Kollege Roboter

Tobias Blaser/Lichtwerk
Ein Flugzeug zu bauen braucht Zeit. Im Gegensatz zur Automobilindustrie, wo über 1.000 Fahrzeuge pro Tag das Werk verlassen, baut Airbus etwa 60 Flugzeuge pro Monat. Dabei ist teilweise immer noch Handarbeit im Spiel: Strukturen müssen gereinigt, Stützelemente vormontiert und befestigt werden. Die Prozesse erfordern ein hohes Maß an Genauigkeit und sind sehr zeitaufwändig. Deshalb sollen neue Konzepte und Technologien dabei helfen, den Anteil an automatisierten Arbeitsschritten zu erhöhen. Zusammen mit Partnern aus Industrie und Forschung hat das DLR untersucht, wie eine solche Zusammenarbeit von Mensch und Maschine aussehen könnte.
Der Rumpf eines Mittelstreckenflugzeugs wie dem Airbus A320 besteht aus mehreren Segmenten, sogenannten Sektionen, die aus mehreren Schalen aufgebaut sind. Damit die metallische Außenhaut einer Schale nicht zerknickt, wird sie von einer Stützstruktur gehalten, ähnlich wie bei einem Schiff. Bevor der Werker oder die Werkerin die bis zu sieben Meter langen Elemente der Stützstruktur anbringen kann, müssen die Außenhaut gereinigt und eine Aktivierungsflüssigkeit sowie eine Dichtmasse aufgebracht werden. Dann erst wird das Stützelement angebracht und die Vormontage ist abgeschlossen. Bei der Endmontage müssen die Fachleute noch einmal bis zu 1.000 Nieten pro Segment setzen, um die Bauteile fest miteinander zu verbinden. Im Anschluss folgt eine abschließende Qualitätsprüfung.
„Ein riesiger Pluspunkt war für uns, dass wir Zugang zu allen Daten hatten und mit Bauteilen arbeiteten, die so an realen Flugzeugen fliegen würden.“
Dr. Marcin Malecha, Mitarbeiter beim Zentrum für Leichtbauproduktionstechnologie des DLR und Projektleiter von Agreed.
Automatisierung in der Vor- und Endmontage
Diese beiden Prozessschritte, die Vor- und Endmontage einer Schale, bildeten den Kern des Forschungsprojekts Agreed. Das DLR war Auftraggeber für das Projekt und arbeitete zusammen mit dem Flugzeugbauer Premium Aerotec daran, die Abläufe zu digitalisieren und zu automatisieren. Premium Aerotec fertigt für Airbus Rumpfteile für verschiedene Flugzeugtypen. Die Vormontage findet in Augsburg statt, die Endmontage im niedersächsischen Nordenham. „Ein riesiger Pluspunkt war für uns, dass wir Zugang zu allen Daten hatten und mit Bauteilen arbeiteten, die so an realen Flugzeugen fliegen würden. Normalerweise unterliegen diese der Geheimhaltung“, sagt Dr. Marcin Malecha. Er arbeitet beim Zentrum für Leichtbauproduktionstechnologie des DLR (ZLP) und leitete das Projekt seitens des DLR. „Außerdem haben wir mit Fachleuten aus der Fertigung zusammengearbeitet, was die Akzeptanz gegenüber den entwickelten Technologien enorm gesteigert hat. Die Ergebnisse werden für unsere zukünftige Forschung von großem Nutzen sein“, so Malecha weiter.
