DLR tests turbines for more environment-friendly aircraft
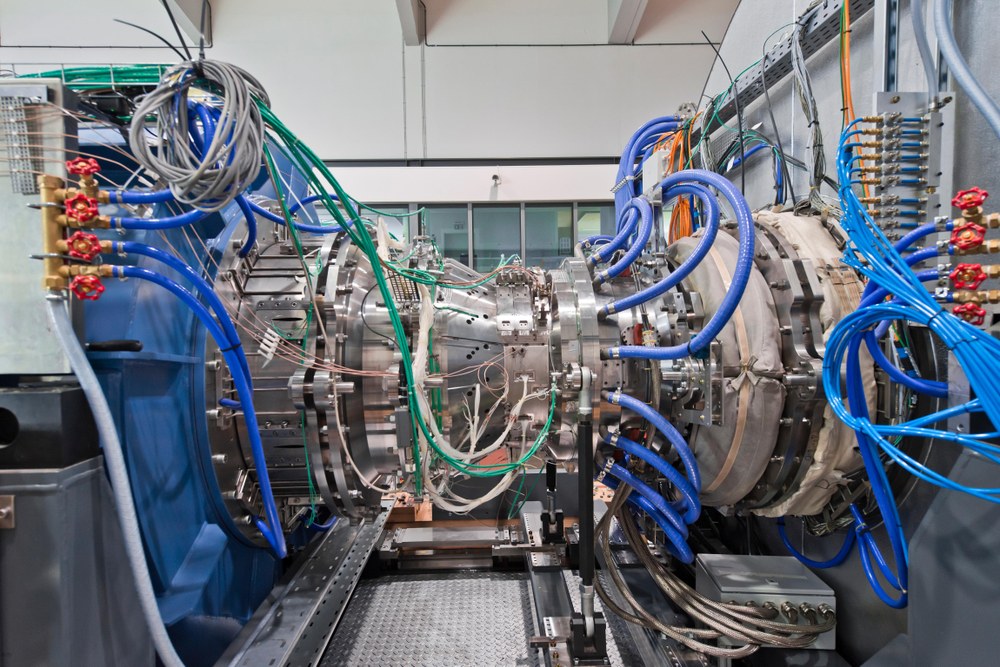
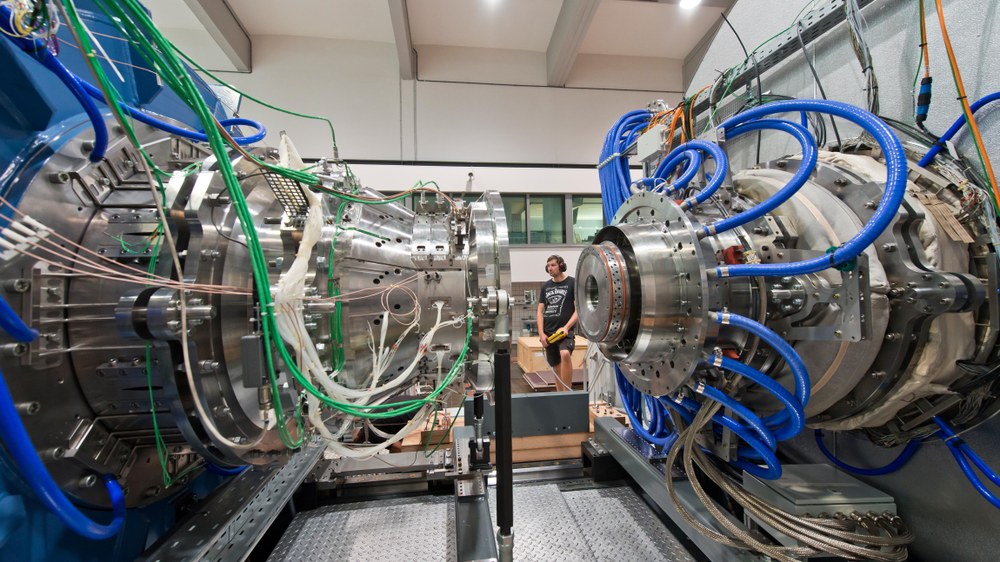
- DLR successfully tests turbines for environment-friendly aircraft
- Focus: Aeronautics
The foundations for a new generation of environment-friendly aircraft turbines have been successfully tested by the German Aerospace Center (Deutsches Zentrum für Luft- und Raumfahrt; DLR) at its site in Göttingen. The interaction between the combustion chamber and turbine was examined for the first time under realistic conditions in a new test rig.
The experiments were carried out within the framework of the EU project FACTOR (Full Aerothermal Combustor Turbine interactiOns Research), which aims to gain significant insight into the design of aircraft turbines. Turbines are the core element of aircraft engines. If their design is improved, the engine characteristics will improve substantially as well.
Interaction between cooling, flow and mixing of air
The FACTOR project investigates the complex interaction between the coolant system, the flows and the mixing of the air within aircraft turbines. The goal is to investigate and better understand, in particular, the effect of combustion chamber outflow, which can reach up to 1700 degrees Celsius, on turbine function. “To achieve this, we apply highly accurate measuring methods that are not suitable for use in a real engine under more tolerable temperatures and pressures in the test rig. This should not only reduce fuel consumption and pollutant emissions, but also improve the service life and optimise the maintenance costs of the turbine components", says Alexander Krumme from the DLR Institute of Propulsion Technology in Göttingen.
Hot gases and turbulent flow
The interface between the combustion chamber and the turbine presents major challenges for engine manufacturers – in addition to the very hot gases, there are also extremely turbulent air flows. Until now, these components have only been investigated separately – never together. But this is possible at the new 'Next-Generation Turbine Facility' (NG-Turb) at the DLR site in Göttingen, where the tests were carried out. "The innovation in FACTOR with regard to NG-Turb is the use of a combustor simulator in the inflow of the turbine combined with various pneumatic and optical measurement techniques using laser and infrared light", explains Alexander Krumme.
The NG-Turb test rig is among the most powerful international test facilities for aircraft turbines. The test rig is capable of analysing the turbines of modern aircraft in detail, from business aircraft to the A380. The goal is the development of environment-friendly and cost-effective aircraft engines. In addition, power plant turbines can also be investigated.
The test rig stands out, among other things, due to the air volume that can flow through the turbine – the so-called mass flow or volume flow. This is very high, at up to 10 kilograms per second, and consequently occupies a leading position worldwide. Furthermore, the pressure ratio of the associated compressor station is higher than that of nearly all comparable modern facilities.
International partners
The partners involved in the EU FACTOR project include Rolls-Royce, Siemens, MTU, ONERA, GE-Avio, as well as the universities of Oxford and Cambridge.