From hot to cold – solar researchers test new silicon oil under power plant conditions
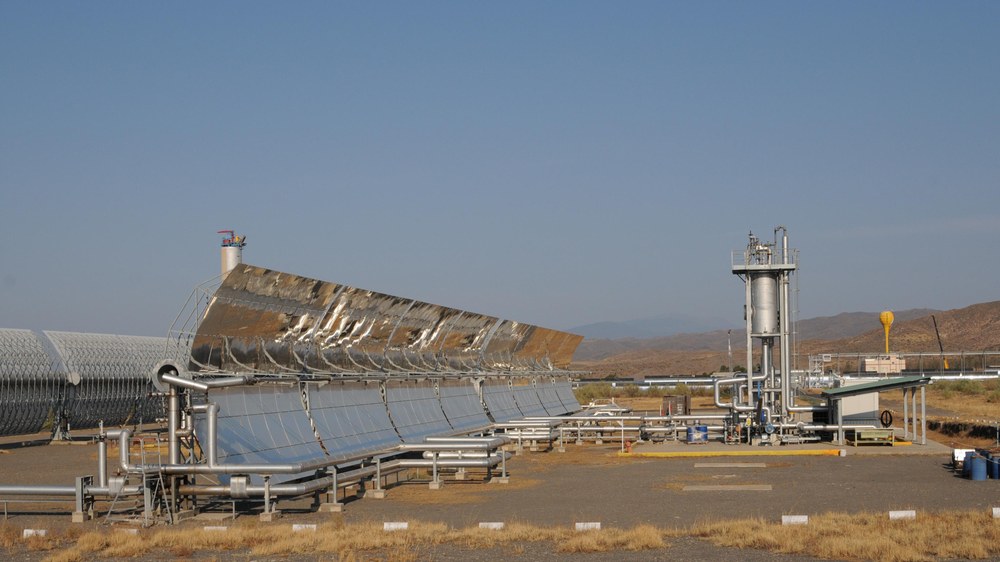
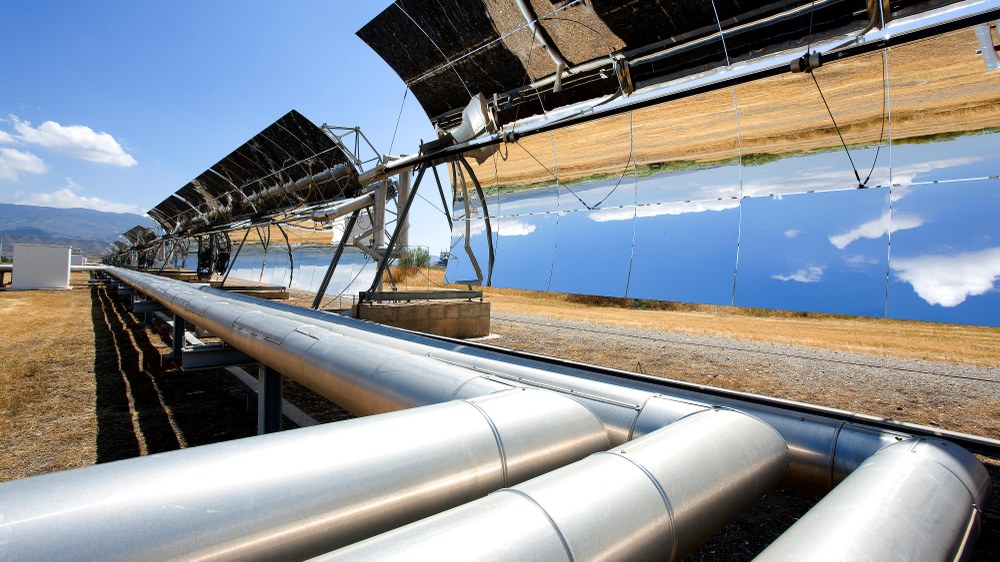
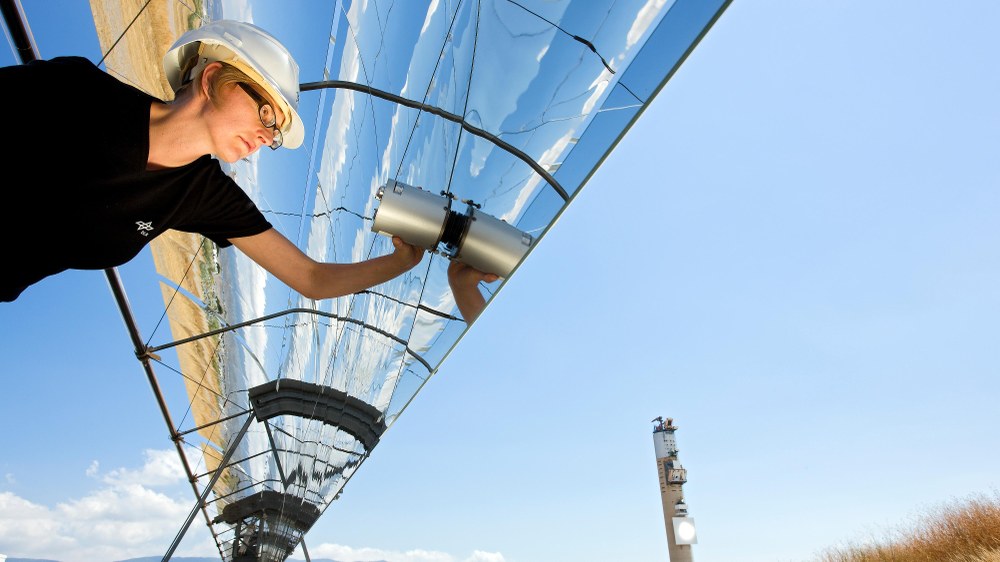
Solar thermal power plants play an important role for the energy transition, especially in regions of the world with a significant number of sun hours. When combined with a heat storage system they have the capacity to deliver electricity even after sunset. A consortium of researchers and industrial enterprises is currently working under the auspices of the German Aerospace Center (Deutsches Zentrum für Luft- und Raumfahrt; DLR) to increase the efficiency of solar parabolic trough power plants by improving the heat-carrier oils used in the absorber pipes. The viability of a newly developed silicon oil by Wacker Chemie AG is now being tested at temperatures of up to 425 degrees Celsius.