Planung und Entwicklung in der digitalen Fabrikhalle
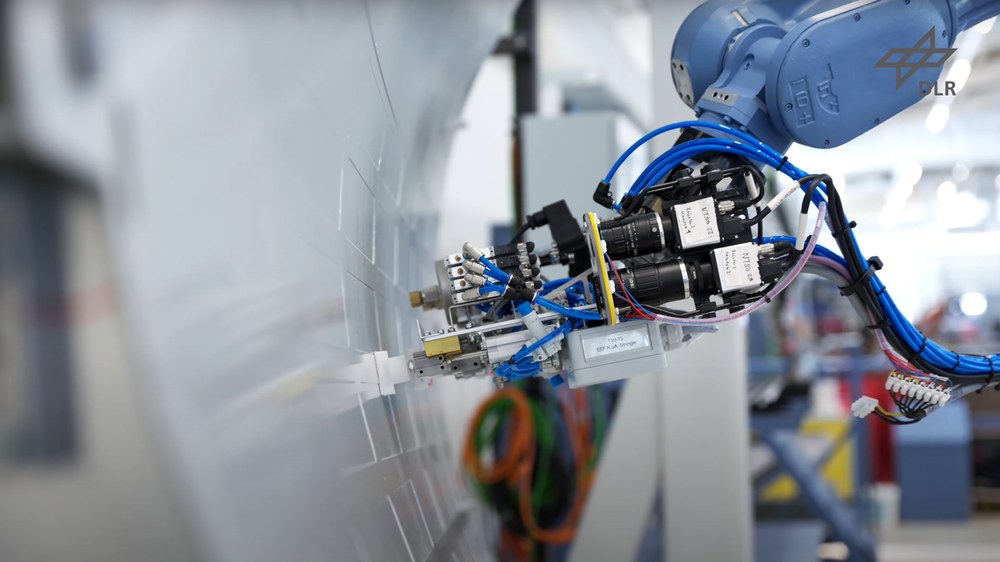
Video (engl.): Vollautomatische Vormontage im Projekt Agreed
Für die Wiedergabe dieses Videos auf Youtube.com ist Ihre Zustimmung zur Speicherung von Daten ('Cookies') erforderlich. Unter Datenschutz-Einstellungen können Sie Ihre Wahl einsehen und verändern.
Zunächst entwickelte das Team sogenannte digitale Zwillinge für die Vormontage in Augsburg und für die Endmontage in Nordenham. Dadurch wurde die Prozessentwicklung beschleunigt, da alle Werkzeuge vor dem Prototypenbau getestet und die Roboterbewegungen programmiert werden konnten, noch bevor die Anlagen aufgebaut wurden. Die virtuelle Umgebung bildete jeden Schritt der Fertigung ab. Die digitalen Zwillinge waren auch die Grundlage für den täglichen Arbeitsplan, denn sie zeigten, wie viele Werkerinnen und Werker und wie viele Roboter im Einsatz waren. Die Fachleute wurden mit Augmented-Reality-Brillen ausgestattet. Diese blendeten Arbeitsschritte sowie passende Hilfestellungen ein und steuerten so die Verteilung der Aufgaben zwischen Menschen und Robotern. In einigen Prozessschritten wurde künstliche Intelligenz eingesetzt, die die Programmierung übernahm, beispielsweise bei den komplexen Einfädelbewegungen der Clips bei der Vormontage. An anderen Stellen bewegten sich die Roboter gänzlich autonom, wie beim Bohren und der Vollständigkeitsprüfung. Die Bohr- und Nietwerkzeuge wurden speziell entwickelt und zusammen mit Leichtbaurobotern auf mobilen Transporteinheiten an den jeweiligen Einsatzort gebracht. Deren Routen wurden ebenfalls über den digitalen Zwilling gesteuert.
Parallel entwarfen die Forschenden die Roboter und die Werkzeuge, die zum Reinigen der Außenhaut und zum Fixieren der Stützstruktur benötigt wurden. Auch hier profitierten die Fachleute von dem digitalen Zwilling. „Das Programm zeigte uns direkt, ob unser Werkzeug die richtige Größe hatte oder an der richtigen Stelle angebracht war und wo wir noch Anpassungen vornehmen mussten. So konnten wir uns den Bau von vielen Prototypen sparen“, ergänzt Malecha.
