Von der Raumfahrt zum Uhrengehäuse
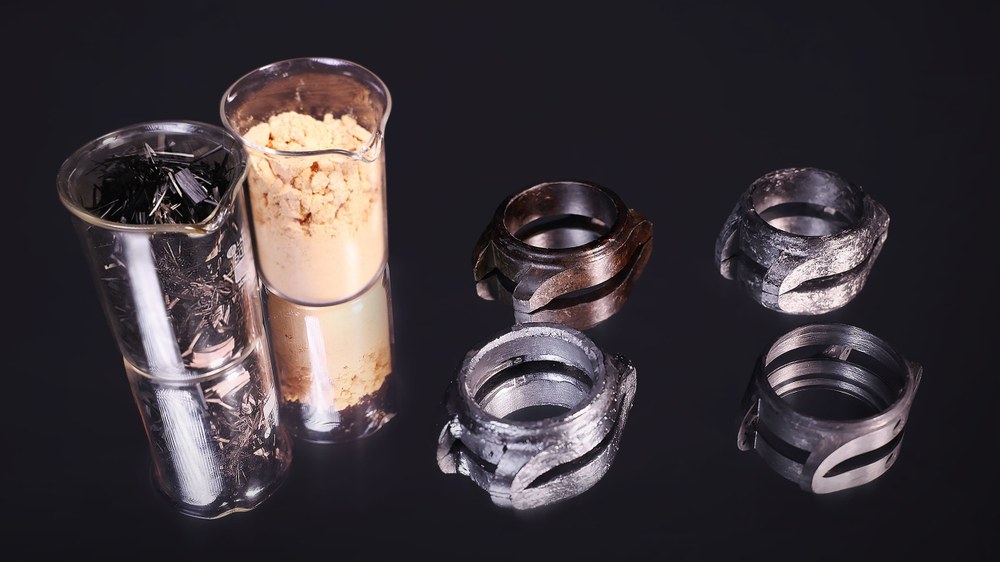
DLR/KonstantinLanduris
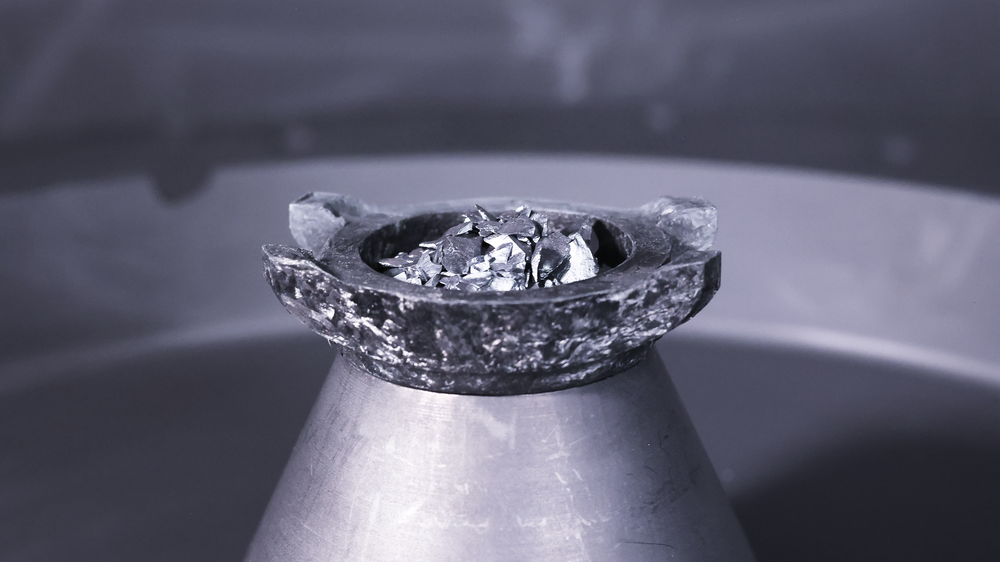
DLR/KonstantinLanduris
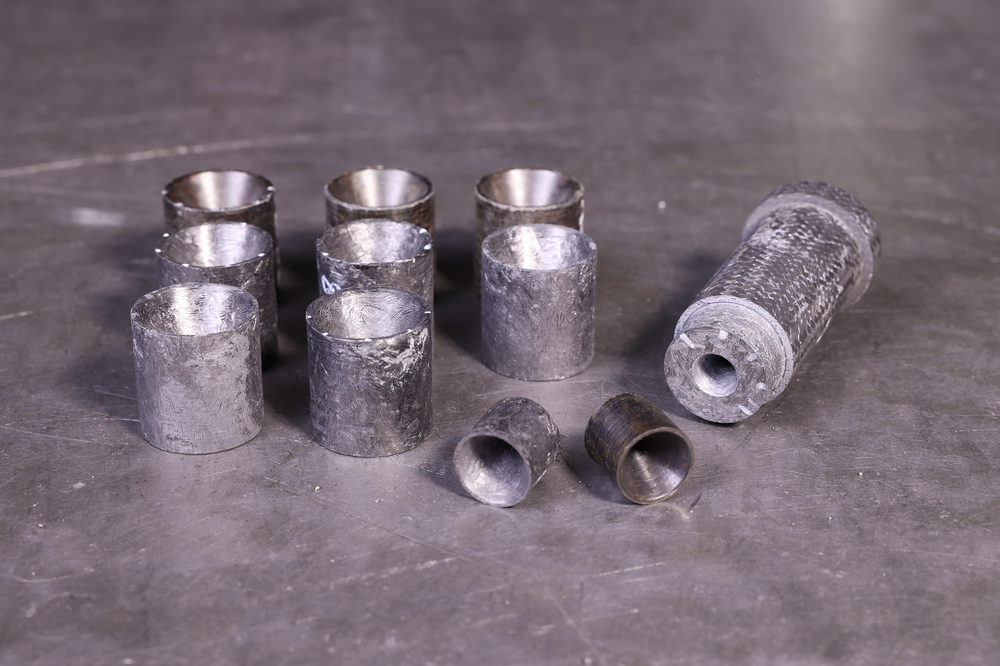
DLR/KonstantinLanduris
- Das DLR hat gemeinsam mit dem Uhrenhersteller IWC eine spezielle Hochleistungskeramik entwickelt.
- Der keramische Faserverbundwerkstoff kommt im Gehäuse einer Uhr zum Einsatz.
- Faserverstärkte Keramiken sind sehr leicht, besonders hart und halten auch große Temperaturschwankungen aus.
- Die Erfahrungen aus diesem Projekt fließen in die Entwicklung von besonders kleinen Strukturen aus diesem Werkstoff ein – zum Beispiel für die Antriebe von kleinen Satelliten.
- Schwerpunkte: Raumfahrt, keramische Faserverbundwerkstoffe, Innovation & Transfer
Faserverstärkte Hochleistungskeramiken kommen vor allem in der Luft- und Raumfahrt zum Einsatz. Anwendung finden sie aber auch im Verkehr oder in der Energietechnik. Gemeinsam mit dem schweizerischen Uhrenhersteller IWC Schaffhausen hat das Deutsche Zentrum für Luft- und Raumfahrt (DLR) einen speziellen keramischen Faserverbundwerkstoff (Ceramic Matrix Composite, CMC) und ein entsprechendes Herstellungsverfahren entwickelt, um diesen Werkstoff als Gehäuse einer Uhr von IWC zu verbauen. Das matt-schwarze Uhrengehäuse wird dadurch besonders hart, kratzfest, korrosionsbeständig und gleichzeitig sehr leicht. Neben diesen funktionalen Vorteilen, die beispielsweise besonders robuste Kanten umfassen – spielt auch die Optik eine große Rolle: Jedes Gehäuse hat eine andere, interessante Oberfläche, die durch die individuelle Struktur der eingesetzten Kohlenstofffasern zustande kommt.
