STORT
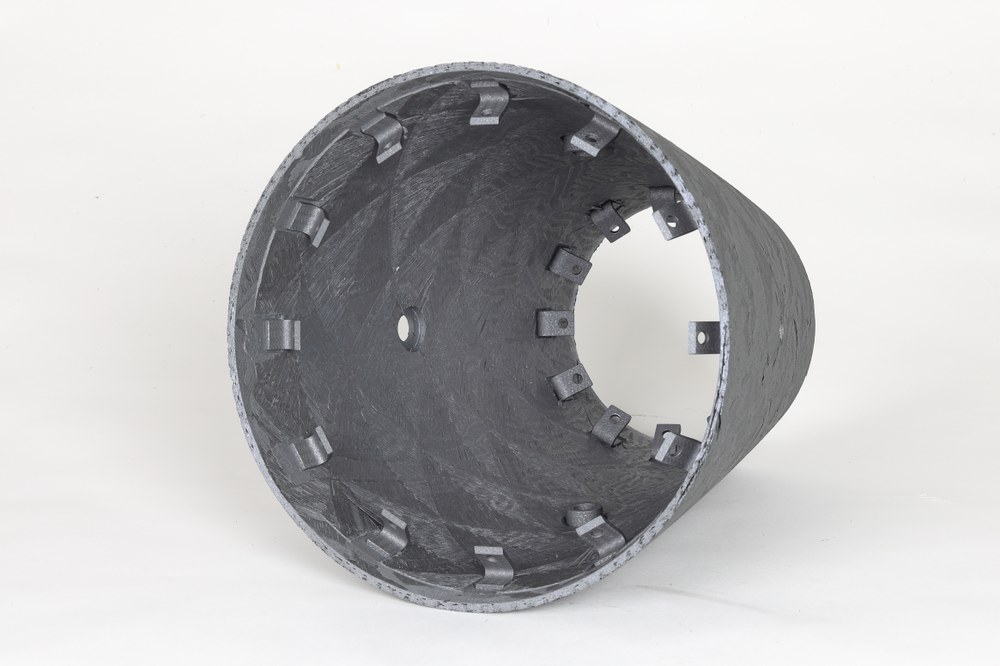


Reducing costs while maintaining reliability is one of the main requirements for future space transport systems. In addition to new and more efficient manufacturing and qualification methods, reusability is a key element in achieving this goal. Since one of the most cost-intensive elements of launch vehicles is the first stage, further optimisation of the cost-effectiveness of this stage is of great importance. One of the possibilities is the reusability of this stage. The latest studies show that in the case of reusability, the first stage must be separated and returned at higher Mach numbers (between 8 to 10) than previously. The reusability of upper stages poses an even greater thermomechanical challenge.
The "STORT" project is part of DLR's key program for reusable space transport systems. The aim of the project is to develop specific technologies and methods for the thermomechanical analysis and evaluation of launcher systems. To this end, the component structures, measurement methods and evaluation algorithms developed in basic studies are adapted for a flight experiment and finally tested in flight. In particular, while previous and other ongoing DLR funded projects for flight experiments concentrate on short-term high-speed flights or on aerodynamics and control at Mach numbers below 5, the focus of the STORT project is on the thermal management of thermally highly stressed components at high Mach numbers (over 8) over a relatively long period of around 2 minutes. In order to achieve the desired high Mach numbers, a three-stage flight configuration developed by DLR is flown for the first time in STORT.
As part of the STORT project, our Institute of Structures and Design, with its "Space Systems Integration" and "Ceramic Composites and Structures" departments, is responsible for the design and manufacture of the rocket's forebody structure, which in the mentioned severe flight conditions becomes of extreme importance. For relatively long exposition times, as in the case of STORT, this requires the design of a suitable thermal protection system (TPS) with use of high-temperature resistant ceramic matrix composite (CMC) materials.
For the thermal management experiments, the researchers also used three permanently installed canards with CMC outer shells developed by our institute on the rocket. One canard was actively cooled, a second was passively cooled and the third canard, which served as a reference, was not cooled and was used to investigate the shock wave - boundary layer interaction. In flight, all three canards showed different structural reactions when exposed to the same aerothermal load.
Finally, a module of the rocket made entirely of CFRP is developed at our institute, integrated and tested in flight for the first time, in order to validate the technology, enabling a significant mass reduction.
In the early morning of 26 June 2022, the three-stage rocket experiment took off from the Andøya Space launch site in northern Norway. The upper stage reached a flight speed of around 9,000 km/h at the apex of the trajectory at an altitude of 38 km, which corresponds to a Mach number of over eight. It then fell into the Atlantic Ocean more than 350 km from the starting point. The extensive measurement data was transmitted to the ground station during the flight.
![Video (engl.): Andoya Space - DLR STORT [Launched]](/de/vorschaubilder-logos-platzhalter/vorschaubilder-videos/2022/standbild-andoya-space-dlr-stort-launch/@@images/image-1000-55bc6902d0998025ffb901c6488c9f16.jpeg)
Video (engl.): Andoya Space - DLR STORT [Launched]
Your consent to the storage of data ('cookies') is required for the playback of this video on Youtube.com. You can view and change your current data storage settings at any time under privacy.
YouTube/Andoya Space