Der gute Ton
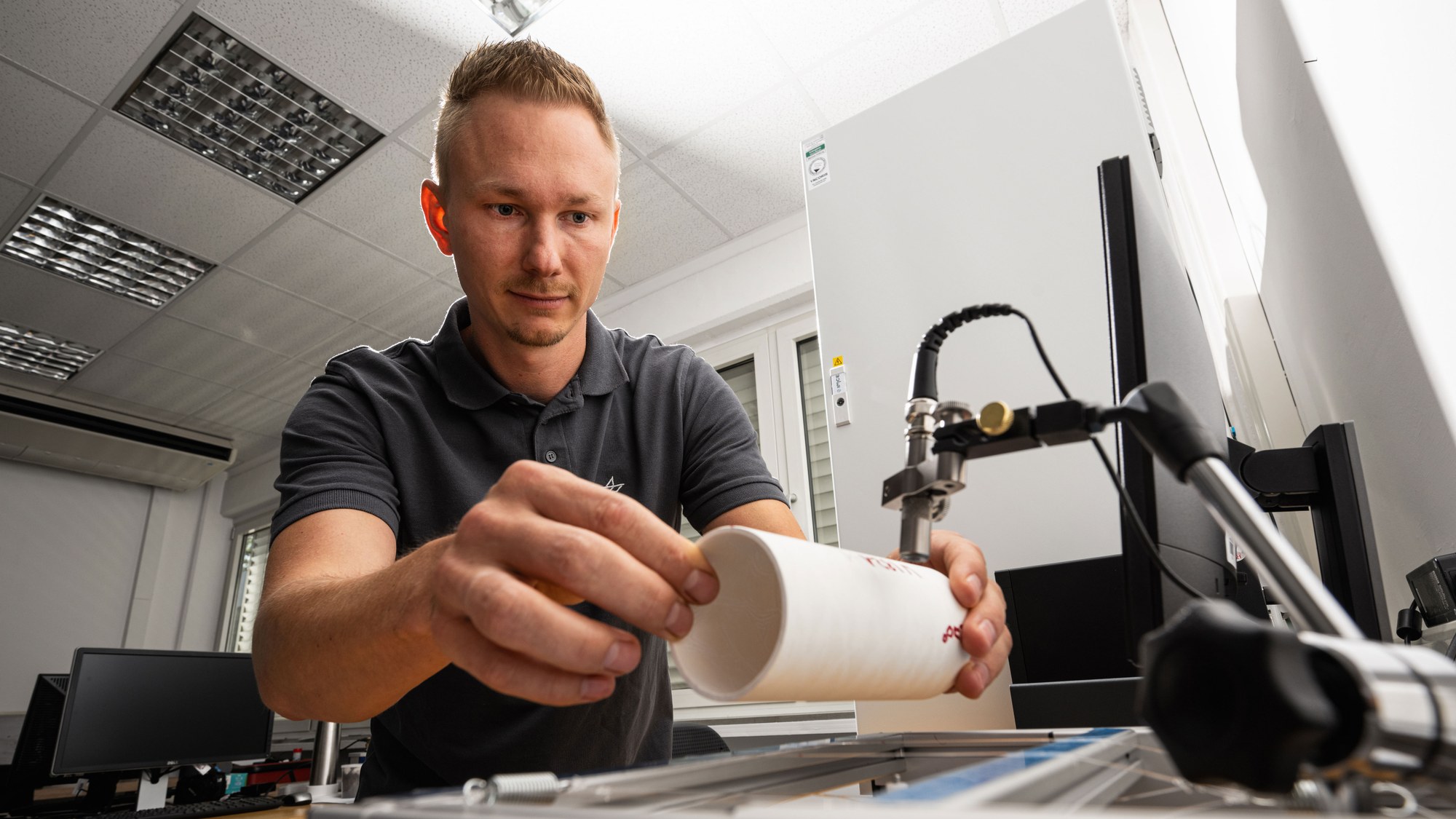
Wenn Werkstoffe unter Spannung stehen oder kleine Risse aufweisen, verändern sie ihren Klang. Auch Zug- oder Druckbelastung beeinflussen das Schwingungsverhalten von Materialien. Dies macht man sich beispielsweise beim Spielen einer Gitarrensaite zunutze. Bereits in der Antike führten Töpferinnen und Töpfer nach dem Brennen ihrer Tongefäße die Klangprobe durch. Beschädigte Gefäße haben einen dumpferen Klang. Auch heute wird die Klangprüfung eingesetzt, um bei der industriellen Serienfertigung die Qualität von Erzeugnissen aus Ton oder Porzellan zu überprüfen und beschädigte Teile schnell auszusortieren. Die Forscherinnen und Forscher im DLR-Institut für Werkstoff-Forschung verwenden diese Methode jedoch auch, um neue Hochleistungswerkstoffe für Luftfahrt, Raumfahrt oder den Energiesektor zu entwickeln.
"Bislang mussten wir unseren Werkstoff immer zerstören, um zu überprüfen, ob sich seine Belastbarkeit verändert hatte. Da der Werkstoff in einem großen Temperaturbereich eingesetzt wird, mussten entsprechend viele Proben geprüft werden, was zeitaufwändig und kostspielig war. Mit der zerstörungsfreien Klangprobe ist das nun nicht mehr nötig", beschreibt Jan Roßdeutscher, wissenschaftlicher Mitarbeiter am DLR-Institut für Werkstoff-Forschung, das Verfahren.
