Variable fan blades for maximum efficiency in cruise flight
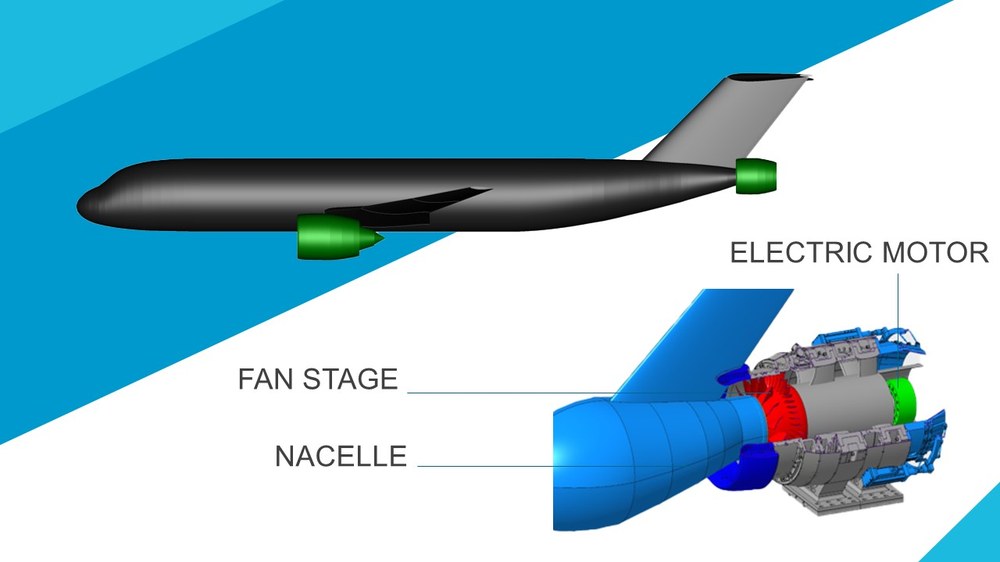
- In the LuFo project EPIFAN (development of a hybrid electric propulsion system consisting of an electric motor and a boundary-layer inlet thrust generator with experimental off-design testing), the specification of the propulsion system and the preliminary design have now been completed.
- One of the main challenges was to combine the requirements of the individual fan and electric motor components while keeping the overall weight low.
Since the advantages of boundary layer injected propulsion systems are most apparent in cruise flight, the EPIFAN propulsion system has been designed for these flight conditions and performance requirements. Careful consideration of the speed and torque ranges is particularly important, as these affect the weight of the electric motor and thus the drivetrain to be installed. Heavy propulsion systems present significant challenges for integration into the aircraft fuselage and reduce the payload of the aircraft. For this reason, the researchers are generally aiming for a low weight. The researchers' design strategy of dimensioning the powertrain for cruising flight means that the fan only reduces the rated torque of the electric motor at partial speed, and therefore partial load, at operating points close to the ground, such as during take-off and landing. The fan also operates close to its stability limit. This means that there are two possibilities at operating points close to the ground: the electric motor has power reserves and the fan aerodynamics can be improved.
At the Institute of Propulsion Technology, we see the solution in moving fan blades. On the one hand, they make it possible to increase the distance between the fan's operating points and the stability limit and, on the other hand, to utilise more of the installed power. To this end, we carried out the preliminary design, studies on the blade pitch angle range and the size of the gap between the blades and the nacelle. The variable gap geometry was a particular challenge.
OSWALD Elektromotoren GmbH analysed various motor topologies and selected the most promising design, while the Institute of Flight Propulsion and Turbomachinery at the Technical University of Braunschweig designed the fuselage, fin and nacelle. The next steps for the project team are the detailed design of the individual components. The results of this phase will then be manufactured and prepared for the test campaign.
Contact
Annabel Brückmann