First MTC test stands delivered
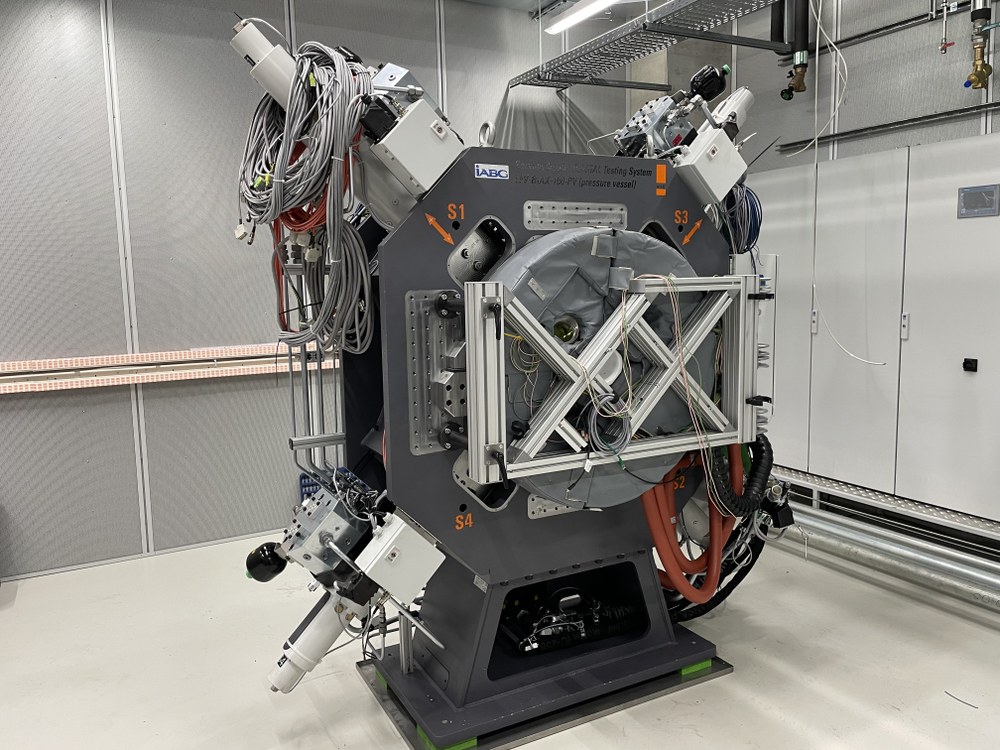
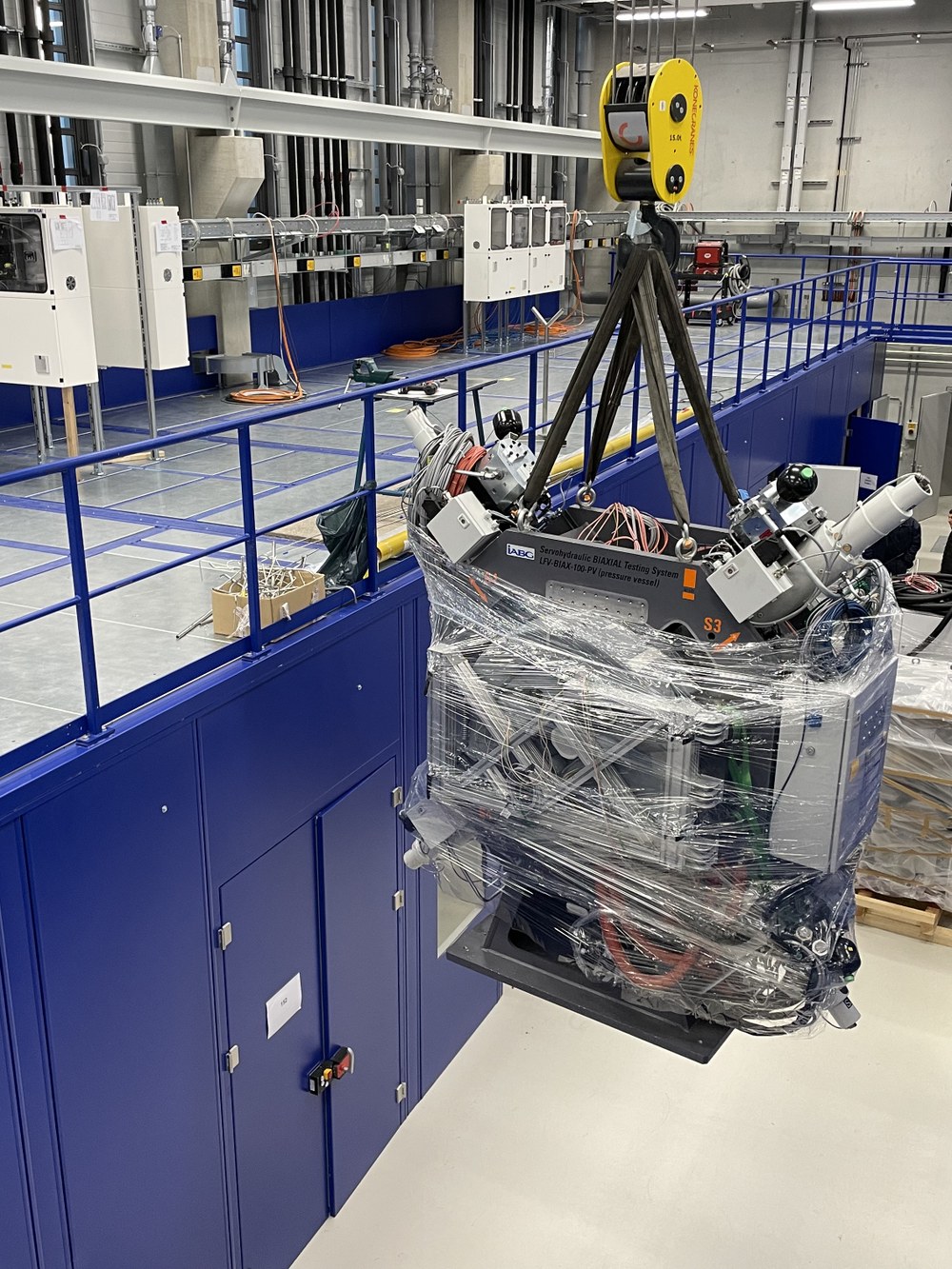
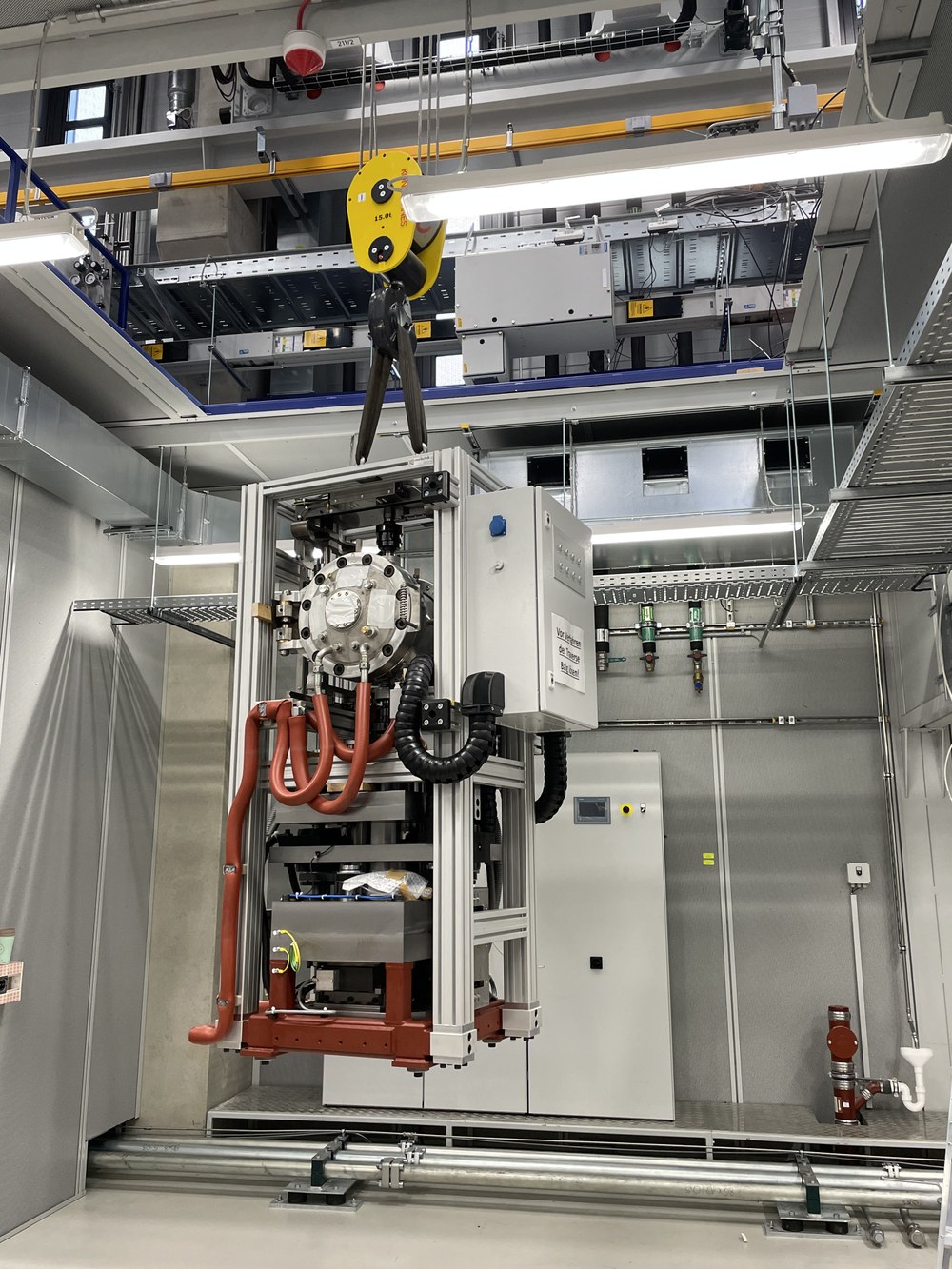
The first two MTC test stands, the MTC-Biax and the MTC-VHCF test stand (VHCF: Very High Cycle Fatigue), have now been delivered to the Institute for Test and Simulation for Gas Turbines (SG) and installed in the designated enclosures within the newly constructed test hall.
In an innovation partnership with IABG that was started in 2020, four test stands for testing materials under simultaneous mechanical, thermal and chemical loads (MTC) are being developed and procured for the DLR institute SG. With these test stands, it will be possible to test specimens under engine-like conditions with regard to their service life behavior. The results will be used to validate numerical service life models that are being developed at the SG Institute as