Stabil auch bei großer Hitze
Faserkeramische Bauteile werden beispielsweise in Hochtemperaturbrennkammern eingesetzt. Herkömmliche Brennkammern aus Metalllegierungen haben eine materialbedingte Belastungsgrenze von rund 1.200 Grad Celsius. Brennkammern aus Faserkeramik sind weitaus resistenter gegenüber hohen Temperaturen, was für die Verbrennung von Vorteil ist, da diese dann sauberer und effizienter abläuft. Durch ihre Faserstruktur sind die Keramiken weniger zerbrechlich als ihre Verwandten in Kachelform, haben aber einen ähnlichen Härtegrad.
Der Ton macht die Musik
Mit der Impulserregungstechnik lassen sich Materialproben im Temperaturbereich von Raumtemperatur bis hin zu 1.600 Grad Celsius untersuchen. Bei den Versuchen wird der Prüfkörper in der Anlage mit einem kleinen Projektil angetippt. Ein Mikrofon zeichnet die entstehende Schwingung auf. Mithilfe der Aufnahme ermittelt das Team um Jan Roßdeutscher sowohl die Resonanzfrequenz der Probe als auch ihre Dämpfung, also in welchem Maß sie die Schwingungsenergie überträgt. Die aufgezeichneten Messkurven liefern Erkenntnisse darüber, wie sich das Material im Einsatz verhält und gegebenenfalls verändern wird.
Die Forscherinnen und Forscher können auch mögliche Materialumwandlungseffekte wie das Versintern von Keramiken und chemische Reaktionen im Material erkennen. „Wir sparen extrem viel Zeit und Material, denn im Gegensatz zur Zugprüfung, die wir bislang eingesetzt haben, müssen wir nicht mehr für jede Temperatur eine neue Werkstoffprobe untersuchen, sondern können mit einer Probe beliebig viele Messpunkte aufnehmen. So können wir das temperaturabhängige Verhalten deutlich besser beschreiben“, ergänzt Jan Roßdeutscher.
„Wir sparen extrem viel Zeit und Material, denn im Gegensatz zur Zugprüfung, die wir bislang eingesetzt haben, müssen wir nicht mehr für jede Temperatur eine neue Werkstoffprobe untersuchen, sondern können mit einer Probe beliebig viele Messpunkte aufnehmen.“
Jan Roßdeutscher, wissenschaftlicher Mitarbeiter am DLR-Institut für Werkstoff-Forschung
Aktuell nutzen die Forscherinnen und Forscher die Impulserregungstechnik, um Materialkennwerte zu bestimmen. Diese sind wichtig, um größere Bauteile, die aus dem Werkstoff hergestellt werden sollen, realitätsgetreu simulieren und auslegen zu können. Mit den Ergebnissen der Klangprobe können die Faserverbundkeramiken außerdem effizienter und ökonomischer hergestellt werden, da die Wissenschaftlerinnen und Wissenschaftler die Qualität bei jedem einzelnen Produktionsschritt überprüfen können und fehlerhafte Bauteile frühzeitig erkennen.
Von Turbinenschaufeln bis Bremsscheiben
Die Ergebnisse dienen dazu, Werkstoffe zu entwickeln, die noch beständiger gegenüber hohen Temperaturen sind und dabei gleichzeitig eine hohe Festigkeit und Schadenstoleranz aufweisen. Auch bei ganzen Bauteilen aus faserverstärkter Verbundkeramik, wie beispielsweise neuartigen Turbinenschaufeln oder keramischen Bremsscheiben, liefert die Klangprobe Aussagen darüber, ob diese Schwachstellen aufweisen. Hierbei werden die Resonanzfrequenzen des Bauteils ermittelt und mit einem Bauteil verglichen, dessen Eigenschaften bekannt sind, wie ein Fingerabdruck. Wenn die gemessenen Resonanzfrequenzen deutlich voneinander abweichen, deutet dies auf einen Defekt hin.
In Zukunft möchten die Forscherinnen und Forscher des Instituts außerdem gezielt herstellungsbedingte Unterschiede zwischen ebenen und nicht ebenen Geometrien untersuchen. Das können Platten oder Rohre sein. Mit den Ergebnissen wollen sie die Simulationsmodelle und Fertigungstechnologien für Faserverbundkeramiken weiter optimieren und damit deren Zuverlässigkeit und Effizienz erhöhen.
Das DLR-Institut für Werkstoff-Forschung
Hier werden neue Werkstofflösungen und deren Prozesstechniken für Anwendungen in der Luft- und Raumfahrt, in der Energie und im Automobilsektor entwickelt. Die Wissenschaftlerinnen und Wissenschaftler untersuchen metallische, hybride und keramische Werkstoffe, sie entwickeln Beschichtungen, die das Einwirken schädigender Umgebungsmedien auf Werkstoffe, Bauteile und Strukturen verhindern, und forschen an thermoelektrischen Systemen wie auch an Aerogelen und Aerogel-Verbundwerkstoffen. Darüber hinaus werden am Institut werkstoffmechanische Prüfungen durchgeführt und Werkstoffe auf mikroskopischer Ebene analysiert.
Ein Beitrag von Michel Winand aus dem DLRmagazin 171