Tape-laying machine
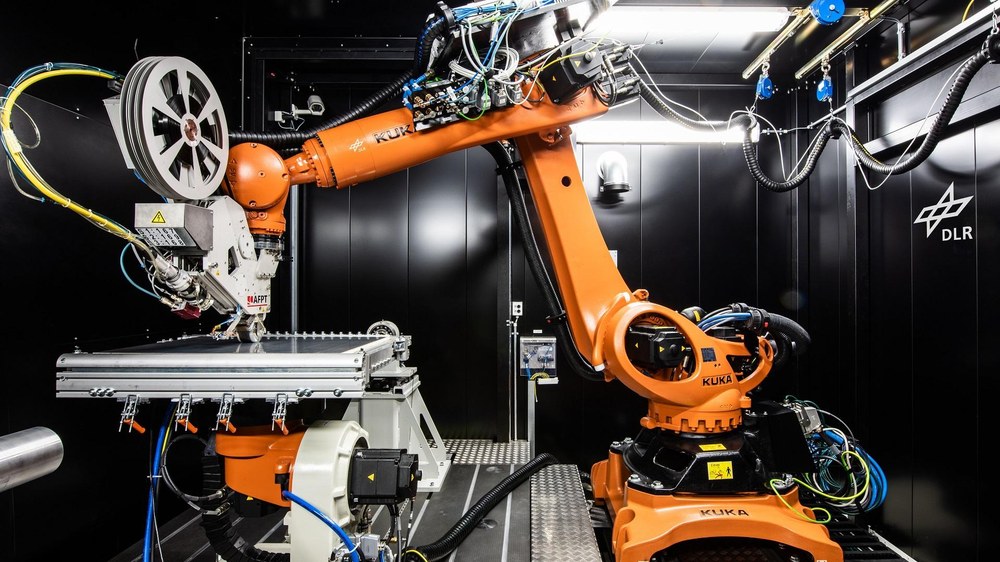


The tape-laying machine at the Institute of Structures and Design in Stuttgart is used for developing competitive, innovative manufacturing processes for hybrid, uniform fibre-composite structures for aeronautics and space, transport technology and the aircraft engine industry. The automated tape-laying process is focused on fibre-composite materials with a thermoplastic matrix.
High-performance plastics, layer by layer
The tape-laying machine for thermoplastic, semi-finished products at the German Aerospace Center (Deutsches Zentrum für Luft- und Raumfahrt; DLR) site in Stuttgart consists of a robot moving on a linear track, a rotatable arm and a rotary/tilt table. At the end of the robotic arm is a special head that lays one to three strips of material onto a mould, partially melts them using a laser, and thus builds up the required component layer by layer. The strips of material are between six and 25 millimetres wide and made of a carbon-fibre-reinforced thermoplastic, a special type of plastic in which carbon fibres are added to improve rigidity and strength.
Thermoplastics can be formed under the influence of heat and can also be welded. The facility makes it possible to manufacture components with a length of up to 3.6 metres, a diameter of 1.8 metres and a width of up to two metres. Possible components range from flat and double-curved panels and round profiles to special shapes for standard and innovative material testing. The materials are used in the production of series components such as fan blades or guide vanes for aircraft engines, large-scale fuselage components, pressure vessels and pipes.