DLR at JEC World 2019 in Paris
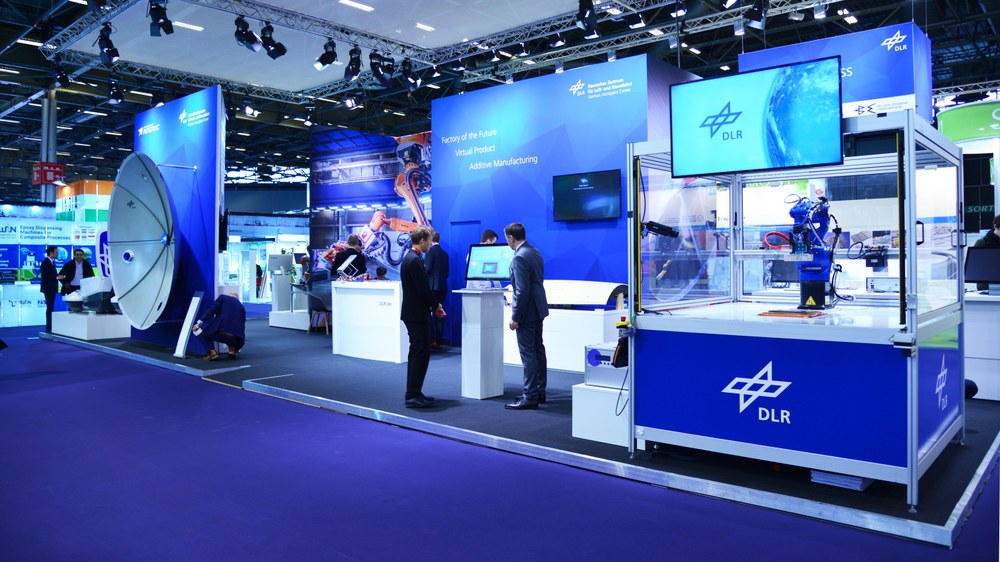
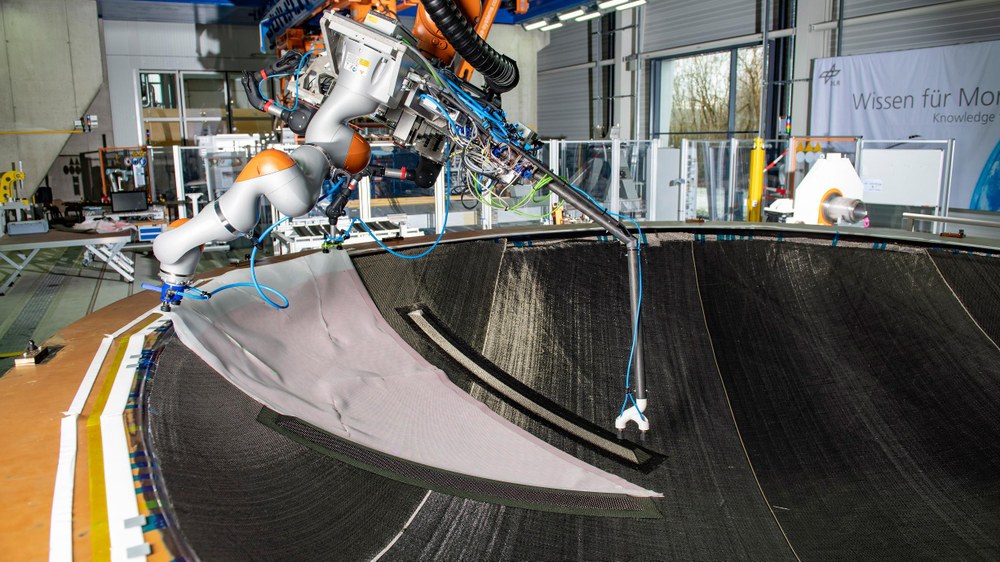
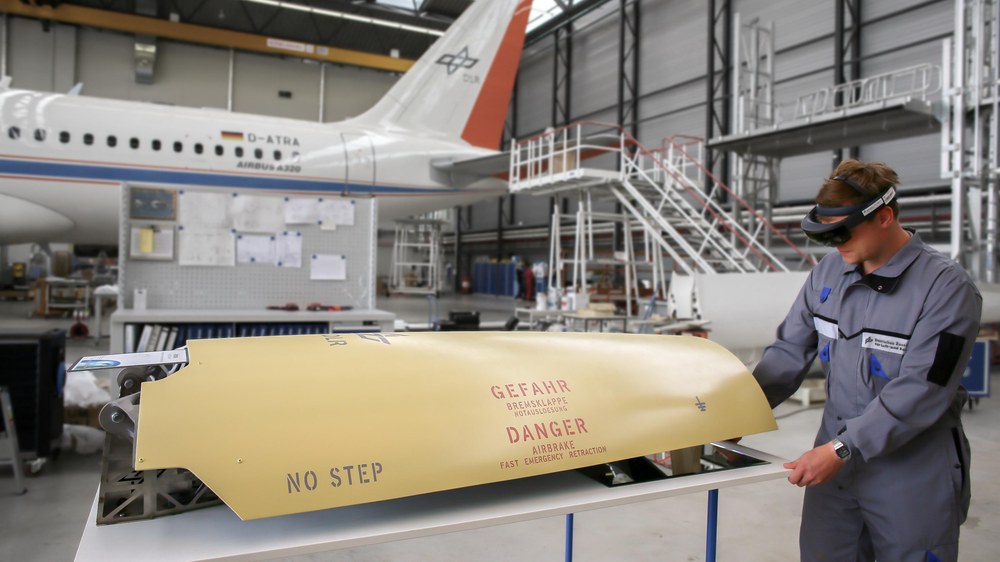
- The trade-show presentations will focus on thermoplastics technologies, production automation, additive manufacturing and virtual aircraft maintenance.
- There is a special area – ‘Science2Business’ – for technology transfer projects.
- DLR at JEC World 2019: DLR stand (Hall 5a, Stand E67); ‘Composites in Action – Additive Manufacturing’ (Hall 5a, Stand Q90); ‘Innovation Planet - Construction and Energy’ (Hall 5a, Stand E15).
- Focus: Aeronautics, digitalisation, production technology, Industry 4.0
As part of JEC World 2019, the leading European trade fair for fibre-composite technology, the German Aerospace Center (Deutsches Zentrum für Luft- und Raumfahrt; DLR) is presenting its current research projects from 12 to 14 March 2019 in Paris. Among 1300 international exhibitors from research institutions and industry, DLR is represented by the Stuttgart-based Institute of Structures and Design, the Braunschweig-based Institute of Composite Structures and Adaptive Systems, and the Center for Lightweight-Production-Technology (ZLP) in Augsburg and Stade. They will be showcasing a wide range of examples of applications from the fields of aeronautics and space.
Efficient joining through resistance welding
Joining techniques are key to the successful incorporation of thermoplastic composites in future aeronautical applications. At the DLR stand, the Institute of Structures and Design is showing its full-scale demonstrator of a thermoplastic rear pressure bulkhead. The components were joined using an electrical resistance welding process at the ZLP in Augsburg. The bulkhead was produced in collaboration with Premium AEROTEC GmbH, the Institute for Composite Materials (IVW) in Kaiserslautern and TenCate, using eight thermoformed CF-PPS segments. The researchers succeeded for