Prüfstand-Profis
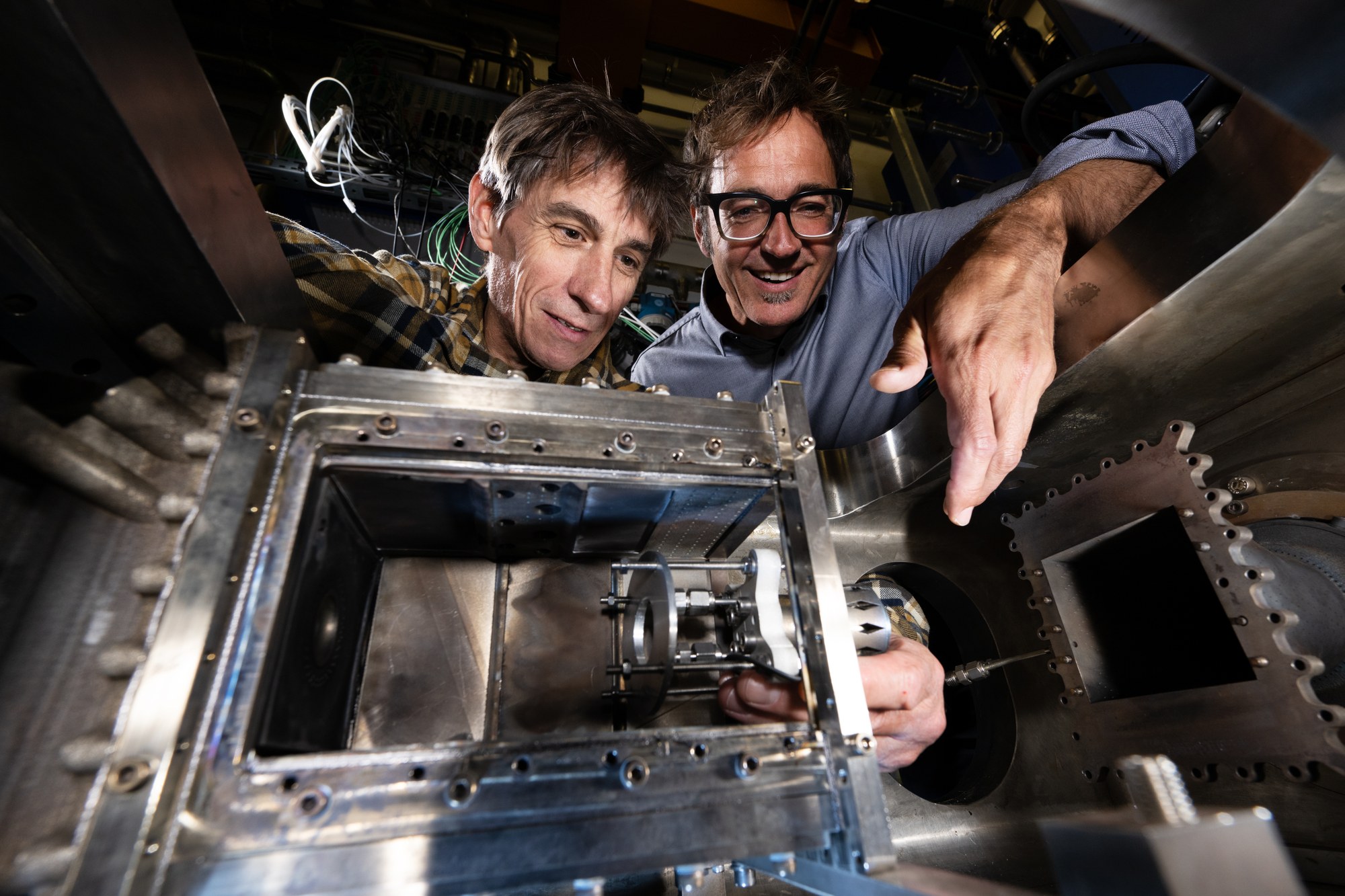
Für eine klimafreundliche Luftfahrt bietet Wasserstoff enormes Potenzial. Anders als bei Kerosin entstehen bei seiner Verbrennung nur Wasser und Wärme … zumindest theoretisch. Allerdings hat ein solcher Treibstoff auch seine Herausforderungen: Damit der Wasserstoff flüssig bleibt, muss er stets auf Minus 253 Grad Celsius gekühlt werden. Auch verbrennt Wasserstoff anders als Kerosin. Wie genau dieser potenzielle neue Flugzeugtreibstoff sicher und schadstoffarm verbrennen kann, untersuchen die Forscherinnen und Forscher des DLR-Instituts für Antriebstechnik in Köln. Dazu nutzen sie moderneHochdruckbrennkammerprüfstände in Kombination mit moderner laseroptischer Messtechnik. Warum diese Technik so gefragt ist, darüber sprechen Dr. Bertram Janus, kommissarischer Co-Institutsleiter und Leiter der Abteilung Brennkammer, sowie Dr. Christian Willert, Leiter der Abteilung Optische Triebwerksmesstechnik, in diesem Gespräch.