Technologietransfer: Erfahrung und Know-how aus der Forschung in die Wirtschaft
Die Herstellung von CMC-Bauteilen erfordert spezielles Know-how und ausgefeilte, mehrstufige Fertigungsprozesse. Das DLR-Institut für Bauweisen und Strukturtechnologie in Stuttgart verfügt im Bereich der keramischen Faserverbundwerkstoffe über umfassende Expertise: Es erforscht diese Materialien und die dazugehörigen Herstellungsprozesse seit vielen Jahren – für den Einsatz in der Raumfahrt, beispielsweise für Hitzeschilde für Raumfahrzeuge oder in Schubkammern von Satellitenantrieben. Weitere industrielle Anwendungsmöglichkeiten auf der Erde sind Bremsen für Fahrzeuge und Aufzüge.
„Die technische Zusammenarbeit mit IWC Schaffhausen war ein wichtiger Schritt, um speziell die Machbarkeit von kleinen Komponenten aus faserverstärkter Keramik zu zeigen. Die Ergebnisse tragen dazu bei, den Werkstoff und seine Herstellungsverfahren weiter voranzubringen“, erläutert Bernhard Heidenreich, Wissenschaftler und Leiter des Projekts am DLR-Institut für Bauweisen und Strukturtechnologie. „Davon können viele weitere Projekte für Anwendungen in der Luft- und Raumfahrt profitieren – zum Beispiel unsere Arbeiten, um faserkeramische Komponenten für die Schubkammern von Satellitenantrieben weiterzuentwickeln.“ Denn in Zukunft werden sich immer mehr kleine und kleinste Satelliten auf den Weg ins All machen. Für sie sind Werkstoffe notwendig, die leicht, extrem temperaturbeständig und robust sind.
„Aufgrund der einzigartigen Kombination aus Leichtigkeit und Festigkeit ist CMC ein attraktives Material für Uhrengehäuse. Die Herstellung von faserverstärkten Keramik-Komponenten erfordert jedoch ein tiefgreifendes und sehr spezifisches Know-how. Durch die Kombination des Fachwissens von IWC und DLR in unseren jeweiligen Bereichen konnten wir gemeinsam die Grenzen dessen, was bisher mit CMC-Teilen in so kleinem Maßstab möglich war, erfolgreich verschieben", erklärt Dr. Lorenz Brunner, Abteilungsleiter Forschung und Innovation bei IWC Schaffhausen.
Hochkomplexer Herstellungsprozess
Das Fertigen und Bearbeiten von Keramik unterscheiden sich grundlegend von den Prozessen bei Metallen oder Kunststoffen. Der Ausgangspunkt für das Uhrengehäuse aus CMC ist ein mit Kohlenstofffasern verstärktes Polymer. Die Fasern werden zunächst zerkleinert und mit einem Harz als Bindemittel infiltriert. Mit einer am DLR entwickelten Presstechnologie speziell für kurze Kohlenstofffasern wird dann ein Rohling hergestellt. Dieser entspricht schon möglichst gut den Konturen des Uhrengehäuses. In einem Hochtemperaturprozess, der sogenannten Pyrolyse, wird dieser Rohling „gebacken“ und von Bindemittel befreit. Die Pyrolyse findet bei Temperaturen von rund 1.600 Grad Celsius statt und kann bis zu mehreren Tagen dauern. Es entsteht ein Werkstück aus porösem, kohlenstofffaserverstärktem Kohlenstoff.
Im nächsten Schritt, der Silizierung, werden Siliziumkristalle auf das Bauteil aufgebracht. Dann wird es erneut in einem Ofen erhitzt. Bei über 1.425 Grad Celsius schmilzt das Silizium, wird in die Hohlräume des Werkstücks gezogen und reagiert chemisch mit dem Kohlenstoff. So entsteht eine neue Struktur aus Siliziumkarbid-Keramik. Das Gehäuse ist nun so hart, dass es nur noch mit Werkzeug aus Diamanten nachbearbeitet werden kann. Ob in der Raumfahrt oder bei Uhren – in beiden Bereichen ist Präzision, Qualität und Zuverlässigkeit wichtig. Um das schon während der Entwicklung und Herstellung sicherzustellen, haben DLR und IWC die einzelnen Prozessschritte immer wieder geprüft: Dazu kamen beispielsweise zerstörungsfreie Prüfverfahren mittels Computertomographie zum Einsatz, wie sie das DLR für Strukturen aus faserverstärkten Kunststoffen und Keramiken standardmäßig nutzt.