the first time in using the welding process on a curved component with welding seams of this length. In order to identify the optimal joining technologies for each individual application, the ZLP in Augsburg is working on the automation of additional processes, such as continuous ultrasonic welding. Both technologies are being presented at the trade fair.
Sounding rocket payload container is a finalist for the JEC Award
In addition to welding technologies, Automated Fibre Placement (AFP) processes for industrial applications are being developed at the DLR sites in Stuttgart and Augsburg. A payload container for a sounding rocket is being presented At the JEC World trade fair. This container was produced from carbon-fibre-reinforced thermoplastic tapes (CF-PEEK) in a one-step in-situ process. The implementation without an additional post-consolidation process marks a major development step, since expensive and time-consuming vacuum bagging processes can be eliminated. This year, the payload container will fly on board the VSB-30 sounding rocket as part of the ATEK project and is therefore one of the first primary structures used in an operational flight to be produced using the in-situ AFP process. The component has been nominated for the JEC Innovation Award in the aerospace category.
Innovative heating technology for the automated placement of thermoplastics
As part of of the EU’s ‘Clean Sky 2’ research programme, the ZLP in Stade is working with the company Heraeus Noblelight to develop its humm3® heating technology for the automated placement of thermoplastic materials. In doing so, the multi-robot GroFi® system at DLR in Stade offers the best conditions to validate the heating technology for the automated fibre-placement process on large-scale thermoplastic aeronautical structures. The work aims to significantly increase the placement rates for thermoplastic structures while meeting the applicable quality requirements.
