DLR at JEC World 2017 in Paris
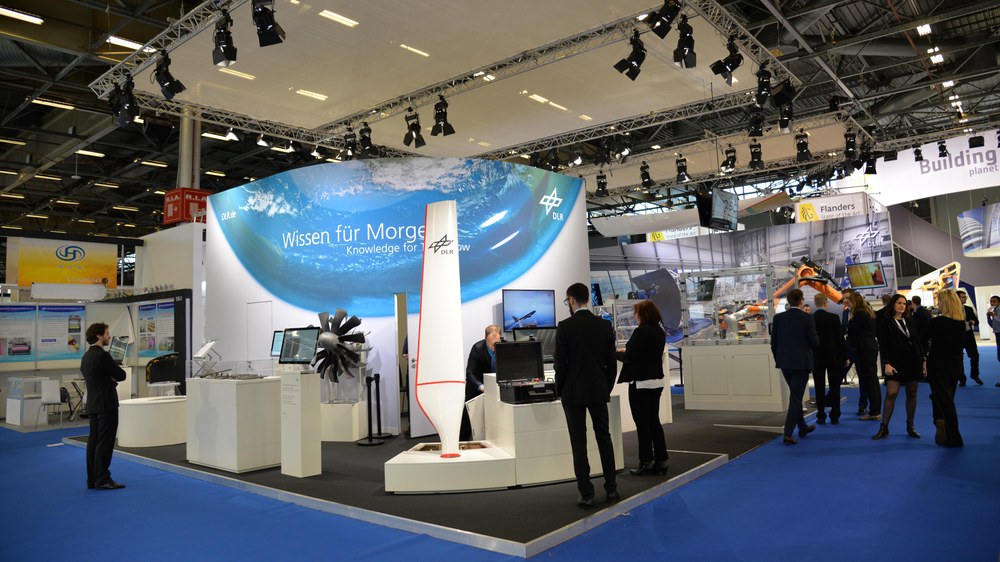

- The DLR stand at JEC World 2017 gives a glimpse of current research projects in the area of fibre-reinforced high-performance plastics and lightweight construction.
- In addition to exhibits from research companies, live demonstrations show the technologies in practice.
- The DLR stand can be found in Hall 5a, E59 and D63.
From 14-16 March 2017, the German Aerospace Center (Deutsches Zentrum für Luft- und Raumfahrt; DLR) is presenting current research projects in the field of fibre-reinforced high-performance plastics at JEC World in Paris, the leading European trade fair for fibre composite construction. This year, the joint presentation of the DLR Institute of Structures and Design, the DLR Institute of Composite Structures and Adaptive Systems and the Center for Lightweight Production Technology (ZLP), located in Augsburg and DLR Center for Lightweight Production Technology, focuses on innovative technologies for the efficient production of composite fibre components. At the approximately 120-square-metre DLR stand, located in Hall 5a (E59 and D63), scientists are explaining and demonstrating a wide range of applications, particularly in the field of aerospace.
Thermoplastic components – automated welding
Fibre-reinforced thermoplastics components are increasingly being used in aeronautics, for example, in order to connect structural components to one another, such as frames and stringers. Thermoplastics are special high-performance plastics that can be thermoformed and welded. Welding yields a very strong, flat and tight connection and at the same time has a high automation potential, which is indispensable for mass production. In a live demonstration, researchers from the DLR Institute of Structures and Design and the Center for Lightweight Production Technology will be demonstrating a fully automated joining process in which carbon fibre reinforced corners are applied to a flat composite sheet. For this, an electric resistance welding process is used: an electrically conductive welding element generates the heat required to melt the thermoplastics directly in the joining section while the components to be joined are compressed together.
Automated fuselage shell production for the short-haul aircraft of tomorrow
So-called fibre metal laminates (FML) – a combination of thin aluminium sheet and glass fibre fabric – have great potential for short-haul aircraft in the near future. Compared to pure aluminium, they have much better structural properties. Currently, the production of structures from this composite material is still largely carried out by hand. The DLR Center for Lightweight Production Technology in Stade is therefore working on the ProfiRumpf project to automate the production of FML components and make the process more efficient and economical. In addition to technologies for quality assurance, a live exhibit will show how automation using mobile robot units can be made even more flexible in the future.
Flex-in Heat: plaster for high-tech plastics
Low weight and high strength – these properties characterise structures made of fibre-reinforced plastics (FRP). They are therefore increasingly used in aviation and automotive engineering. Following this development, suitable repair concepts are becoming increasingly important. To make FRP structures more competitive and economically more interesting, scientists from the DLR Institute of Structures and Design have developed a novel repair concept: It is flexible, efficient, material-appropriate and extends the utilisation phase of these structures. The central element is a flexible induction heating system that precisely and homogeneously heats only the area of the repair patch. Under pressure and heat, this 'plaster' then bonds with the surrounding structure. The Mobile repair station being showcased at the DLR stand contains all the necessary equipment, and demonstrates the procedure.
Pressure tank for space mission Eu:CROPIS
When the Eu:CROPIS satellite is launched to space in September 2017, it will carry a very special payload: Two greenhouses in which tomatoes will grow under environmental conditions such as may be found in Lunar or Martian habitats. The DLR Institute of Composite Structures and Adaptive Systems has developed the necessary pressure tank made of carbon fibre reinforced plastic (CFRP). Its special feature is that it holds the payload and guarantees the impermeability required for the experiment over the entire two-year mission. At the same time, the container is protected by a special protective layer (whipple shield) against the impact of microparticles.
Successful DLR spin-off at the JEC Startup Booster
As one of the world's ten startup companies, COPRO Technology, a spin-off from the DLR Institute of Composite Structures and Adaptive Systems, is presenting itself at the JEC Startup Booster. For the first time, young companies can present their innovations to international investors and users. COPRO Technology specialises in particularly efficient and flexible processes for the industrial production of profiles made of composite materials, which can be used to improve quality and reduce costs and waste.
Other exhibits at the DLR stand provide insights into the fully automatic, pre-contour preform production of aircraft frames, a crash absorber concept for CFRP fuselage structures based on progressive perforation failure and a lightweight construction counter-rotating rotor that can make the next generation of aircraft engines more efficient and quieter.