'Urban Ray' package drone wins the NASA/DLR Design Challenge 2020
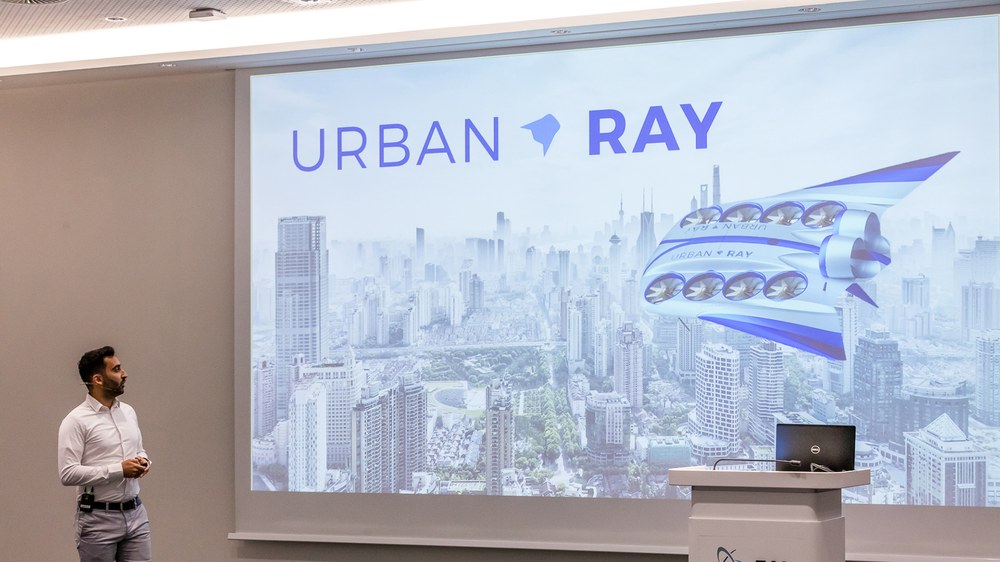
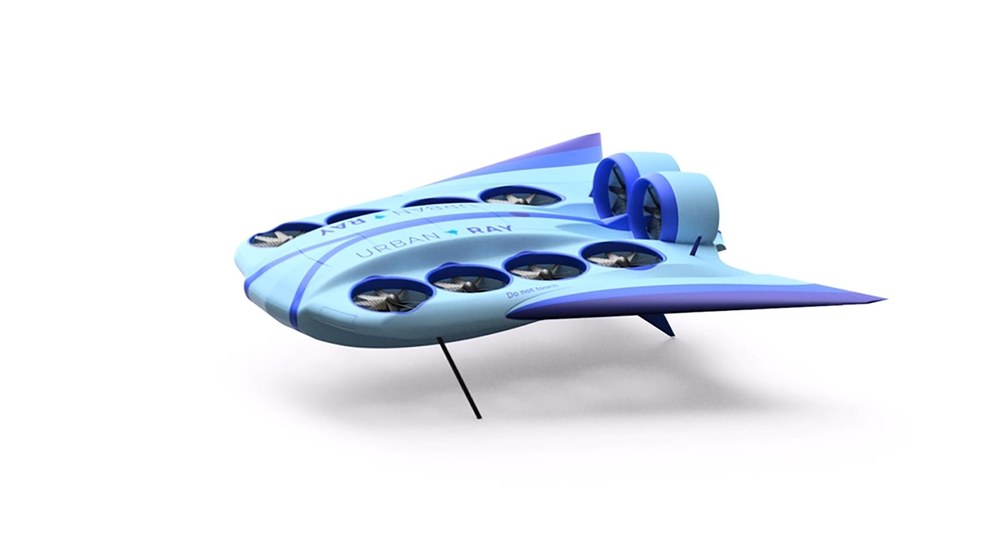
Your consent to the storage of data ('cookies') is required for the playback of this video on Quickchannel.com. You can view and change your current data storage settings at any time under privacy.
