ProfiRumpf - Produktionstechnologie für Leichtbaustrukturen aus Faser-Metall-Laminaten im Flugzeug-Rumpf
Die Arbeitsinhalte des DLR lassen sich wie folgt zusammenfassen:
Das Arbeitspaket Gesamtprozess beinhaltet die Zusammenführung der Einzeltechnologien für die automatisierte und qualitätsgesicherte Fertigung FML-Bauteilen und alle dazu nötigen Vorbereitungen sowie die Identifikation von Optimierungspotenzialen in der Gesamtprozesskette.
Die Handhabung der Aluminiumfolien zum Aufbau der Preform ist das Ziel des Arbeitspaktes Aluminiumablage. Dafür soll ein Greifsystem konzipiert und aufgebaut werden, welches flexibel und skalierbar beliebige Geometrien und Größen abdecken kann. Die Handhabung der Aluminiumfolien erfolgt mit zwei kooperierenden Robotern. Der zu entwickelnde Prozess beinhaltet auch Logistik und Transfer der Zuschnitte (Aufnahme, Transport, Ablage). Besonderes Augenmerk liegt auf der Integrierbarkeit in den Gesamtprozess und eine Absicherung durch sinnvoll gewählte Maßnahmen zur Qualitätssicherung (QS), die im AP 3.4 Prozessüberwachung und Prozessanalyse der Fertigung von FML-Bauteilen detailliert beschrieben werden.
Im Arbeitspaket Neuentwicklung & Darstellung der Ablege und Aushärteprozesskette wird unter anderem die automatisierte Ablage des Glasfaserprepregmaterials mit den Fertigungstechnologien Automated Tape Laying (ATL) und Automated Fiber Placement (AFP) hinsichtlich Verarbeitbarkeit, Genauigkeiten sowie Ablegestrategien untersucht. Weiterhin erfolgt im Anschluss die Herstellung von zwei Fertigungsdemonstratoren mit doppelt gekrümmten Bauteil-geometrien, wodurch die Einsatzfähigkeit der Technologien für diesen Anwendungsfall nachgewiesen wird.
Die ablegte und versteifte FML-Haut wird anschließend in einem simulations- und sensorgestützten Aushärteprozess (One-Shot-Bonding-Verfahren) zu einem Panel zusammengefügt.
Innerhalb des Arbeitspaketes Prozessüberwachung und Prozessanalyse der Fertigung von FML-Bauteilen erfolgt die Konzepterstellung und Umsetzung eines Inline Qualitätssicherungskonzeptes für die Aluminium- und Glasfaserprepregablage sowie für den Aushärtungsprozess. Diese Arbeiten beinhalten ebenso die in-situ Erfassung der Verformung, Dehnung und Topografie des FML-Aufbaus zur Ableitung einer Methode zur Bestimmung von Eigenspannungen.
Während für die Einzelschritte im Fertigungsprozess von FML-Bauteilen eine Inline-QS entwickelt und integriert wird, wird das Endbauteil zerstörungsfrei geprüft. Hierbei steht die automatisierte Auswertung der erhobenen Messdaten im Fokus der Arbeiten, das die bisherigen manuellen Aufwände wesentlich reduzieren soll.
Im Arbeitspaket Werkstoffmechanische Charakterisierung werden FML-Varianten mit biaxialer Prüfung auf Coupon-Ebene hinsichtlich deren Blunt-Notch Festigkeiten untersucht, um hieraus Designkriterien für Nietverbindungen im Flugzeugrumpf ableiten zu können.
