3DCeraTurb
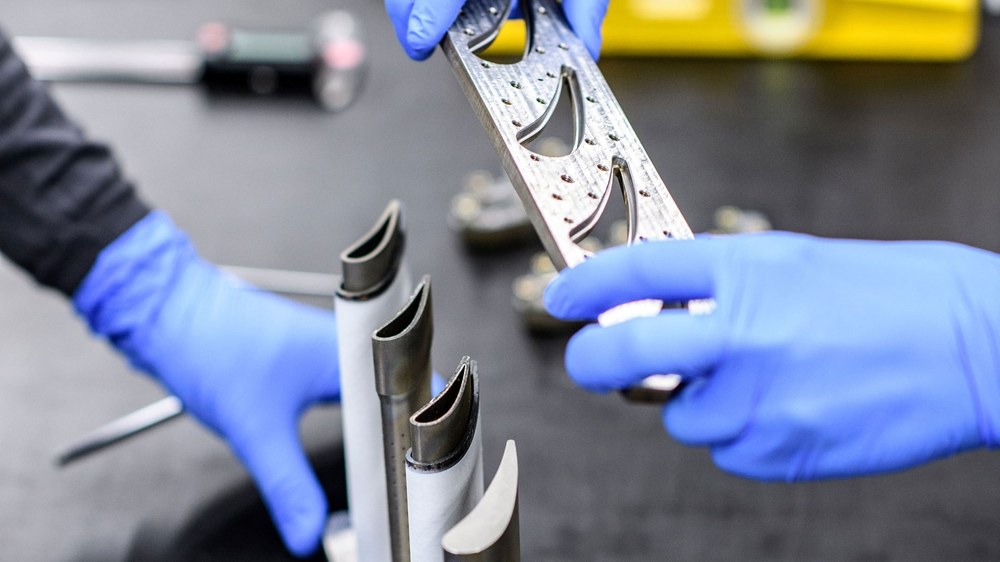
New materials and manufacturing technologies are essential prerequisites for developing ultra-efficient, low-emission engines and are therefore pivotal for the future of aeronautics.
In the 3DCeraTurb project, the German Aerospace Center (Deutsches Zentrum für Luft- und Raumfahrt; DLR) is consolidating and further advancing its expertise in new materials, design proficiency, component manufacturing, testing and evaluation, using as an example the manufacturing development of a turbine guide blade. The project utilises two important new classes of materials: additively manufactured (AM) metals and ceramic matrix composites (CMC) made of silicon carbide (SiC/SiC) fibres.
The primary objectives include the establishment of a comprehensive process chain for CMC components spanning design, production, coating, validation in the flow channel and damage assessment. Additionally, the project aims to advance design and engineering capabilities, as well as a manufacturing strategy for additively manufactured turbine blades with coatings and AM-compatible cooling structures, including assessment methods.
During the manufacturing development phase, DLR's competencies – previously applied to samples and in conventional metallic construction – will be adapted for realistic component applications.
In work package 3.1 of the 3DCeraTurb project, DLR is developing both a heater for overall flow and a heater with a swirl generator for the Straight Cascade Tunnel (EGG). To facilitate test measurements, the EGG will also include a grid slider with a blade cascade that is adaptable to various blade types.
The fundamental feasibility of these modifications to the rig was assessed as part of a concept study and, followed by a simulation of the installation in the EGG using a CAD-based simulation.
The structure consists of three heating grids with electrical connections extending through an existing slot in the EGG's rotating disc. Each grid is secured in a dedicated frame with a lateral clamp. The rapid-acting heater is positioned directly in front of the blade cascade, with slide gates forming a continuous flow channel that connects directly to the heater. Adjustable metal sheets are installed at the heater flow outlet to ensure optimal sealing with the blade cascade, directly linking to the outer blades. A primary design challenge is ensuring the flow channel remains as undisturbed as possible during testing while maintaining the temperature compatibility of all components.
By the end of 2022, after the manufacturing drawings and technical documentation for product safety were completed, all components were manufactured and pre-assembled. These preparations met the requirements for final assembly and initial channel testing in the Straight Cascade Tunnel in Göttingen.
Various manufacturing technologies will be employed for the blade cascade. Alongside ceramic blades, blade geometries will also be produced using selective laser melting (SLM), with special emphasis on the manufacturability of cooling geometries.