Concentrating solar thermal technology ready for efficient use in Germany
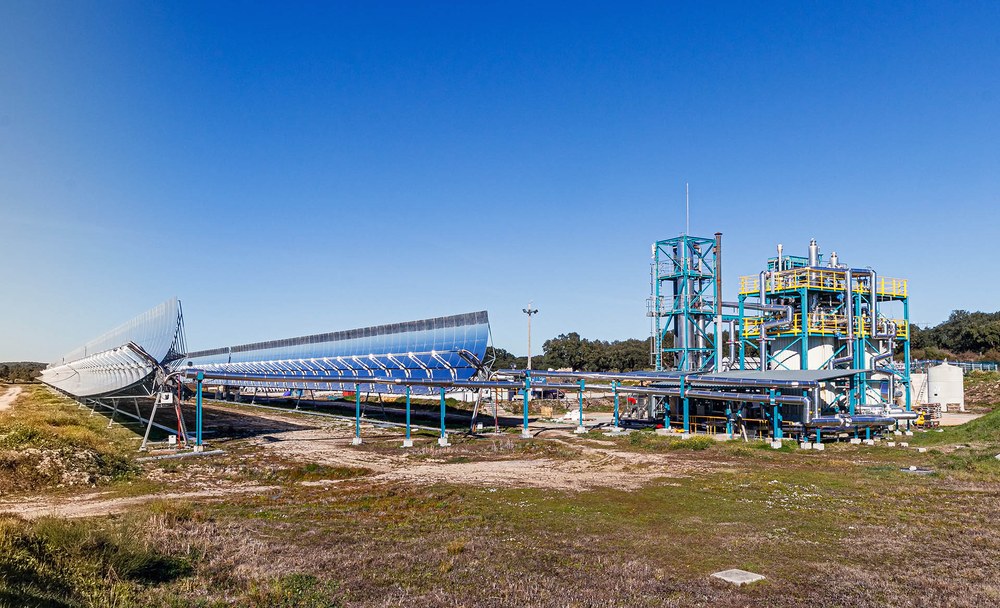
- Concentrating solar thermal systems can also be used in Germany to produce heat efficiently and cost-effectively.
- In an interview, DLR Institute Director Robert Pitz-Paal provides insight into the possibilities and prerequisites of this technology for decarbonising industrial process heat.
- Focus: Energy, process heat, decarbonisation industry, heat transition
Concentrating solar thermal systems are still little known in Germany, although they are a highly efficient approach to producing heat from solar energy. In such a system, specialised mirrors arranged in different geometries are used to focus the Sun’s rays on a defined area, such as a circle or a line. This heats a heat transfer medium, which then flows through a heat exchanger. Concentrating solar thermal power plants, which are today primarily located within Earth’s sunbelt, use this heat to generate electricity. Alternatively, the energy from concentrated sunlight can be used for industrial processes. Another advantage is that heat can be stored much more efficiently than electricity.
In this interview, Robert Pitz-Paal, Director of the Institute of Solar Research at the German Aerospace Center (Deutsches Zentrum für Luft- und Raumfahrt; DLR), describes why concentrating solar thermal technology also has considerable potential for use in Germany and Central Europe.
Why could the use of concentrating solar thermal technologies also prove effective in Germany?
Robert Pitz-Paal: For a long time, it was assumed that concentrating solar collectors would not prove effective in Central Europe, because you need as much direct sunlight as possible, along with little cloud cover. New investigations and comparisons of different collectors have shown that this is not the case. In fact, they can be a cost-effective, efficient and carbon-free solution for achieving industrial process heat between 80 and 400 degrees Celsius, even in Central Europe. This temperature range would cover approximately half of the total required industrial heat. Even in Germany, such heat production would be possible at a price of well under 10 cents per kilowatt hour.
What conditions would this require? And which applications could benefit from it?
Pitz-Paal: The prerequisite is a sufficiently large collector field, covering at least 10 000 square metres. The first such systems already exist: in Belgium, they produce industrial process heat, while in Denmark they supply local heating networks. The high price of gas and government support programmes for process heat are currently helping to make this technology economically viable in Germany. This means that we are starting from a point that is on a par with the situation in southern European countries several years ago. There are already several such facilities there. Sectors that could benefit from concentrating solar systems in Germany include the chemical and food industries, and local heating networks.
That sounds almost like a perfect remedy for our energy concerns, especially for industry.
Pitz-Paal: We have to move away from the idea that the entire industrial heat sector can be decarbonised with a single technology. Instead, we need a clever combination of different approaches. Concentrating solar systems can be part of this, as can green hydrogen and heat pumps specialised for very high temperatures, which use electricity from renewable resources. Research and industry must work together to find out which mix works best for the respective application.
What will it take for concentrating solar thermal energy to take off in process heat generation in Germany?
Pitz-Paal: Subsidies for energies based on fossil fuels, including the gas price cap, are currently leading to a certain hesitancy to switch to renewable technologies in industry. Looking to the long term, however, everyone is clear that we have to take this step. For the time being, the fact that concentrating solar systems can also prove technologically and economically sensible in Germany remains largely unknown. What we need now are a handful of demonstration projects and pilot plants, so that we can show that this technology works and showcase the possibilities it offers.
Politicians have already provided us with some of the means and funding necessary to achieve this. DLR contributes technological expertise, ideas and contacts with manufacturers. Together, we are now capable of generating knowledge, new technology and high-quality jobs here in Germany. Of course, we are also subject to global competition. China is currently the largest market for large-scale concentrating solar thermal power plants for electricity generation, so we must keep up the momentum.
How is DLR contributing to the industrialisation of concentrating solar technologies?
Pitz-Paal: Together with our partners from industry, we offer the best ways to develop innovative technology in Germany. We can help to make new technologies more efficient, more reliable, less expensive to produce and operate in all application areas – electricity, heat and fuels – and survive amid international competition. Such technologies may include advanced storage systems and heat exchangers. We are also working on harnessing recent developments in digitalisation and artificial intelligence to control collector arrays with high precision. DLR has unique large-scale research facilities that enable us to transfer concentrating solar systems from the laboratory to application, in conjunction with industry. These facilities include our solar towers and the Synlight solar simulator in Jülich and our partnership with the Plataforma Solar de Almeria, which is operated by the Spanish research institute CIEMAT. For 40 years now, we have been working together to demonstrate that concentrating solar technology fundamentally works. During this time, the expertise and experience we have acquired have seen us adopt a pioneering role in the field. We are proud that innovations from DLR have flowed into more than 90 percent of all commercial solar thermal power plants for electricity production, often via our spin-offs. Through these partnerships, we are continuing to develop the technology in a targeted way, as feedback from industrial practice shows us what we should focus on in our research.