Welche Flugzeugklassen sollen denn in Zukunft mit Wasserstoff betrieben werden?
Dr. Bertram Janus: Das gilt es derzeit noch zu bewerten. Unser Verständnis davon, was die einzelnen Technologiezweige leisten können, wächst stetig. Denn es gibt unterschiedliche Ansätze für ein klimaverträglichesPassagierflugzeug: Bei Kurzstrecken liegen die Erwartungen eher im Bereich „elektrisches Fliegen“. In diesem Zusammenhang wird auch an hybriden Ansätzen mit Wasserstoff als Energieträger geforscht.
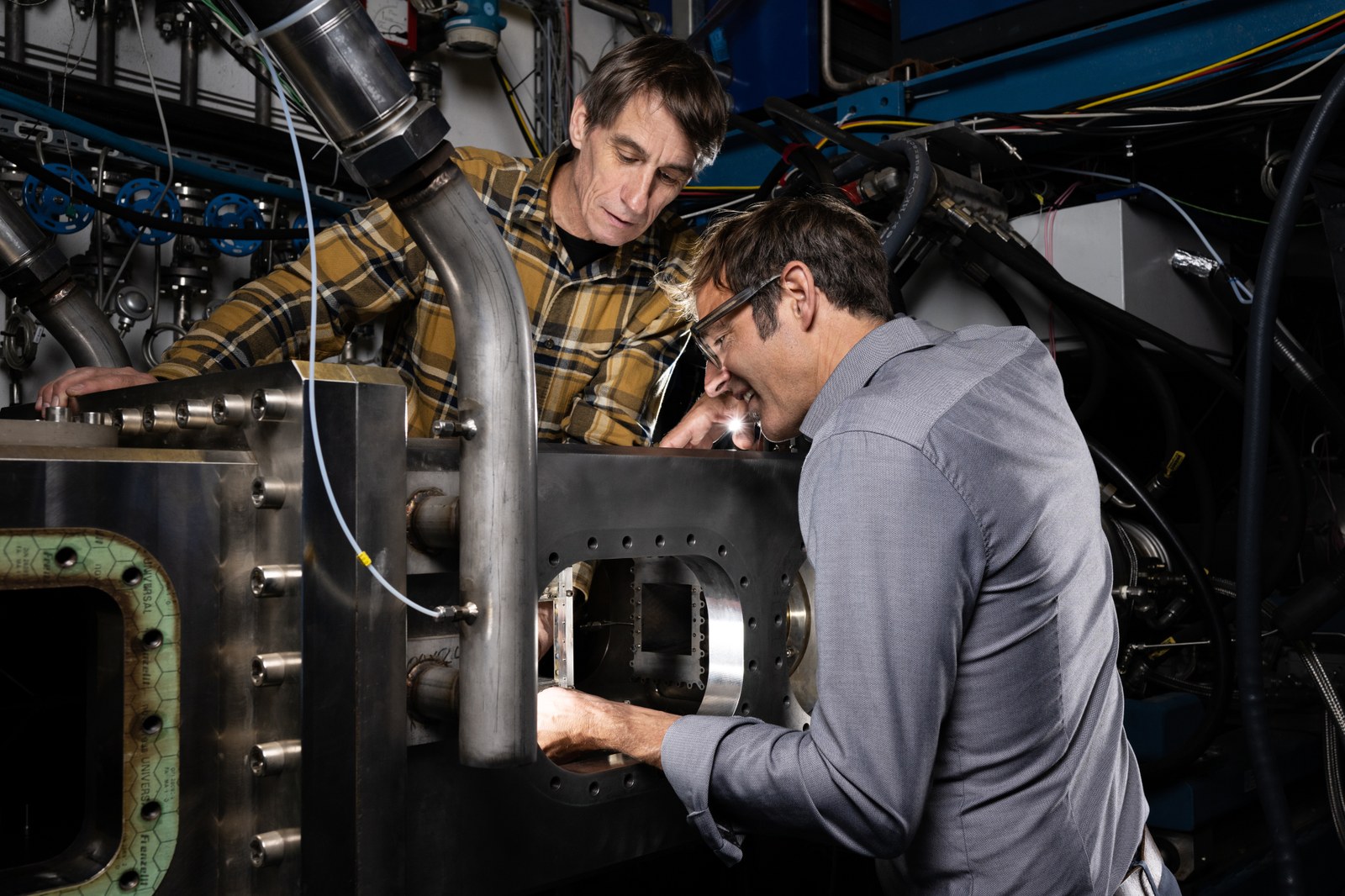
Dieser wird dabei aber nicht in einem Triebwerk verbrannt, sondern in einer Brennstoffzelle in Strom umgewandelt. Damit wird der Propeller angetrieben. Wir hingegen forschen an der direkten Verbrennung von Wasserstoff in konventionellen Flugzeugtriebwerken für die Mittelstreckenklasse. Hier wird momentan das größte Potenzial für den verbrennungsbasierten Wasserstoffbetrieb gesehen. Deshalb kooperieren wir mit verschiedenen Triebwerksherstellern, die aktuell Demonstratoren entwickeln. Die aktuellen Versuche am DLR konzentrieren sich auf eine Triebwerksklasse für Business Jets.
Airbus will bis 2035 das weltweit erste wasserstoffbetriebene Verkehrsflugzeug entwickeln …