RWTH Aachen University, Chang Cao
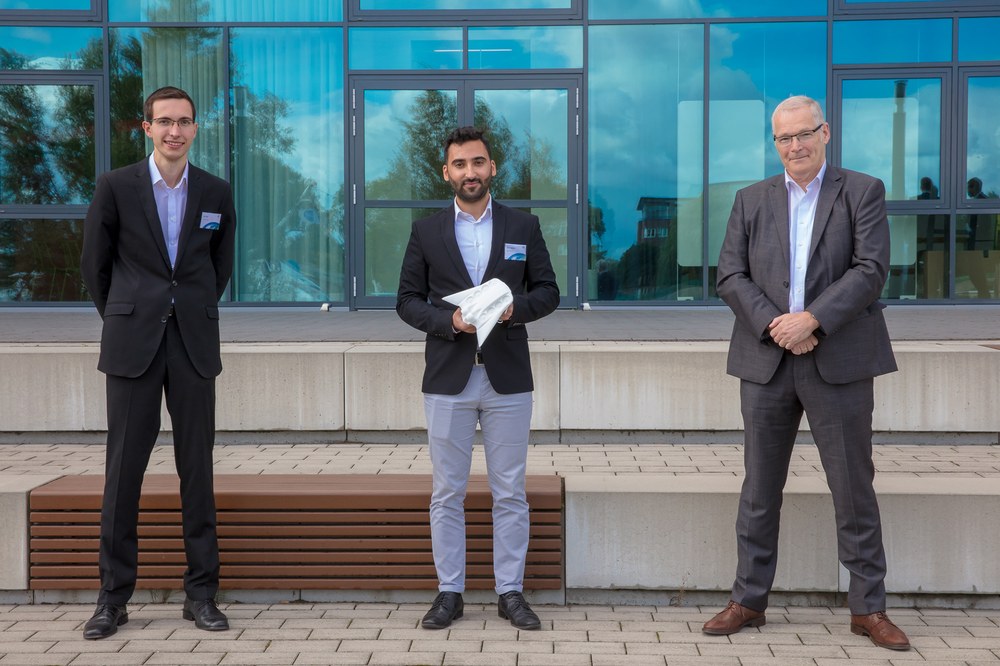
- Students at RWTH Aachen University won over the jury headed by DLR Executive Board Member for Aeronautics Research, Rolf Henke, in the German part of the competition with their 'Urban Ray' concept
- Contestants in the NASA/DLR Design Challenge were set the task of designing concepts for autonomous and reliable airborne systems for delivering goods in inner-city areas.
- Focus: Aeronautics, logistics, unmanned and electric flight, urbanisation, DLR support for young researchers
This year, the organisers of the NASA/DLR Design Challenge were looking for innovative solutions for the fully automatic and on demand airborne delivery of packages across a city. In late August 2020, seven teams of students showcased their creativity and diverse ideas at the final symposium for the German part of the competition. There, they demonstrated how the logistics of unmanned aircraft, package hubs, and landing platforms within urban areas might look in the future. The jury from the German Aerospace Center (Deutsches Zentrum für Luft- und Raumfahrt; DLR) awarded first place to the 'Urban Ray' concept from RWTH Aachen University. They were followed by the team from the University of Stuttgart, which won second place for its 'aIRO' project, and the Technical University of Munich, which came third with 'Mercurius'. The Center of Applied Aeronautical Research (ZAL) in Hamburg hosted the closing ceremony for the German teams.
"The NASA/DLR Design Challenge combines many important elements," explained Rolf Henke, DLR Executive Board Member for Aeronautics Research and chairman of the jury during the event in Hamburg. "It is about fostering young talent and encouraging collaboration between large-scale research institutions and universities in order to stimulate new designs, ideas, inspiration and transatlantic cooperation, which is particularly important for us. The winners will all have the experience of competing as part of a team and will be able to draw upon their personal achievements within a group. As a jury, we were particularly impressed that the students managed to submit seven great concepts despite the difficulties posed by the Coronavirus pandemic."
Overall concept and business model
The challenge of this year's competition was to develop an efficient, unmanned aerial system suitable for city use, together with ground stations, ground logistics, a safety strategy and a business model. The students had to work within certain parameters; their package drone had to directly transport small packages weighing up to 2.5 kilograms for a distance of up to 15 kilometres and be able to take off and land safely on very small platforms, even in cross winds. The flight altitude was set at 120 metres – a region of urban airspace that is as yet largely unused and thus offers a range of possibilities for uncrewed aircraft, in compliance with appropriate additional regulations.
NASA and DLR have now organised the student competition, which takes place in parallel in the USA and Germany, for a fourth year. This year the measures implemented as a result of the Coronavirus pandemic meant that the students primarily worked together within their teams digitally, and attended the kick-off meeting as a video conference. By the time of the final symposium in Hamburg, up to two members per team were able to attend in person to present their jointly developed concept. The rest of the team watched the event online. The prize for the winning team – a trip to the USA and a visit to NASA – has been postponed until 2021 due to the pandemic. The participating students have been invited to visit the DLR site in Braunschweig during the autumn.
On the German side, 37 students divided between seven teams from six universities entered the NASA/DLR Design Challenge 2020. Here we take a closer look at the three winning entries:
1st place – RWTH Aachen University with 'Urban Ray'
The 'Urban Ray' concept from RWTH Aachen University consists of a completely autonomous, electrically powered unmanned aircraft system (UAS) with a blended wing body configuration and separate propulsion systems (rotors) for hovering and forward flight. This enabled the team to develop an innovative, thrust-based solution for flight control that does away with the need for conventional control surfaces. The design also combines a parachute system with a shock-absorbing structure made of foam in order to meet the high safety requirements for the use of such a system in inner-city areas. The system's vertical take-off and landing (VTOL) capability also allows the use of small platforms without restricting its high cruising speeds. The team developed a modular array of platforms to create a dense, adaptable network. This included everything from a simple folding platform to a central hub with a fully automated system for the loading and storage of packages and battery changes. 'Urban Ray' is designed to be offered as a pay-per-use service for package logistics companies and other customers, such as those selling consumer goods or health products.