Parabolic trough power plants use U-curved mirrors that are arranged as collectors and track the passage of the sun during the day. Special absorber pipes filled with a heat-carrier oil are located in the focal line of each collector. The thermal energy acquired in this way is used to generate steam for the production of electricity or stored for downstream use.
Realistic testing
Scientists from the DLR Institute of Solar Research are currently using the PROMETEO test system at the Plataforma Solar de Almería (PSA) to test a silicon oil developed by the chemicals corporation Wacker AG at temperatures above 400 degrees Celsius as part of the SITEF (Silicon Fluid Test Facility) project. The heat-carrier oil HELISOL® 5A is being tested for the first time under realistic conditions and in its interaction with the various components of a parabolic trough power plant over a period of several months.
Before current test operations commenced, an industrially-financed demonstration at the same test facility already proved the operational stability of the oil up to 400 degrees Celsius. Moreover, the stability of the silicon oil has also already been tested to 425 degrees Celsius but under laboratory conditions. Now the time has come for its large-scale deployment within the SITEF project.
A characteristic feature of the new heat carrier is its substantially greater flexibility in the lower temperature range. The solidification point lies at around –55 degrees Celsius, meaning that additional heating systems to protect the heat-carrier fluid from the cold are almost certainly unnecessary with this heat carrier. Silicon-based heat-carrier oils are better than organic biphenyl/diphenyl oxide (BP/DPO) blends with regard to their ageing characteristics and the adverse side-effect of hydrogen formation as well. What's more, heat-carrier oils on a silicon basis do not emit any carcinogenic or otherwise dangerous substances like benzene and hence contribute to a more sustainable and even safer operation of these facilities.
Background
Water already evaporates at approximately 100 degrees Celsius at ambient pressure. If water is used as the heat carrier, instead of oils or molten salt, the pressure in the absorber pipes must be particularly high to prevent the water from forming steam. This requires a more sophisticated technical system. Accordingly, special thermal oils and, in future, molten salts will be more commonly used.
Heat carriers have to fulfil high demands. They must withstand extreme temperatures without showing any chemical decomposition. It is also extremely beneficial if they remain fluid at low temperatures. The latter ability is extremely advantageous in sunny regions of the Earth where the ambient temperatures vary substantially over the course of the day and the year, and may often fall below the freezing point of water.
The heat-carrier oil commonly used in current parabolic trough power plants is a blend of biphenyl and diphenyl oxide (BP/DPO), which shows the highest thermal resistance of all organic heat carriers. This oil mixture can be used at temperatures of up to 400 degrees Celsius, but solidifies at below 12 degrees Celsius. Temperature-associated solidification of heat carriers can have particularly severe ramifications in ongoing power plant operations, as a solidified oil can block or even damage pipes.
To prevent thermal solidifaction sophisticated heating systems, which are expensive to operate, must be installed to continue pumping the oil through the kilometres-long hermetic system of pipes through the facility. Although the oil is heated to around 400 degrees Celsius in regular operations, the parabolic trough collectors do have the capacity to achieve higher temperatures. Operating at higher temperatures would be advantageous for the heat storage process and the conversion into electricity, as it would increase the facility's overall efficiency and energy yield.
Besides DLR as the project coordinator and Wacker Chemie AG, the industrial project partners are TSK Flagsol, TÜV NORD and Senior Flexonics GmbH. The associated partners are innogy SE and Rioglass Solar. On the research side, the Spanish organisation CIEMAT (Spain) (Centro de Investigaciones Energéticas, Medioambientales y Tecnológicas) – owner of the PROMETEO test facility – has contributed to improving the efficiency of solar power plants over two decades in cooperation with DLR.
Funded by the Federal Ministry for Economic Affairs and Energy (BMWi), the primary aim of the project is to increase efficiency and simultaneously lower the operating costs of parabolic trough power plants.