Janus: Richtig. Der Flugzeughersteller plant zunächst eine Technologiedemonstration am Boden und später auch in der Luft. Dazu möchte er ein modifiziertes Triebwerk an einen Airbus A380 montieren, um zu zeigen, dass ein Wasserstoffantrieb grundsätzlich möglich ist. Gleichzeitig können Untersuchungen zur Klimawirkung durchgeführt werden. Das ist ein großer Meilenstein auf dem Weg zu einem wasserstoffbetriebenen Flugzeug. Die großen Triebwerkshersteller, mit denen wir in verschiedenen EU-geförderten Projekten zusammenarbeiten, unterstützen diesen Weg. Und bei uns am DLR in Köln finden die vorbereitenden Verbrennungstests statt.
Bis 2035 soll das Wasserstofftriebwerk den Weg in die zivile Luftfahrt finden. Welche Hürden müssen bis dahin noch genommen werden?
Janus: Das erste Zwischenziel sind Triebwerksdemonstratoren auf dem Boden. Hierzu laufen Versuche in unseren Prüfständen, bei denen wir die Verbrennung von außen durch ein Fenster beobachten können. Wir lernen, das Verhalten des Brenners und der Brennkammer besser zu verstehen, und beseitigen grundsätzliche technische Unsicherheiten. Sobald ausreichend Vertrauen in den Brenner besteht, folgen anwendungsnähere Experimente in größeren, komplexeren Prüfständen, wo ganze Ringbrennkammern untersucht werden können – unter Bedingungen, die denen eines realen Triebwerks entsprechen. Nach weiteren erfolgreichen Tests baut der Triebwerkshersteller den Brenner dann in ein Triebwerk ein.
