Aerodynamics and the art of aircraft design
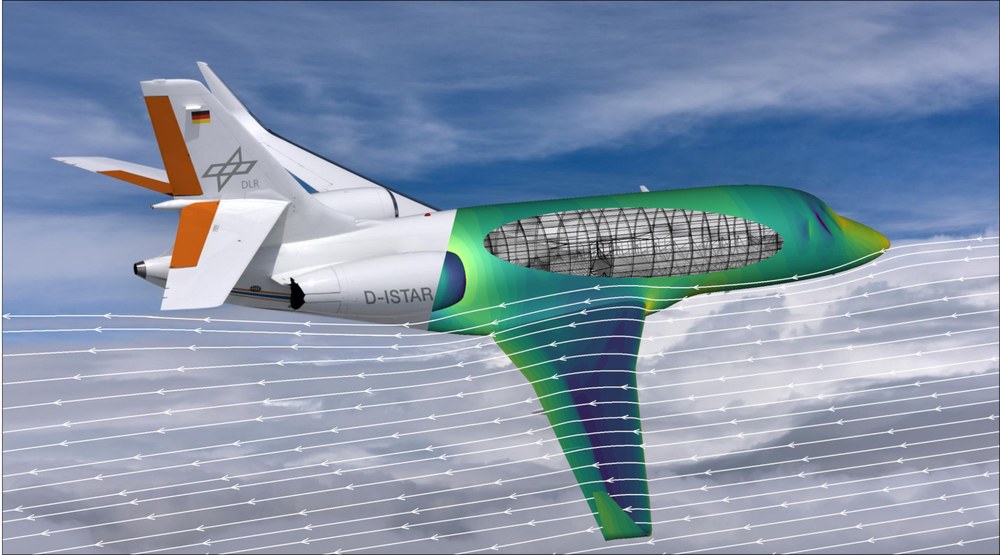
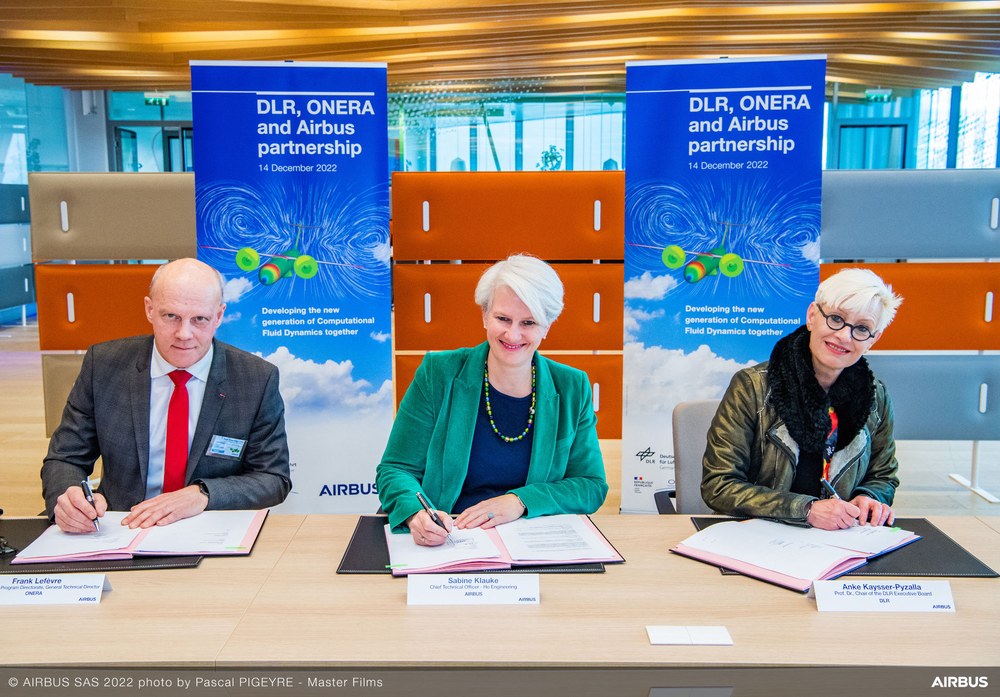
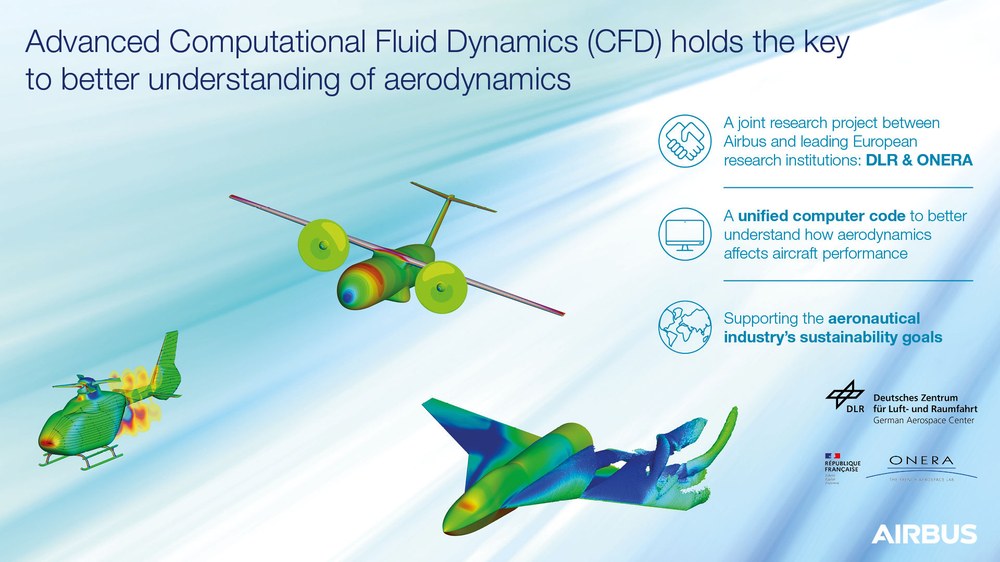
- Computer-aided flow simulation helps researchers design more efficient aircraft and thus reduce fuel consumption and emissions.
