DLR auf der Internationalen Handwerksmesse
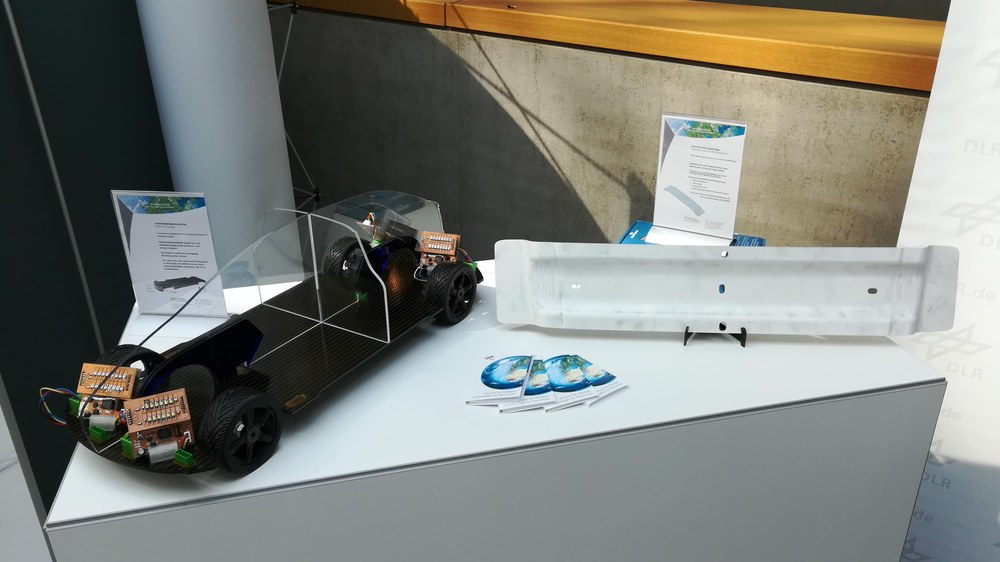
- "Systems and Control Innovation Lab" SCIL
- FlexIn Heat
- "Integrierter Kabelbaum" Strukturintegrierte lasttragende Leiterbahnen
- Integrated Positioning System
- 3D-Druckmodelle
- Schwerpunkt: Technologiemarketing
Die Internationale Handwerksmesse (IHM) in München ist der Treffpunkt für alle, die bauen, modernisieren und sanieren wollen. Vom 13. bis 17. März 2019 sind mehr als 1000 Aussteller aus über 60 Gewerken vor Ort. "Ist das noch Handwerk? Die Tradition als Basis. Die Zukunft als Vorbild." So lautet das offizielle Leitmotiv der Internationalen Handwerksmesse 2019. Das erste Mal präsentiert das Deutsche Zentrum für Luft- und Raumfahrt (DLR) Forschung für die Zukunft auf der IHM.
Besuchen Sie uns in Halle C2 Stand 360.
"Das Handwerk muss sich zunehmend mit den technischen Herausforderungen wie beispielsweise der Digitalisierung und den damit verbundenen Anforderungen auseinandersetzen. Nicht alle technischen Probleme können aber von den Handwerksunternehmen selbst gelöst werden, die Forschung jedoch kann hier wertvolle Impulse liefern. Das DLR ist ein exzellenter Innovationspartner für das Handwerk und der "Lieferant" für konkrete Lösungen. Gemeinsam mit dem Handwerk wollen wir in nächster Zeit Innovationsideen entwickeln und damit Zukunftsanwendungen, seien es Produkte, Dienstleistungen oder Verfahren möglich machen", betont Dr. Rolf-Dieter Fischer, Leiter des DLR-Technologiemarketing.