A brief interview with the team from RWTH Aachen University is available on DLR’s Soundcloud channel (German only).
2nd place – University of Stuttgart with 'aIRO'
The 'aIRO' concept developed by the team from the University of Stuttgart is a UAS consisting of a package drone with four wings, eight rotors and a striking red fin. The connection between the on-board computer and the control computer on the ground is maintained via real-time 5G communication, making the aircraft itself considerably lighter. A secondary flight control computer on board keeps the drone safe in the event of any connectivity issues. The combination of a tandem and multicopter configuration with quiet, electrically-powered tilt rotors uses a hybrid energy system consisting of lithium-sulphur batteries (LiS) and lithium-ion capacitors for optimised energy supply. The redundant VTOL systems are at the heart of ‘aIRO’. Ground stations the size of two standard parking spaces can be flexibly distributed around the urban area. Risk to staff and systems on the ground is kept to a minimum thanks to an all-encompassing safety strategy – a high-performance, ground-based passive radar recognition and avoidance system provides input for the flight control path via the 5G network.
A brief interview with the team from the University of Stuttgart is available on DLR’s Soundcloud channel (German only).
3rd place – TU Munich with 'Mercurius'
The 'Mercurius' drone design developed by the team from TU Munich focuses on maximum efficiency at minimum weight. Two fixed front propellers and six swivelling, rear upper wing propellers handle the conflicting requirements of hovering and horizontal flight. Design features such as inverted winglets which act as supports for the upper wing ensure good aerodynamic properties. The hybrid propulsion system, consisting of a fuel cell and a lithium-ion battery, gives the aircraft a level of performance that could not be achieved with a battery-powered concept. In addition, it maximises flight safety and energy efficiency, thus reducing the cost per package delivered by up to a third. The ground stations combine a light structure with advanced automation, ensuring the quick loading and battery charging of the drones.
A brief interview with the team from the TU Munich is available on DLR’s Soundcloud channel (German only).
The other competition entries (in no particular order):
TU Dresden with 'BeeHive'
The 'BeeHive' concept developed by the team from TU Dresden is a cost-effective, autonomous system that is able to transport small, light cargo within an urban environment at high speed. It consists of two components: the carrier drone, called the Bee, and the landing platform, called the Hive. The Bee is powered by four electric motors, which enable VTOL and allow it to deliver payloads of 2.5 kilograms over a distance of 15 kilometres. The motors are powered by lithium-ion batteries that are automatically swapped for new, fully charged batteries on the landing platform as new cargo is loaded. The system meets the highest standards for safety, noise pollution, and efficiency. It can easily be scaled up and adapted to the needs of customers.
Bundeswehr University Munich with 'eCiconia'
The 'eCiconia' concept developed by the team from Bundeswehr University Munich combines VTOL with fuel-saving, conventional wing-based aerodynamics. Horizontal flight allows precise take-off and landing within the smallest of spaces, with catapult technology reducing the energy required for the drone to take off. A central base station on the ground uses an assembly line system to load and unload parcels and change the batteries. An integrated control centre ensures efficient, reliable operation requiring minimal space and time. One attractive aspect of the concept is its ability to use existing package stations extended by a landing platform, which enables reliable package delivery without the risk of landing on the ground. A combined safety system consisting of a parachute and airbags prevents damage in the event of a system failure.
TU Hamburg with 'HecTO-R'
The 'HecTO-R' concept developed by the team from TU Hamburg is a cross between a quadcopter and a blended wing tail-sitter that combines VTOL with fast cruising speeds. The wings are optimised to ensure safe, stable flight characteristics and minimise the potential risk of accidents. High-energy batteries from Licerion are used to ensure air quality and have sufficient storage capacity for two flights. Almost all of the components are made of carbon fibre-reinforced polymers (CRP) to keep the mass and costs low. 'HecTO-R' can land very flexibly on folding stilts at the rear of the fuselage. The lightweight aluminium loading mechanism is integrated into the fuselage to allow 'HecTO-R' to place packages almost anywhere independently.
TU Hamburg with 'City-Del'
Another team from TU Hamburg developed the 'City-Del' concept, a package drone entirely made from carbon-fibre-reinforced polymer in order to minimise its weight. 'City-Del' has a vertical and horizontal mode, allowing it to operate within a confined space. The vertical mode is enabled by eight coaxially arranged rotors, which allow the drone to manoeuvre. The horizontal mode is achieved with two rotors mounted on the wings and an inverted-V tail unit. When the drone is in use, a battery pack made up of 60 cells supplies the motors and avionics with sufficient power. 'City-Del' contains a capacitor that maintains the power supply during the combined changeover of batteries and charging unit.