Electron Microscope & Microanalytics (EMA)
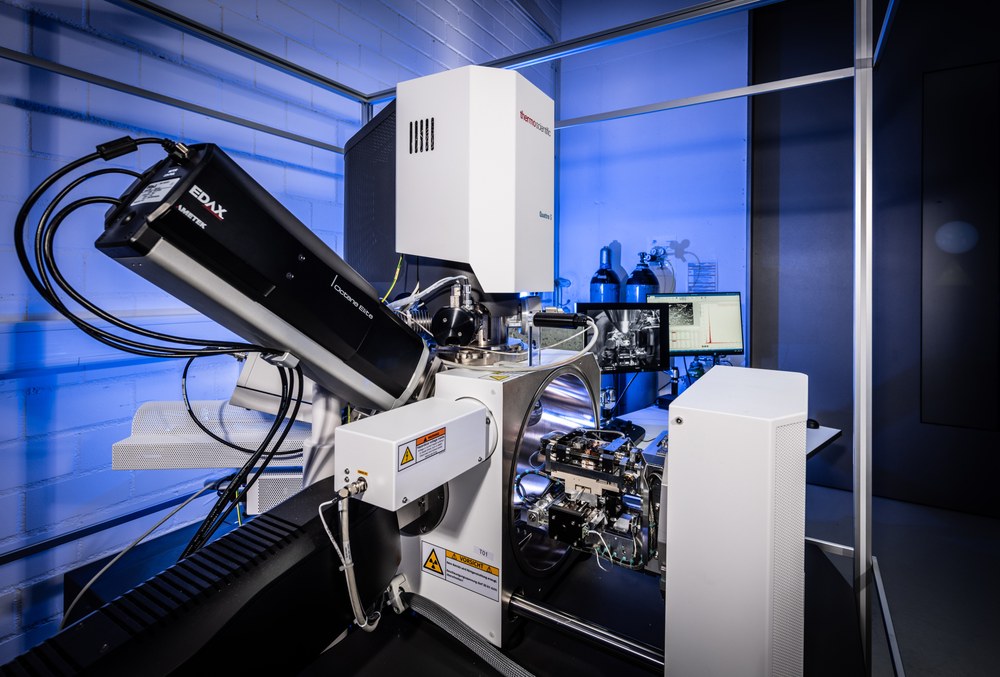
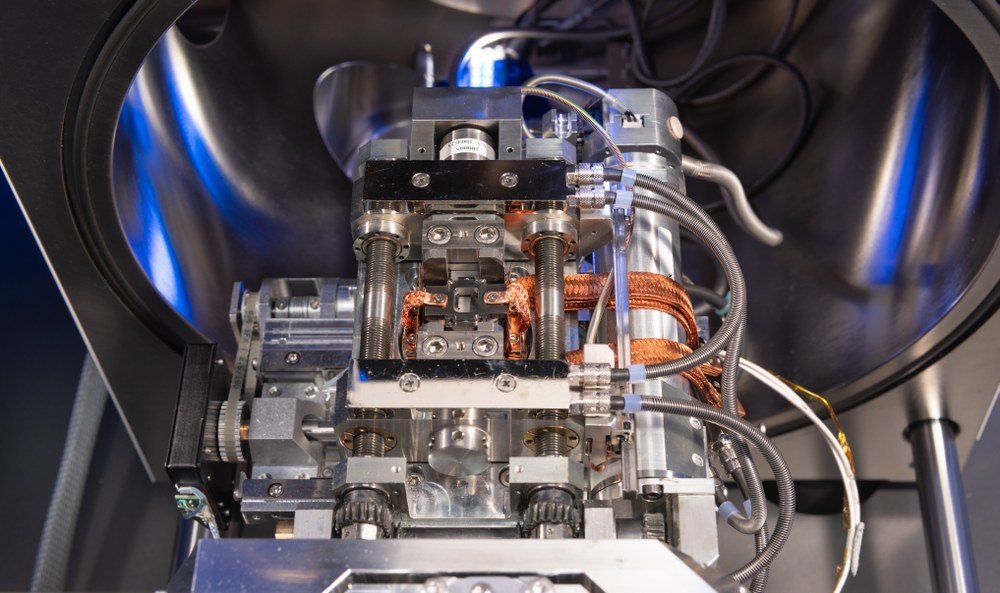
The facility at the DLR Institute of Test and Simulation for Gas Turbines in Augsburg is used for the microanalysis of materials from the engine and general turbomachinery sector. The data obtained contributes to our understanding of the degradation mechanisms due to oxidation, corrosion and mechanical fatigue at the micro and meso scale at temperatures of up to 1400 °C. The experimental data will also be used to validate lifetime models developed at the DLR Institute.
The Quattro S scanning electron microscope (Thermofisher Scientific) features an ESEM mode (environmental scanning electron microscope). In this operating mode, even non-conductive and outgassing materials can be analysed at up to 4000 Pa. Furthermore, it is possible to analyse elements using EDX and examine crystalline structures using EBSD. A heating module also enables in-situ imaging at high temperatures of up to 1400 °C.
The MZ.HD micro load frame (Kammrath & Weiss) in the Quattro S makes it possible to analyse material damage at the micro scale under tension/compression at up to 1200 °C or under LCF load at room temperature. Therefore, crack formation and crack propagation under LCF load can be investigated in-situ. The measurement of local strains at the micro scale is facilitated by imaging the secondary electrons and using digital image correlation.
Technical Data
- Scanning electron microscope ESEM Quattro S with FEG column
- ESEM mode for analysing non-conductive and outgassing materials
- Element analysis using EDS
- Analysis of crystalline structures using EBSD
- In-situ imaging at up to 1400 °C
- Micro tensile load frame in SEM for static tensile/compressive loading and cyclic LCF loading
- In-situ investigation of crack formation and crack propagation using digital image correlation
- Basic microanalytics equipment: cutting machines, grinding and polishing machines, digital microscope, stereomicroscope
Areas of Application
- Microanalysis of materials
- Development of service life models under cyclic mechanical load: crack formation and crack propagation at the micro scale
- Determination of melting points of eutectic alloys and materials
- Development of multi-physical and multi-scale lifetime models taking corrosion processes into account
- Simultaneous mechanical (M), thermal (T) and chemical (C) loading at the micro scale
- Measurement of local strains at the micro scale
- Damage analysis and fractography