Im letzten Jahr haben das DLR und der Zentralverband des Deutschen Handwerks (ZDH) eine Kooperationsvereinbarung geschlossen mit dem Ziel, zukünftig enger zusammenzuarbeiten. Damit sollen der Technologietransfer zwischen Wissenschaft und Handwerk intensiviert und Innovationen hervorgebracht werden. "In diesem Jahr sind wir erstmalig mit einem Messestand auf der IHM vertreten und freuen uns, ausgewählte DLR-Technologien aus den Bereichen 3D-Druck, Faserverbundwerkstoffe sowie Simulation und Digitalisierung präsentieren zu können", betont Dr. Fischer.
Die Forschungsthemen des DLR:
- "Systems and Control Innovation Lab" SCIL
- FlexIn Heat
- "Integrierter Kabelbaum" Strukturintegrierte lasttragende Leiterbahnen
- Integrated Positioning System
- 3D-Druck Modelle
Die Forschungsthemen des DLR auf der IHM kurz beschrieben:
SCIL zeigt wie Unternehmen vom Digitalen Zwilling profitieren
Der Einsatz digitaler Technologien bietet Unternehmen eine Vielzahl an Möglichkeiten, um Kosten einzusparen, Entwicklungen zu beschleunigen und die Produktqualität zu verbessern. Simulationswerkzeuge wie der physikbasierte 'Digitale Zwilling' nehmen dabei eine zunehmend wichtige Rolle ein. Am Beispiel eines fiktiven Baukrans demonstriert das Systems and Control Innovation Lab (SCIL), wie ein digitaler Prototyp effizient in den Entwicklungsprozess eingebunden werden kann. Anhand des realitätsnahen Modells veranschaulichen die Experten, wie Unternehmen Simulationen für Machbarkeitsstudien, parallele Softwareentwicklung, Konstruktionsunterstützung oder Kundenakquise nutzen können. Mit einer real gekoppelten Anlagensteuerung (SPS) wird auch die virtuelle Inbetriebnahme des digitalen Prototyps demonstriert. "Mit dem fiktiven Baukran möchten wir kleinen und mittelständischen Unternehmen einen anschaulichen Einblick in das komplexe Thema Digital Engineering geben und ihnen das große Potenzial der Simulation praxisnah aufzeigen", erklärt Laborleiter Dr. Tobias Bellmann.
Das vom DLR Institut für Systemdynamik und Regelungstechnik gegründete Forschungslabor SCIL begleitet kleine und mittelständische Unternehmen (KMU) Schritt für Schritt bei der Digitalisierung ihrer Produktion und Entwicklung und macht sie so fit für den Wettbewerb. Ergänzend bietet das SCIL seinen Partnern individuelle Beratung zur Auswahl und Beantragung von passenden Förderprogrammen (EU, Bund, Länder) um gemeinsame SCIL-Projekte anzustoßen.
FlexIn Heat
Die DLR-Ausgründung msquare zeigt ein neues und effizientes Reparaturverfahren für faserverstärkte Kunststoffe. Technologischer Kern ist das innovative Heizkonzept "FlexIn Heat". Mit dessen Hilfe kann ein Reparaturstück schnell und präzise erhitzt werden, so dass es sich mit der umliegenden Struktur verbindet. Das am DLR-Institut für Bauweisen und Strukturtechnologie in Stuttgart entwickelte Reparaturkonzept verwendet flexible Induktionsspulen, die in eine Silikonvakuummatte eingegossen sind. Das System besteht aus wenigen Komponenten und ermöglicht eine schnelle und präzise Reparatur bei Temperaturen von bis zu 400 Grad Celsius - auch bei Strukturen mit gekrümmten Oberflächen.
"Integrierter Kabelbaum" Strukturintegrierte lasttragende Leiterbahnen
Buskommunikation und Stromversorgung lasttragend im KFZ-Unterboden integriert - das zeigt das DLR-Institut für Faserverbundleichtbau und Adaptronik mit dem Unterboden-Demonstrator. Mit der steigenden Anzahl an Fahrerassistenzsystemen, Motorsteuergeräten und komplexen Infotainment-Systemen in der Automobilindustrie steigt auch der Verkabelungsaufwand für die verschiedenen Sensoren und Aktoren. Das notwendige Bordnetz stellt sowohl die Spannungsversorgung als auch die Datenverbindung zwischen den einzelnen Komponenten sicher. In einem modernen Auto werden bis zu 1.500 Leitungen mit Leitungslängen von zirka drei Kilometern verlegt und kontaktiert.