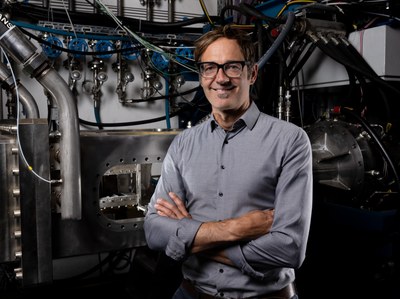
Wir lernen, das Verhalten des Brenners und der Brennkammer besser zu verstehen, und beseitigen grundsätzliche technische Unsicherheiten.
Warum werden die Versuche beim DLR gemacht und nicht bei der Industrie? Was kann das DLR, das die Privatwirtschaft nicht kann?
Janus: Mit den Hochdruckbrennkammerprüfständen wie dem Hochdruckbrennkammerprüfstand 1 (HBK1) stellen wir der Industrie eine außergewöhnliche Infrastruktur zur Verfügung. Beispielsweise erlauben druckfeste Quarzglasfenster spezielle Einblicke in die eigentlich geschlossene Brennkammer. So können wir das Verbrennungsverhalten charakterisieren und die Strömunginnerhalb der Brennkammer bestimmen. Dafür setzen wir eigens entwickelte laseroptische Messverfahren ein.
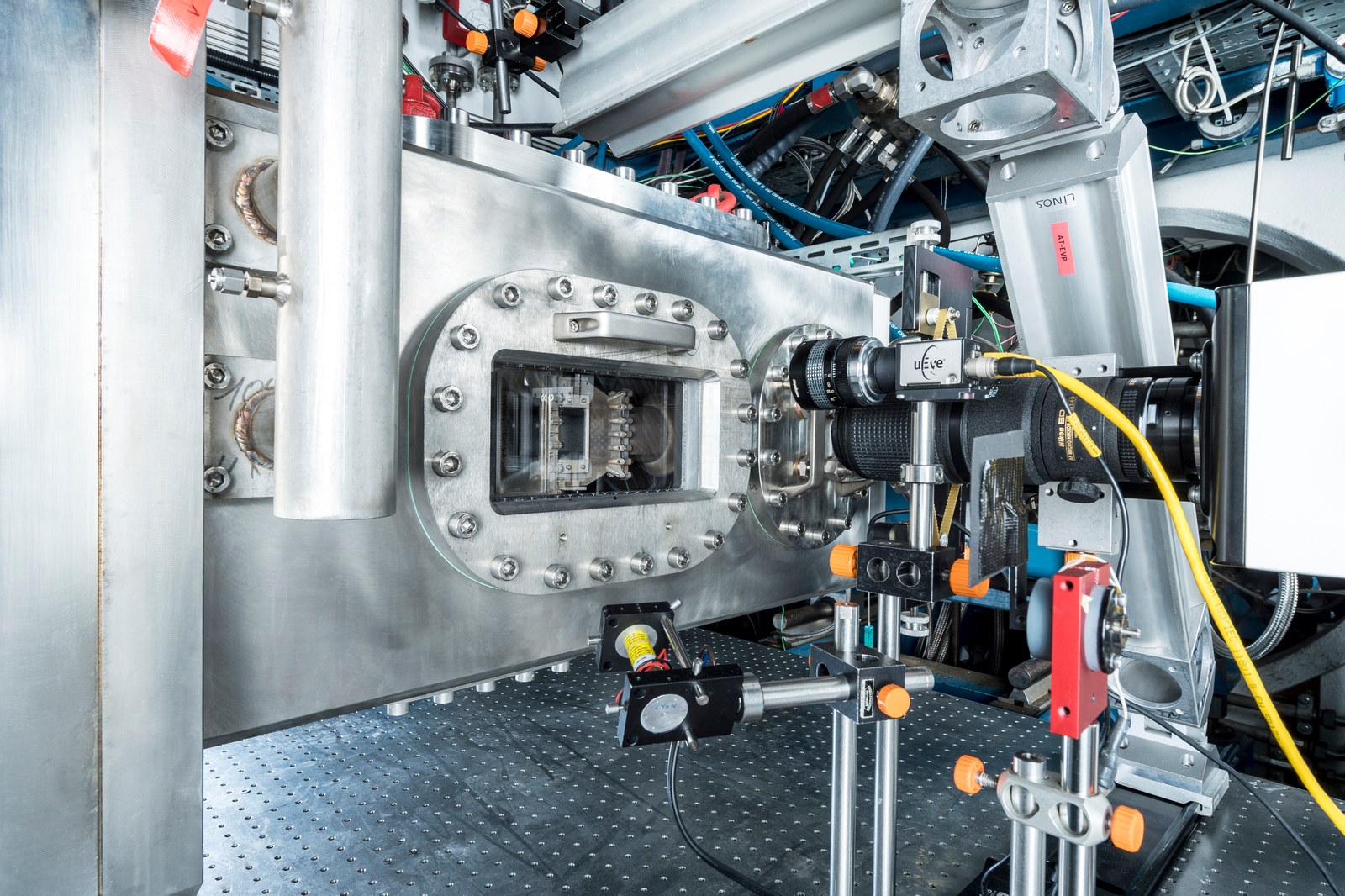
Dr. Christian Willert: In den Versuchen nutzen wir verschiedene Messtechniken. Sie vervollständigen das Bild des Verbrennungsvorgangs. Außerdem können wir mit solchen Experimenten Simulationen überprüfen und verbessern, welche die Kolleginnen und Kollegen aus der