Alu ade
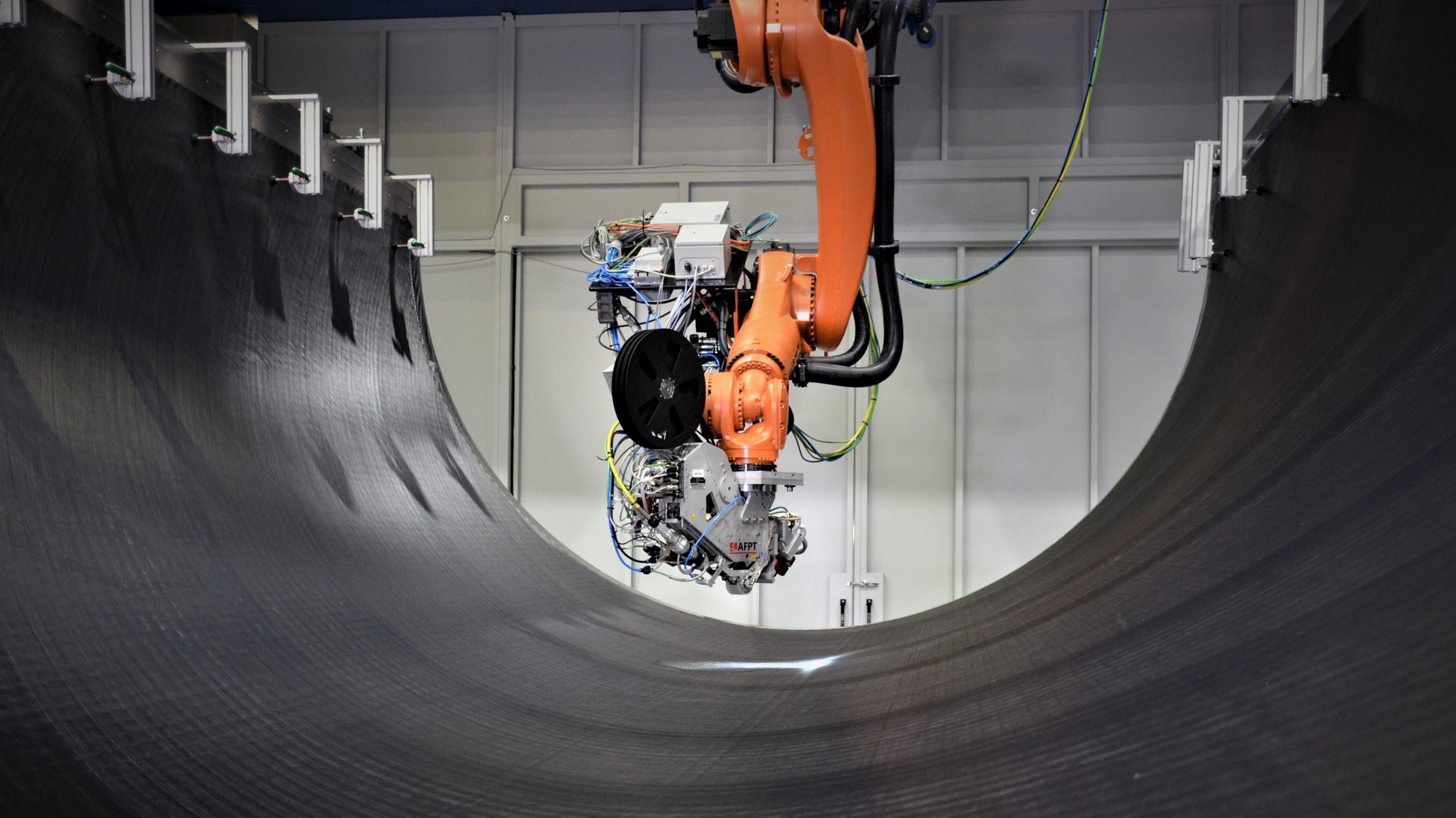
Jahrzehntelang das Nonplusultra im Flugzeugbau – Aluminium ist als Rohstoff weit verbreitet und bei gleicher Festigkeit wie Stahl nur etwa halb so schwer. Dann kamen sogenannte Thermoplaste ins Spiel. Sie gehören neben Duromeren zur Gruppe kohlenstofffaserverstärkter Kunststoffe (CFK), sind leichter als Aluminium und lassen sich schweißen. Vor knapp 20 Jahren hielt CFK im Flugzeugbau Einzug, vom Airbus A380 über die Boeing 787 bis zum Airbus A350 mit einem Carbonfaser-Anteil von bis zu 50 Prozent. Die Forschung arbeitet daran, diesen Anteil weiter zu steigern. Damit künftig der komplette Rumpf aus CFK gefertigt werden kann, werden neue Produktionsverfahren benötigt. Daran forscht das DLR in Augsburg.