- Airbus, ONERA and DLR have cooperated closely since 2017 on the development of the next generation of CFD code. This partnership has now been extended.
- The aim is to apply the code to current and future Airbus research projects such as ZEROe, EcoPulse and Open Fan.
- Focus: Aviation, digitalisation, climate-neutral flight
Decarbonisation of aviation relies on a combination of many incremental steps and outright technological breakthroughs. To succeed, both approaches need to exist inside a collaborative ecosystem. In this spirit, Airbus and two leading European research institutions, DLR and ONERA, are exploring how high-performance computing can improve our understanding of the relationship between aerodynamics and aircraft efficiency.
Computational fluid dynamics (CFD) combines applied mathematics, physics and high-performance computing. It is used to understand how air moves over complex shapes and helps aircraft engineers maximise lift and minimise drag in order to make an aircraft as fuel efficient as possible at both low and high speeds.
"I always say that CFD is where science meets art. It's a beautiful thing, a kind of computerised wind tunnel," says Airbus' Head of Aerodynamics Simon Galpin. Galpin oversees a partnership that has existed for five years with the German Aerospace Center (Deutsches Zentrum für Luft- und Raumfahrt; DLR) and the French aerospace lab ONERA (Office National d’Etudes et de Recherches Aérospatiales) on behalf of Airbus.
'Experts at our fingertips'
DLR and ONERA have collaborated with Airbus for decades. Historically, each organisation worked on separate computer code – the foundations on which the CFD flow simulation is built. Although the code developed by each organisation was effective in its own right, communication between the different development teams was limited.
Gradually, it became clear that the code required collective re-engineering for extreme-scale parallel computing platforms. The renewed partnership addresses that shortfall. "It made sense to combine our efforts," says Galpin. "We're developing a new generation CFD code that is 'industry-ready' for flow prediction and equally applicable to aircraft, helicopters and space systems."
The signing of the first agreement in 2017 was significant for a field that demands substantial time, resources and investment. "From one day to the next the workforce doubled!” recalls ONERA's Director of Aeronautical Programmes, Philippe Beaumier. “We had a team of experts on both sides of the Rhine at our fingertips."
The partners renewed their commitment in late 2022, with the goal of extending the code to current and future Airbus projects, such as ZEROe, EcoPulse and Open Fan research. It is already being used to mature test cases previously thought unfeasible due to limited physical representation and computational capacity. Soon these cases could influence propulsion, engine integration and wing technology choices that will determine the blueprints for a new generation of fuel-efficient aircraft.
"We want to improve the predictability of performance right from the design phase," says DLR's Markus Fischer, Divisional Board Member for Aeronautics. "The new code can also help specialists investigate even more radical design concepts, such as the flying wing, with a degree of speed and accuracy that wasn’t within the grasp of previous software."
Every gram of energy counts
"Without unfettered digitalisation to accelerate the pace of innovation, decoupling air traffic growth from emissions cannot be guaranteed," argues Fischer. DLR shares the vision of zero-emission aviation held by Airbus and ONERA, one which Fischer says will require a disruptive approach. "Decarbonisation calls for a twin revolution," agrees Beaumier, "one technological and one methodological. Aircraft development cycles need to be halved to realise those ambitions. This is where mature numerical simulation plays a major role."
How does CFD make a net-zero contribution? Galpin answers by pointing out that kerosene substitutes are likely to be more costly. "We better be extracting every gram of energy from every kilogram of alternative fuel, using the most efficient aircraft architecture. Using advanced CFD helps us shave off drag little by little."
Attracting future aeronautical engineers
Airbus has access to some of the highest-performing extreme-scale computational systems in the world to help develop and validate the code, helping boost engineers' confidence in their predictions. It's an inspiring and rewarding exercise, Baumier says, with a real-world application: "To directly support the aeronautical industry's sustainability goals."
The final word goes to Pascal Larrieu, Airbus Computational Simulation Expert and the company's lead for developing the new flow solver: "This project opens doors to a diverse, dynamic and Europe-wide research network. We are convinced our work will help attract future aeronautics engineers to join us in meeting the zero-emission ambition together."