Numerischen Simulation vorab durchgeführt haben. Mit den optischen Messungen erfassen wir die Reaktions- und Wärmefreisetzungszonen, ohne dabei die Brennkammerströmung zu beeinflussen. Außerdem können wir durch Strömungsfeldmessungen die Bewegung des Luft-Wasserstoff-Gemischs und der Reaktionsprodukte durch die Brennkammer verfolgen.
Janus: Am HBK1 schauen wir uns Technologieentwicklungen in einem frühen Stadium an. Der HBK5 ist unser größter Verbrennungsprüfstand am DLR. Hier können bis zu den hohen Technologiereifegraden 5-6 ganze Ringbrennkammern für reale Triebwerke untersucht werden. Das Besondere ist, dass viele Prüfstände beim DLR in Köln entstanden sind, sich ständig weiterentwickelt haben und stetig an neue Anforderungen angepasst werden. Außerdem haben wir eine einzigartige Infrastruktur für Luft, Kerosin und Sonderkraftstoffe, die unsere Anlagen je nach Forschungsgegenstand versorgen. Zudem punkten wir seit einigen Jahren mit unserer hervorragenden Wasserstoffinfrastruktur.
Wie laufen die Wasserstoffversuche in der gläsernen Hochdruckbrennkammer genau ab?