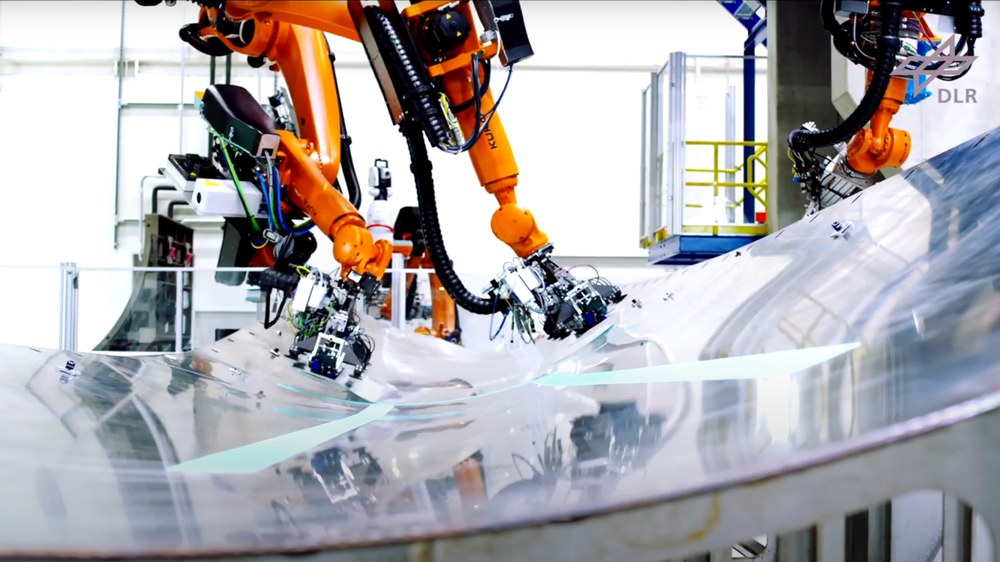
Video (engl.): Mensch-Maschine-Kollaboration im Projekt Agreed
Für die Wiedergabe dieses Videos auf Youtube.com ist Ihre Zustimmung zur Speicherung von Daten ('Cookies') erforderlich. Unter Datenschutz-Einstellungen können Sie Ihre Wahl einsehen und verändern.
Zwei Konzepte wurden erfolgreich getestet
Im Laufe des Projekts konnte das Team die Vormontage komplett automatisieren. Der Prozess lief ab, ohne dass ein Mensch eingreifen musste. Bei der Endmontage arbeiteten Mensch und Maschine eng zusammen. Auch die Qualitätssicherung am Ende wurde von einem Roboter übernommen. Dieser verglich die Position der Nieten und Bohrlöcher anhand von Fotos mit der auf den digitalen Konstruktionsplänen. Nur wenn eine Position nicht übereinstimmt, musste eine Fachkraft beurteilen, ob nachgebessert werden sollte.
Aktuell laufen die Anlagen auf den Forschungsstrecken von Premium Aerotec. „Bis eine erste automatisierte oder kooperative Station in der Fertigung genutzt wird, wird es wahrscheinlich noch zwei bis drei Jahre dauern. Seitens der Industrie herrscht aber großes Interesse gegenüber den Technologien, die in Agreed entwickelt wurden“, erklärt Marcin Malecha. Wenn es nach ihm geht, ist das Projekt hier aber nicht zu Ende. Zusammen mit Premium Aerotec soll ein Konzept für eine Station entwickelt werden, an der Roboter parallel an mehreren Bauteilen arbeiten und der Sektionsmontage folgen. Und er ist zuversichtlich: „Nicht bei allen Prozessen ist eine Automatisierung sinnvoll, aber wir haben unsere Möglichkeiten noch nicht ausgereizt.“
Das Projekt Agreed in Kürze
Das Projekt Agreed war ein internes Projekt des DLR. Ziel war die Entwicklung von Automatisierungslösungen für flexible und erweiterbare Schalenmontagen mit digitaler Intelligenz. Das DLR hat neben technologischer Forschung die administrative und planerische Rolle übernommen. Die Koordination der Arbeiten erfolgte in Zusammenarbeit mit dem beauftragten Generalunternehmer Premium Aerotec GmbH. Für umfangreiche Forschungsarbeiten wurden weitere Beteiligte aus Industrie und Wissenschaft unterbeauftragt: Broetje-Automation GmbH, Viscotec GmbH, Bergische Universität Wuppertal, Fraunhofer IFAM, Fraunhofer IFF und Capgemini.
Ein Beitrag von Dr. Marcin Malecha und Julia Heil aus dem DLRmagazin 171