Fully automated process chain for CFRP manufacturing of large structural components
In the Protec-NSR project, the Center for Lightweight-Production-Technology in Augsburg is examining the interlinking of automated sub-processes into an integrated overall process through the manufacturing of a rear pressure bulkhead. At the DLR stand, the researchers are showing a multi-kinematic gripping system that was developed as part of the project. Three arms, each with at least six degrees of freedom, allow the gripper to be used flexibly. It can adapt to the changing requirements of different scenarios (placement of semi-finished products and additional materials, or placement of stringers) and can safely handle different geometries and sizes of cut materials.
Additive manufacturing opens up new possibilities
In the ‘Composites in Action – Additive Manufacturing’ area (Stand Q 90), DLR is showcasing its activities in the field of 3D printing. The rapid development of 3D printing is creating increasingly sophisticated lightweight components whose use in the manufacture of composite materials opens up new possibilities.
Under the term AddCompS™ (Additive Composite Structures), research is being conducted into how 3D-printing processes can be integrated into existing production technologies. The vision is that the production of today’s fibre composite components using fibre placement heads will merge with the new possibilities offered by 3D printing. This requires a new integrated methodology with innovative approaches for materials, planning, design, optimisation, manufacturing and production through to certification, taking into consideration the best combination of the various manufacturing processes in each phase. The DLR Institute of Composite Structures and Adaptive Systems is developing a new type of additive extrusion technology, which processes standard thermoplastics as well as high-performance materials, such as PEI or PEEK. With the help of this innovative process, carbon fibres that are to be placed are impregnated with the accompanying thermoplastic material in the extrusion unit. The direct processing of the raw materials enables particularly cost-effective production of a CFRP component.
In the IRAS (Integrated Research Platform for Affordable Satellites) project, the Institute of Structures and Design is developing technologies for the flexible and cost-effective production of satellite structures. The great design freedom offered by 3D printing makes it possible to design, produce and qualify lightweight, multifunctional components. One focal point of the research is the integration of electronics and sensors in load-bearing sandwich panels. In the MuSIK project, the multi-material printing of C/Si/SiC ceramics is being implemented. Here, ceramic precursor compounds developed in-house are processed as filaments or pellets via additive extrusion into ceramic components. These compounds are suitable for use in components that are exposed to high temperatures, corrosive environments, high pressures or abrasion. Application areas include the energy sector, in addition to the space sector.
Aircraft maintenance in the future
Using ‘Airbrake’ as an example, the DLR Institute of Composite Structures and Adaptive Systems is demonstrating the future possibility of maintaining aircraft on the basis of augmented reality, remote collaboration and a decentralised database (digital twin). The demonstration includes a structural health-monitoring system for in-service inspection based on ultrasonic waves (Lamb waves). These waves are excited and detected by a network of 36 fixed piezoceramic transducers, thus making it possible to detect structural damage. An inspection task can be carried out using augmented-reality glasses, in this case the ‘Microsoft HoloLens’. The system can also serve as an interface for the exchange of information between the physical component and the digital twin. Such a system has the potential to increase maintenance quality and significantly reduce the costs and the downtime for an aircraft.
‘Science2Business’ technology transfer
DLR promotes the transfer of technology from cutting-edge research to practical use and is presenting two spin-offs as well as two collaborative projects with SMEs in the ‘Science2Business’ area at the trade fair. At the Institute of Structures and Design, an innovative heating technology called FlexIn Heat has been developed in order to repair damage in composite structures quickly and precisely. By combining flexible heating mats and mobile repair kits, two young researchers have become entrepreneurs, founding the company msquare GmbH. Another example of a spin-off from the Institute of Structures and Design is Black Engine Aerospace UG. This company has its origins in the transpiration-cooled ceramic high-thrust rocket engines developed at DLR. This is referred to as Black Engine technology.
For the process monitoring of complex structural components made of fibre-composite plastics, the DLR Institute of Composite Structures and Adaptive Systems is collaborating with Grasse Zur Ingenieurgesellschaft mbH to develop an ultrasound-based sensor technology that can detect the progress of the curing process in fibre-composite structures. In cooperation with COBES GmbH, the automated induction welding of carbon-fibre-reinforced thermoplastics is being investigated, and an innovative inductor is being jointly developed as a result.
We will be reporting live on 13 March 2019 from the JEC in Paris via our Twitter channels in German and English.