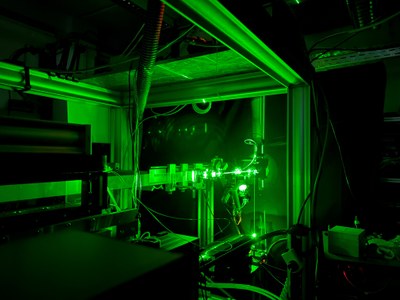
Janus: Man kann sich das so vorstellen, dass man aus der Ringbrennkammer eines Flugzeugtriebwerkes ein Segment „herausschneidet“. Die verglaste Kammer wird in der Regel mit einzelnen Brennern unter realitätsnahen Bedingungen betrieben: hohe Luftvorwärmtemperatur und Betriebsdrücke bis 25 bar. Dies ist ein Alleinstellungsmerkmal dieses Prüfstands. Der Brenner wird dann unter verschiedenen Betriebsbedingungen getestet, zum Beispiel im Leerlauf auf dem Rollfeld oder beim „Taxiing“ – also dem Fahren in Richtung Startbahn oder Parkposition –, beim Abheben oder in der Flugphase. Wir haben ein Messsystem, das die Abgaszusammensetzung analysiert, und wir können in die Brennkammer hineinschauen, um dort Strömungen zu messen. Darüber hinaus benutzen wir Messverfahren, die chemische Prozesse in der Brennkammer abbilden. Auf diese Weise möchten wir das Eindüsverfahren für den Brennstoff so verbessern, dass möglichst wenige Schadstoffe entstehen.
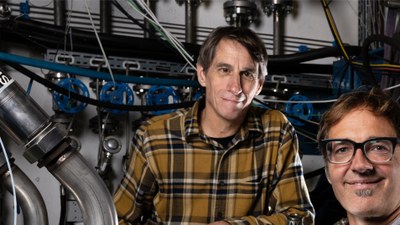
Als bildgebendes Verfahren nutzen wir Laser, die einen sogenannten Lichtschnitt, auch Transsektion genannt, erzeugen. Damit werden einzelne Ebenen im Brennbereich sichtbar.
Willert: Als bildgebendes Verfahren nutzen wir Laser, die einen sogenannten Lichtschnitt, auch Transsektion genannt, erzeugen. Damit werden einzelne Ebenen im Brennbereich sichtbar. Das lässt sich in gewisser Weise mit der Computertomografie vergleichen, bei der man per Röntgenstrahlung das Gehirn in zweidimensionalen Scheiben darstellt. In unserem Fall bilden die Kameras, die durch ein Sichtfenster in der Brennkammer filmen, diese Ebenen ab.
Wo besteht denn Potenzial für Optimierung?
Janus: Je tiefere Einblicke wir in die Strömung bekommen, desto bessere Ansatzpunkte finden wir zur Beantwortung der Frage, wie wir den Ablauf in der Brennkammer optimieren können. Damit könnten wir beispielsweise Temperaturspitzen vermeiden. Wo Luft und Brennstoff „unglücklich“ aufeinandertreffen, entstehen mitunter kurzfristig sehr hohe Temperaturen – das fördert die Entstehung von schädlichen Stickoxiden. Bei den Wasserstofftests nutzen wir einen Brenner, den wir selbst gestaltet haben und bei dem wir Phänomene und Prozesse beeinflussen können. So erfahren wir, ob die technische Idee, die dahintersteckt, sich bewahrheitet.
Willert: Weiteres Potenzial besteht im hinteren Teil der Brennkammer, am Austrittskanal, also dort, wo die heiße Strömung die thermische Energie an die Maschine abgibt. Mit unseren Lasern sehen wir Dinge, die das Auge nicht erkennen kann. Wir arbeiten zum Beispiel sehr viel mit UV-Licht, um Radikale – Hydroxyl, molekular kombinierten Sauerstoff und Wasserstoff – anzuregen. Die Fluoreszenz nutzen wir, um Konzentrationen und Temperaturen abzuleiten. Die optimale Gestaltung der Temperaturverteilung ist auch an dieser Stelle enorm wichtig, um Beschädigungen an der Turbine abzuwenden und eine möglichst lange Lebensdauer zu erreichen.