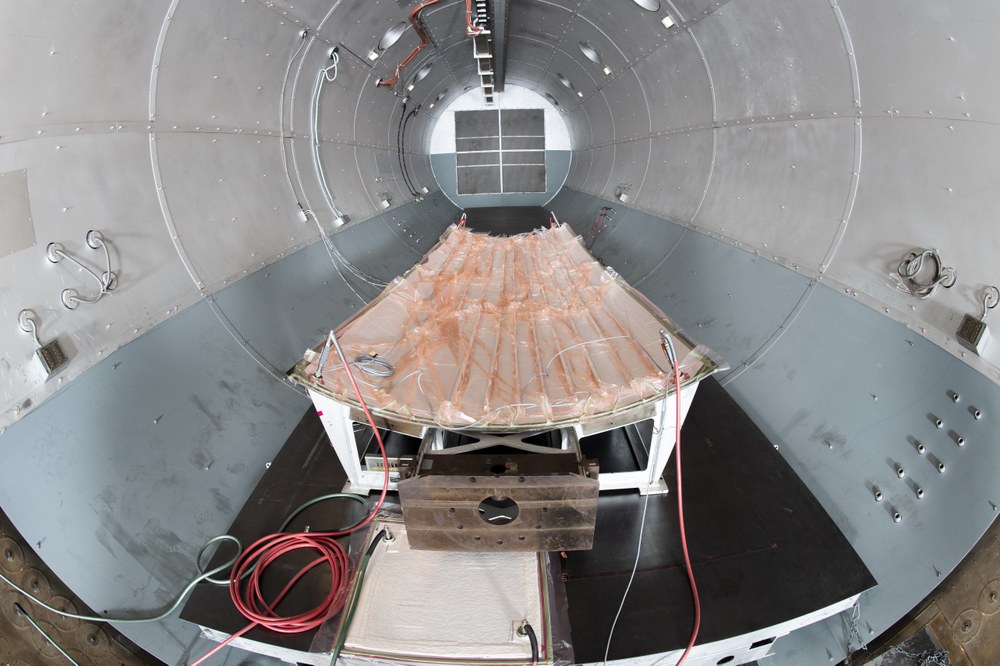
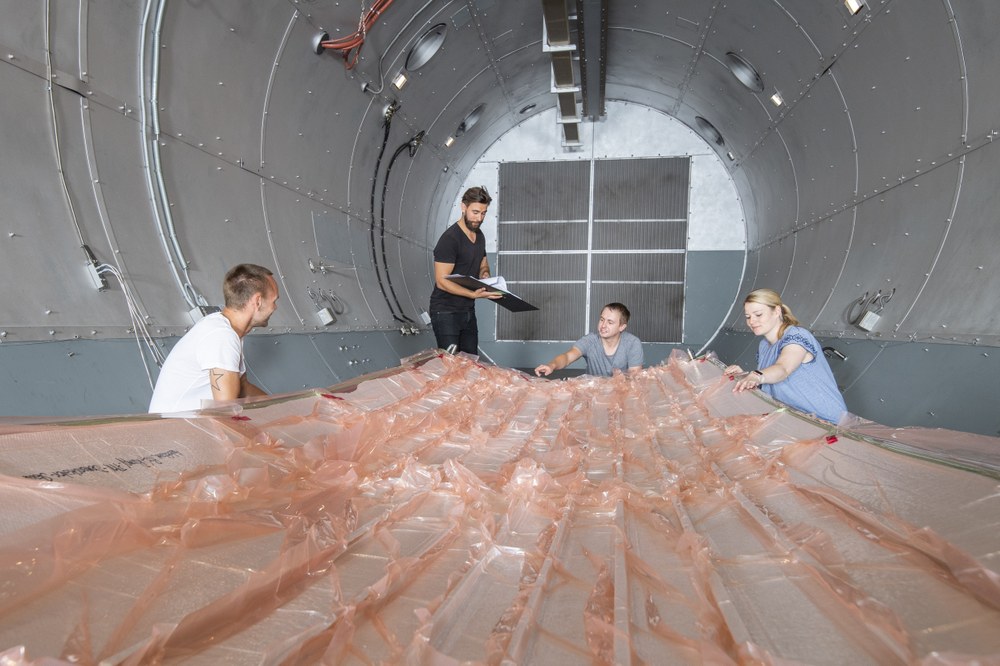
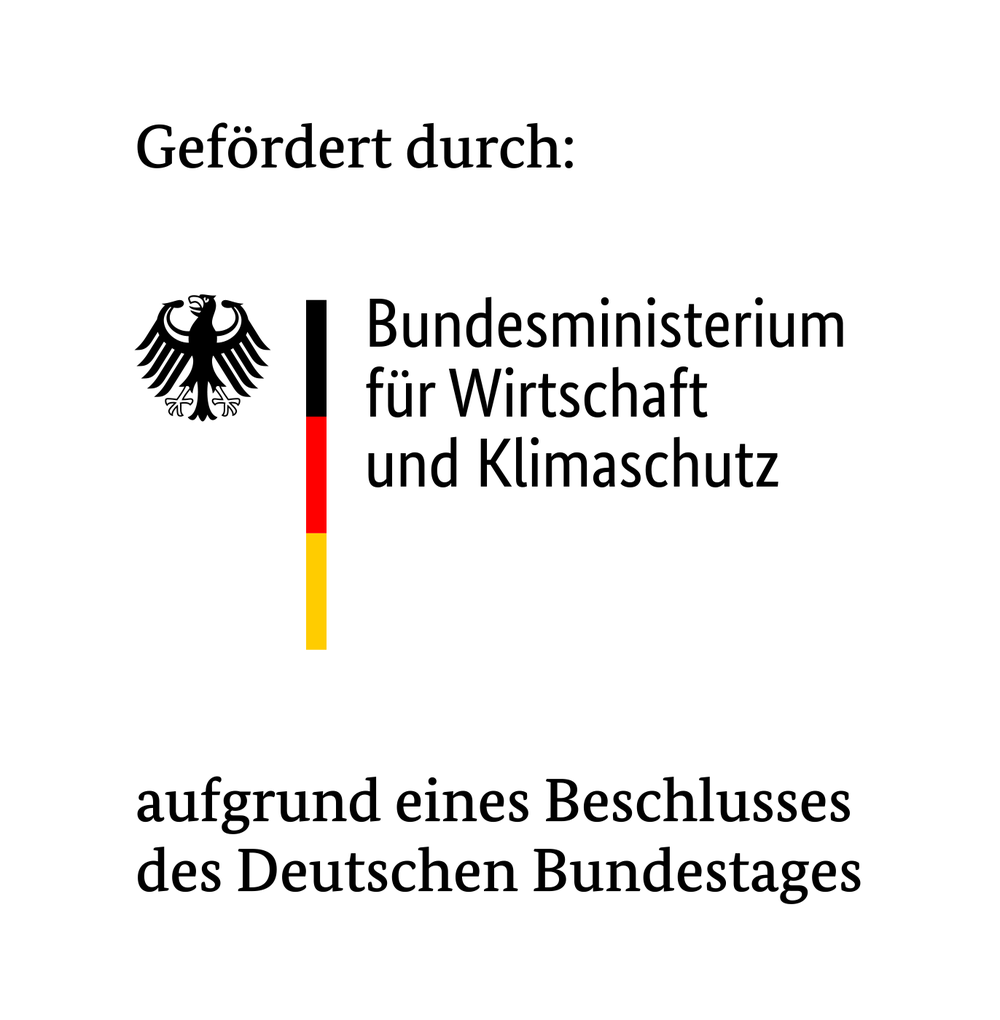
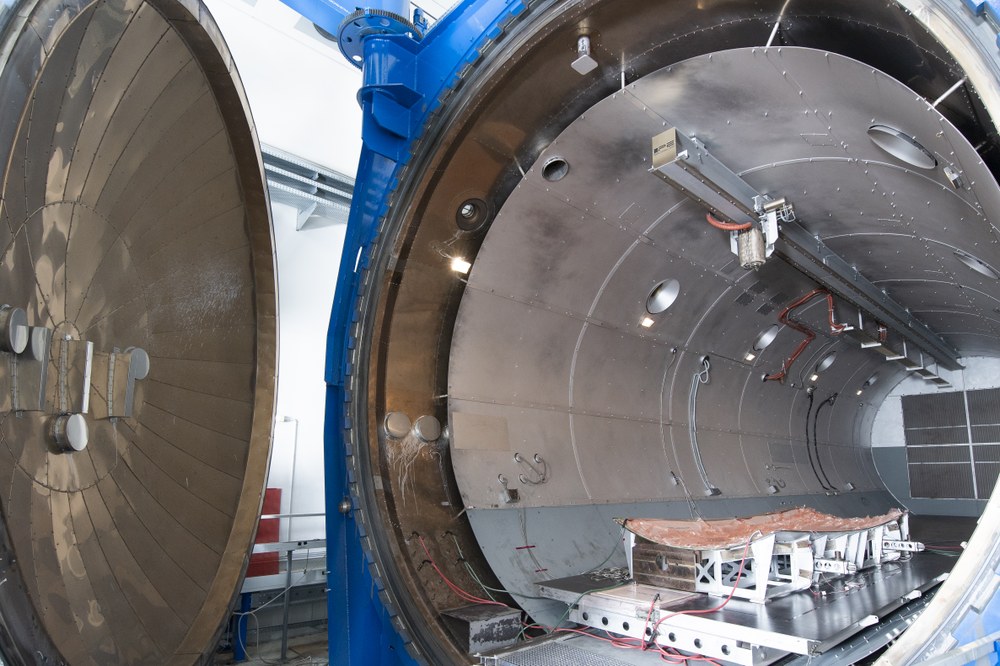
Projekt ProfiRumpf
Für die Wiedergabe dieses Videos auf Youtube.com ist Ihre Zustimmung zur Speicherung von Daten ('Cookies') erforderlich. Unter Datenschutz-Einstellungen können Sie Ihre Wahl einsehen und verändern.