The future of space transport: Will large satellite networks change our way into space?
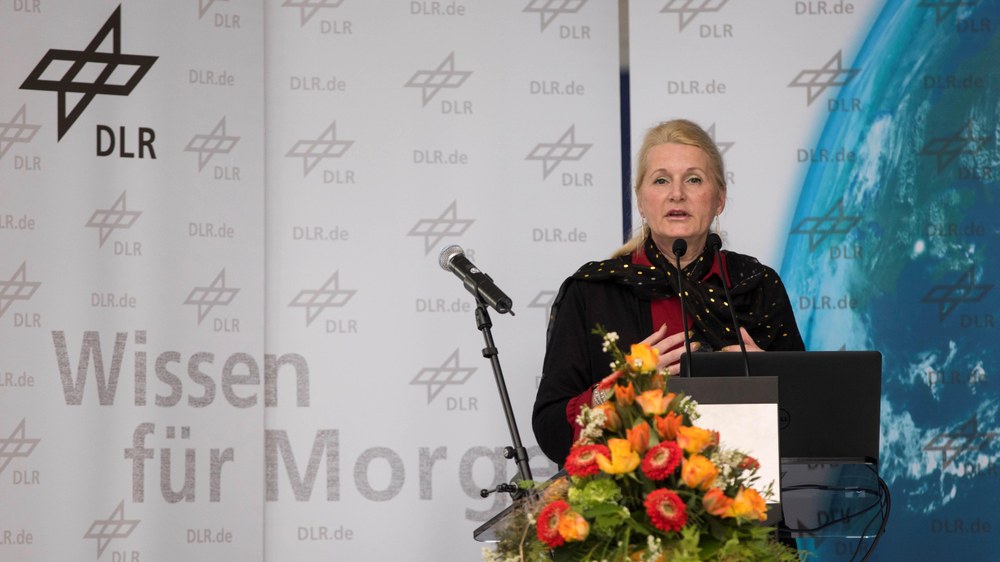
- On 11 and 12 April 2017, within the framework of the 5th Industrial Days, leading space travel representatives met at the German Aerospace Centre (DLR) site in Lampoldshausen.
- Approximately 100 experts from space agencies, industry and science exchanged views on the future of European space transport.
- This year's focus is on current and future developments in the field of LOX / methane technology.
The importance of global networks for the aerospace sector has grown enormously. Increasingly widespread digitalisation and the spiralling volume of data generated are redefining the requirements for the space sector. Plans for a long-term expansion of large satellite networks as the basis for a global communication system are becoming more and more apparent. In future, the operation and use of satellite networks in Low Earth Orbit (LEO) will enable a broad range of uses, such as Earth observation or disaster management. Are our launch vehicles ideally suited for building these new satellite infrastructures? And what are the requirements and technical consequences for European launcher systems? Senior representatives from space agencies, industry and science gathered at the Lampoldshausen site of the German Aerospace Center (Deutsches Zentrum für Luft- und Raumfahrt; DLR) from 11– 12 April 2017 for the 5th Industrial Days to discuss the future of European space transport.
Rethinking space
The European launchers, Ariane, Vega and Soyuz, are among the most reliable systems on the global market. But digitalisation and networking are increasingly changing the way in which space is used – and these changes are already noticeable in the area of space transport. "Now, more than ever before, it is essential to take a critical look at the underlying principle behind our proven launcher systems. The innovative, core principle is individual space transport that is designed to better preserve resources," said Pascale Ehrenfreund, Chair of the DLR Executive Board, summarising the transformation precipitated by a digital world, adding: "The launchers of the future require a greater focus on market-oriented objectives: they must include innovation from other industries, be application - and customer oriented, as well as rapidly available."
The road to Ariane 6 and beyond
Competitive and reliable, high-performance and flexible – these adjectives best describe the Ariane launcher family that will now be expanded accordingly with the addition of Ariane 6. Airbus Safran Launchers, prime industrial contractor for the Ariane 6 programme, has now reached the key milestones: firstly, technical maturity of the launcher system has been confirmed, and secondly, the European Space Agency (ESA) has now signed an addendum to the original Ariane 6 contract, releasing the necessary funds to complete development and industrialisation. The reduction in actual costs for launching without restricting the launcher's reliability is of particular significance in this respect. Moreover, performance and cost-efficiency of Ariane 5 will be further improved as a means of prevailing in an increasingly competitive market. Starting in 2023, Ariane 6 is scheduled to launch up to 12 times per year and replace the current Ariane 5 system.
