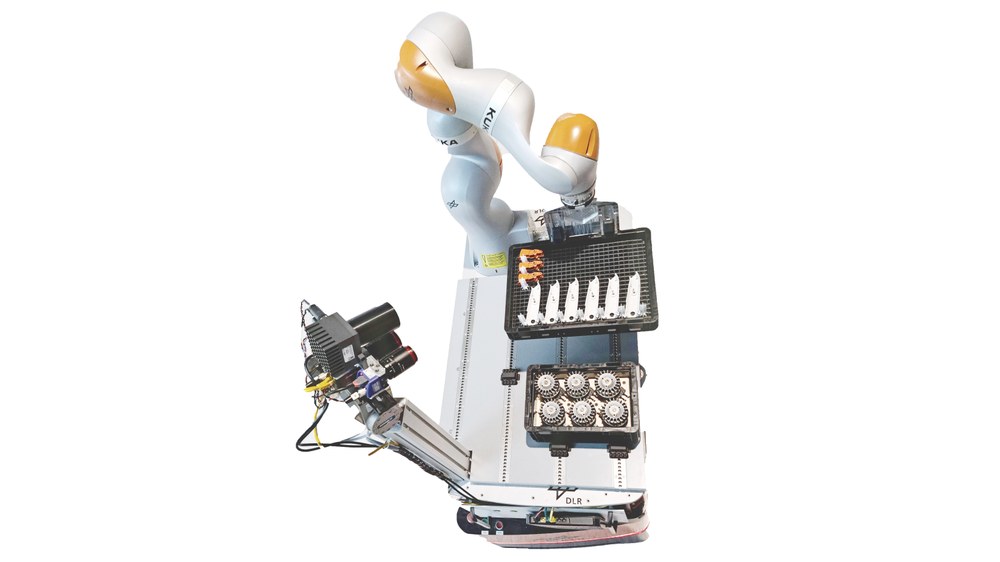
The AIMM (Autonomous Intelligent Mobile Manipulator) robot was developed for highly flexible use in production facilities and its adaptability unlocks new fields of application in agile manufacturing. AIMM is able to take on a variety of tasks at different stations depending on acute needs, where previously a large number of different specialized industrial robots were required.
AIMM was presented to the public for the first time in 2015. A completely revised version can be seen at Automatica 2023.
Technical Data
Size: | 110cm x 61cm x 225cm |
Weight: | approx. 450kg |
Degrees of freedom: | 13 |
Sensors: | • 2 Sick S300 laser scanners • stereo camera RC Viscore • color camera |
Speed: | 1–1,5m/s |
Workspace: | up to 2m height |
Features: | • mobile platform with a manipulator • pan-tilt-unit with stereo camera and pattern projector • flexibility by a tool changer • sutonomous operation |
System Description
Embedded within the Factory of the Future at DLR, AIMM represents one of many advancement in robotics of DLR. This cutting-edge system empowers the reconfiguration of other workstations, empowering the adaptability in industrial settings. With its mobile platform and integrated manipulator from KUKA, AIMM has been enhanced with a tool changer, pan-tilt unit, and multiple sensors, enabling seamless perception of the environment and objects to be manipulated. This versatility allows AIMM to effortlessly switch between various workstations and undertake different tasks, eliminating the need for dedicated robots that may prove cost-ineffective. As a result, AIMM unlocks new application possibilities while simultaneously addressing the technological challenges inherent in such a complex system. Operating on unknown terrains and responding to dynamic task variations, AIMM embraces a high level of autonomy to find its way in new environments and actively support users in implementing novel tasks. Research efforts centered around perception, planning, and programming drive AIMM towards its ultimate goal: a fully autonomous, sophisticated robotic system. All the while, AIMM remains intuitive to operate, ensuring that flexibility and frequent task programming are easily accommodated. With its integration into the Factory of the Future at DLR, AIMM leads the charge towards a transformative era of adaptable workstations and enables the future of industrial automation.
Within the EU project TAPAS, AIMM was successfully applied in a real industrial environment to aid the assembly of a rotor. The various tasks which needed to be carried out autonomously included part retrieval from multiple workstations, conveyor handling, part transportation, and delivery of finished parts to the warehouse. Within the European Robotics Challenges EuRoC, five challenger teams from all over Europe are using a newer version of AIMM to carry out various tasks ranging from robot-human logistics for aircraft assembly to maintenance operations in hazardous environments and automotive logistics at a car assembly line. In the EU project RobDREAM, the AIMM concept is applied in order to improve the mobile manipulator's performance concerning the perception, navigation, manipulation and grasping abilities.
Selected Publications
- Andreas Dömel, Simon Kriegel, Michael Kaecker, Manuel Brucker, Tim Bodenmüller and Michael Suppa, "Towards Fully Autonomous Mobile Manipulation for Industrial Environments", International Journal of Advanced Robotic Systems, 2017.
- Andreas Dömel, Simon Kriegel , Manuel Brucker and Michael Suppa. "Autonomous Pick and Place Operations in Industrial Production", In Proceedings of 12th International Conference on Ubiquitous Robots and Ambient Intelligence URAI, Goyang city, Korea, October 2015. Best Video Award. [BibTeX] [PDF] [Video]
- Simon Bogh, Casper Schou, Thomas Ruehr, Yevgen Kogan, Andreas Dömel, Manuel Brucker, Christof Eberst, Riccardo Tornese, Christoph Sprunk, Gian D. Tipaldi, and Trine Hennessy. "Integration and assessment of multiple mobile manipulators in a Real-World industrial production facility", In Proceedings of 41st International Symposium on Robotics ISR/Robotik, pages 1–8. VDE, June 2014.