Dabei trägt der Kabelbaum lediglich zum Gesamtgewicht des Fahrzeuges bei, ohne jedoch strukturelle Eigenschaften des Fahrzeuges zu verbessern. In der Luftfahrt werden bereits seit einigen Jahren viele Strukturteile aus einem Glasfaser-/Aluminium-Verbund hergestellt. Es ist daher naheliegend, zukünftige Karosseriebauteile aus einem derart hybridisierten Faserverbundkunststoff zu fertigen und die Signalübertragung und die Spannungsversorgung über die Metalllagen zu realisieren und in die Struktur zu integrieren. Abweichend vom klassischen Aufbau, bei dem Aluminium mit Glasfasern kombiniert wird, ist in Vorversuchen bereits der Einsatz dünner Stahlfolien getestet worden. Grundsätzlich ist für die Leiterbahnen jedoch jedes elektrisch leitfähige Metall denkbar. Mit der vorgestellten Technologie lässt sich die Struktur als Leiterbahn verwenden. Ein Mehrgewicht des Kabelbaums sowie die Montagezeiten beim Zusammenbauen entfallen bei diesem Konzept fast vollständig.
Integrated Positioning System
Das am DLR-Institut für Optische Sensorsysteme entwickelte IPS ist ein optisches Navigations- und Inspektionssystem für den Einsatz in Umgebungen, die keine Positionsbestimmung über ein Global Positioning System (GPS) ermöglichen - beispielsweise in Tunneln, Bergwerken, Wäldern oder Industrieanlagen. Das optische Navigations- und Messsystem ist in der Lage, die eigene Position ohne zusätzliches "Vorwissen" über die Umgebung und ohne äußere Bezugspunkte akkurat zu bestimmen. In Zukunft werden solche Sensorsysteme bei Forschungsmissionen auf fremden Planeten oder bei sicherheitsrelevanten Anwendungen auf der Erde eine entscheidende Rolle spielen. Sie sind gewissermaßen das technische Auge und liefern umfassende und wertvolle Daten.
3D-Druck Modelle
Im DLR wird eine Vielzahl von unterschiedlichen Technologien für die additive Fertigung von Bauteilen eingesetzt. Auf Grund des breiten Materialangebots, insb. auch bzgl. Hochleistungskunststoffen, findet das FDM-Verfahren (Fused Deposition Modeling) im DLR eine breite Anwendung. Bei diesem Verfahren werden thermoplastische Kunststoffe schichtenweise zum gewünschten Modell aufgebaut werden. Das Verfahren kommt zum Einsatz, wenn es darum geht schnell und im Vergleich zum Metalldruck relativ günstig Bauteile in den unterschiedlichsten Anwendungsfeldern zu drucken, beispielsweise als Anschauungsmodelle (u.a. BIROS, Philae), als Funktionsmodelle oder als Funktionsbauteile.
Das FDM-Verfahren eignet sich durch die breite Anwendbarkeit und unkomplizierte Nutzung auch sehr gut um Auszubildende und angehende Wissenschaftler für die additive Fertigung zu begeistern. Das selektive Laserschmelzverfahren (SLM) ist eine additive Fertigungstechnologie, in der verschiedenste Metallpulverwerkstoffe zu einem Modell aufgebaut werden. Mit dem Verfahren können Bauteile hergestellt werden, die mit konventionellen Fertigungstechnologien nicht bzw. nur mit erheblichem Aufwand herzustellen wären. Großer Vorteil ist der geringe zeitliche Aufwand für die Herstellung komplizierter Prototypen und damit verbunden eine Reduktion der Kosten.