part of the virtual engine. With these capabilities, the MTC test benches are unique worldwide and thus contribute to more reliable and precise service life predictions for engine components subjected to multi-physical loads.
The MTC test benches (Biax, Uniax, VHCF and Creep) are designed to be mechanically complementary and together cover the most relevant corrosion-induced damage behavior in the engine.
The MTC-Biax test stand enables fatigue tests with forces of up to 100kN per axis and frequencies of up to 50Hz using two servo-hydraulic actuators on each axis. By modifying the mechanical fixtures, this test rig also allows fretting fatigue testing, a damage behavior of particular relevance in the engine.
The load frame of the MTC-VHCF test stand is based on a customized electrodynamic resonance testing machine and allows a test frequency of 1000Hz with a maximum load amplitude of 25kN. This test stand is particularly suitable for service life tests with a very high number of load cycles (order of magnitude 10^9).
In all MTC test benches, the test specimen is located inside a pressure vessel that can be pressurized with a variable mixture of pure gases (N2, O2, CO2, NO, CO, SO2) and a high water vapor content in order to simulate the corrosive influence of real engine exhaust gases. Furthermore, each MTC test stand is equipped with a laser heating system that facilitates material temperatures of up to 1400°C and achieves a very homogeneous temperature on the sample thanks to the precise controllability of the laser.
Now that the two test benches have been installed, the connection to the building's supply infrastructure and the commissioning phase will follow in Q1 and Q2/2025. The delivery of the two other MTC test stands, MTC-Uniax and -Creep, are expected starting in Q2/2025.

DLR