The main actors within the European aerospace sector have their eyes firmly fixed on the commissioning of Ariane 6. Moreover, Europe is already actively preparing a future launcher system: the CoRoT Special, Airbus Safran Launchers and DLR are collaborating within the Prometheus Project to develop a cost-efficient, high-thrust and reusable rocket engine powered by liquid oxygen (LOX) and methane. Numerous projects around the world have investigated the use of methane as a rocket fuel for decades. But so far the LOX/methane propulsion system has not been used in any real launcher. Since the 2016 ESA Council at Ministerial Level, the committee that oversees European space policies, however, the research and technology development of the Prometheus project have been included in the ESA Future Launchers Preparatory Programme (FLPP).
Research for the adoption of new technologies
A fuel combination comprising methane and liquid oxygen has an auspicious role to play in the development of new liquid rocket fuels for space. The potential options of methane extend from adding it to the current liquid fuel engines used in the Ariane launchers, to a complete replacement of liquid hydrogen. DLR engineers in the Prometheus project are now working on developing the LOX/methane technology as quickly as possible for use within the European space programme. The targets are clearly defined: Airbus Safran Launchers and the DLR Institute of Space Propulsion entered into an alliance in 2016 to drive rapid progress in LOX/methane technology. While the engineers at Airbus Safran Launchers designed and built a promising technology demonstrator, the DLR engineers adapted the P3 test rig to suit these entirely new conditions, especially with regards to the fuel supply. The project partners then conducted a 12-month test campaign that yielded important findings for the continued development of necessary, critical technologies such as the combustion chamber. "Our test campaign has paved the way for the development of innovative LOX/methane technology," explained Gerald Hagemann, Head of Liquid Propulsion Engineering at Airbus Safran Launchers. Upon completion of a test campaign with Vulcain 2.1 – the main stage engine of the Ariane 6 rocket – the aim is to run tests on a LOX/methane technology demonstrator with 100 tons of thrust under representative conditions on the P5 test rig at the DLR Test Centre for Rocket Propulsion Systems in Lampoldshausen. This LOX/methane engine has the potential to reduce the costs of the Vulcain main stage propulsion system, developed by Europe in the 1980s, by a factor of 10.
DLR Lampoldshausen Test centre – Backbone of European space transport
"DLR Lampoldshausen contributes its unique expertise as a European test and development site for all liquid space propulsion systems to the research into LOX/methane technology," emphasised Stefan Schlechtriem, Director of the DLR Institute of Space Propulsion. The ground-breaking expansion and research activities are decisive to Lampoldshausen remaining the European test centre for all liquid space propulsion systems within the current alliances, also beyond the development of the Ariane 6 rocket. "In addition to operation of the test rigs, our future at DLR Lampoldshausen will lie in providing system competency," added Schlechtriem. For example, the research objectives in the new DLR project LUMEN are to be expanded from the component level to the system level of an entire propulsion system. The LUMEN project involves the development of a pump-operated LOX/methane engine, which will then be transferred to the European research and technology P8 test rig for downstream testing. "Together with our project partners at Airbus Safran Launchers and CNES, we are acquiring data that we can make available to the engine developers at an early stage," said Schlechtriem to explain the expansion of research activities. And the goals are no less ambitious for the operation of major test rigs: "We are preparing a concept for efficient and optimised use of the test rigs, which will employ digitalisation and technologies already used in Industry 4.0. Aspects such as flexibility, fuel supply, data processing, quality and occupational safety are the main considerations in this respect. Here, long-term success will be predicated on the capability to respond quickly to change," Schlechtriem added.
DLR in Lampoldshausen for over 55 years
DLR operates unique test rigs and systems to test rocket engines at its site in Lampoldshausen. These facilities are of crucial importance for European aerospace. They cover the entire portfolio of test requirements – from component and engine tests, to the testing of entire rocket stages. The test site is used for research and development experiments, as well as for conducting qualification and characterisation tests.
The test rigs simulate the rocket in order to provide the greatest possible similarity to actual in-flight conditions during testing. Suitable interfaces supply the engines with all fuels and fluids in stages. The test systems measure the data, and control, regulate and monitor the test objects during ongoing operations. The test rigs can also create specific environmental conditions as required. Satellites and upper stage engines are tested in a vacuum during the so-called altitude simulation. The extremely hot and fast-moving engine exhaust fumes are directly extracted and discharged in a controlled manner via a specially-designed system to ensure that the engine itself can be operated continuously in a simulated space environment.
Research is conducted on a variety of scales, ranging from laboratory combustion chamber investigations to tests under conditions that can be considered representative for stage propulsion systems like Vulcain 2.1 and Vinci. This is made possible by the infrastructure at the site – the only one of its kind in Europe – and the available expertise in designing and testing research combustion chambers. "New technologies can therefore be verified under representative conditions," explains Schlechtriem. "Our research and test activities hence make a decisive contribution to the future of European space transport."