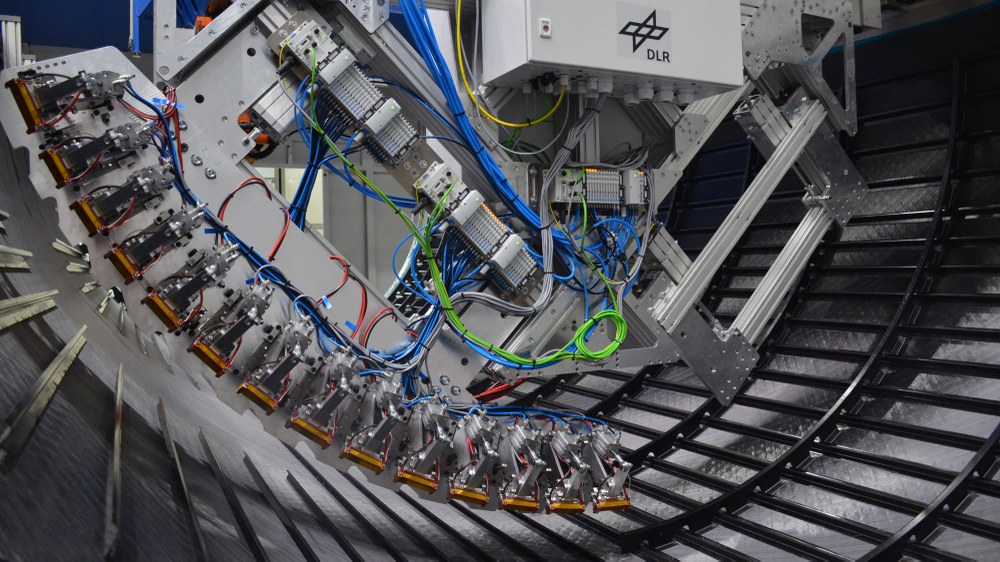
Bevor ein komplett aus CFK hergestellter Flugzeugrumpf den Weg in die Serienproduktion findet, muss das Material umfassend getestet werden. Außerdem ist die Frage zu klären, ob der neue Produktionsprozess im Detail funktioniert. Letzteres erprobten die Forschenden des DLR-Instituts für Bauweisen und Strukturtechnologie im DLR-Zentrum für Leichtbauproduktionstechnologie (ZLP) anhand eines maßstabgetreuen Rumpfmodells mit A320-Geometrie. Im europäisch geförderten Clean-Sky-2-Projekt entstand der Multifunctional Fuselage Demonstrator (MFFD), mit acht Metern Länge und vier Metern Durchmesser die weltweit größte Struktur aus 100 Prozent faserverstärkten Thermoplasten für den Luftfahrtbereich.
Arbeiten am offenen Rumpf
Der heutige Airbus A320 wird in der sogenannten Sektionsbauweise gefertigt. Dabei werden zunächst Unter- und Oberschalensegmente durch eine Längsnaht zu einer Sektion – allgemein auch „Barrel“ genannt – verbunden. Mehrere dieser Sektionen werden dann durch Umfangsnähte miteinander verbunden und bilden den Rumpf. Die Verbindungen bei Flugzeugen aus Aluminium werden durch Bohr- und Nietprozesse realisiert.
Beim Bohren der Löcher für die Nieten entstehen Metallspäne. Diese könnten elektrische Installationen beschädigen. Aus diesem Grund wird zuerst die komplette Rohstruktur gefertigt. Erst danach folgen die Einbauten im Cockpit sowie im Passagier- und Frachtbereich. Dies passiert derzeit in Handarbeit, weil es im geschlossenen Rumpf recht eng ist.
Der große Vorteil von Bauteilen aus Thermoplast-CFK ist, dass sie sich schweißen lassen und so keine Späne entstehen. Dadurch lässt sich die Montagereihenfolge komplett umdrehen: Die untere und die obere Halbschale bleiben frei zugänglich, bis beide Teile längs miteinander verschweißt werden. Dies hat grundlegende Auswirkungen auf den Prozess der Ausstattung, denn so können hier künftig Roboter zum Einsatz kommen. Sie werden in den offenen Halbschalen Leitungen verlegen, den Fußboden und Sitzreihen montieren und Verkleidungen verschrauben. Dies spart Zeit und damit auch Kosten. Nachdem ein Konsortium aus DLR, Premium Aerotec, Aernnova und Airbus die Oberschale gebaut hatte und ein Konsortium in den Niederlanden die Unterschale, wurden beide Teile am Fraunhofer-Institut für Fertigungstechnik und Angewandte Materialforschung in Stade zusammengeschweißt. Aktuell befindet sich der Demonstrator im Zentrum für angewandte Luftfahrtforschung in Hamburg. Dort kann er für weitere Arbeiten genutzt werden.
Wirtschaftlichkeit nachweisen
Die Umstellung von Aluminium auf CFK muss sich lohnen – sowohl für die Herstellerfirmen als auch für die Betreibenden. Mehrkosten, die entstehen, weil Produktionsanlagen angepasst werden müssen oder weil CFK teurer ist als Aluminium, müssen durch mehr Effizienz im Produktionsprozess ausgeglichen werden. Um zu zeigen, dass der Umstieg von Alu auf Thermoplast profitabel sein kann, wurden ehrgeizige Ziele für den MFFD-Rumpfdemonstrator definiert: Im weiteren Verlauf des Projekts soll gezeigt werden, dass 60 bis 100 Einheiten monatlich hergestellt werden können und dass – verglichen mit dem jetzigen Airbus A320 – sich das Gewicht um zehn Prozent sowie die laufenden Produktionskosten um 20 Prozent mindern lassen.
Einen Flugzeugrumpf aus Carbonfasern herstellen – Wie geht das?
Ein Beitrag von Michael Müller und Lars Larsen aus dem DLRmagazin 175