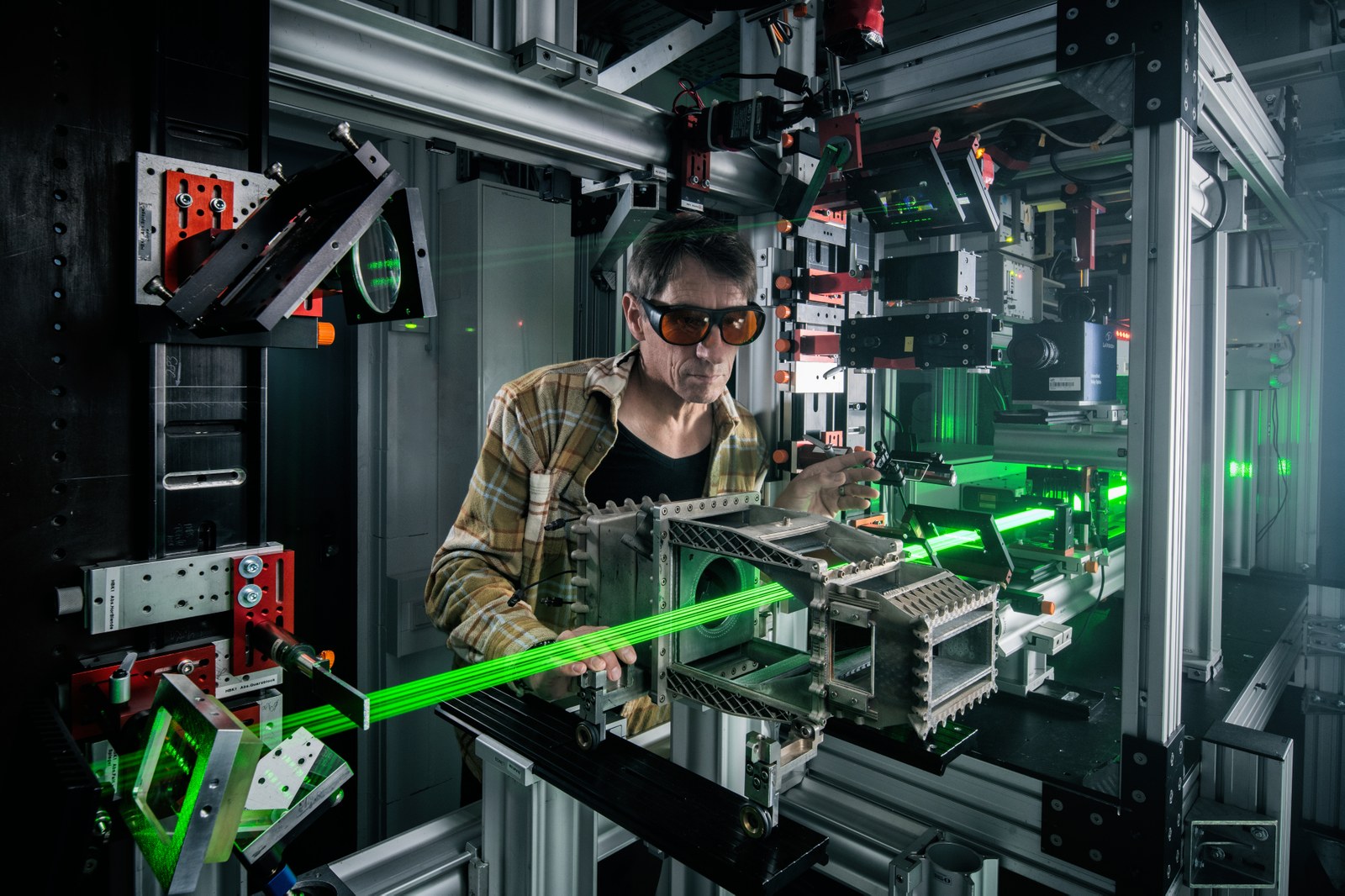
Wenn man hundertprozentigen Wasserstoff verbrennt, bekommt man wirklich nur Wasser und Wärme als „Abfallprodukte“?
Willert: Aus der Turbine kommt tatsächlich nur Wasser in Form von Dampf. Dadurch, dass Stickstoff in der Luft ist, können zusätzlich auch Stickstoffoxide entstehen, was es zu vermeiden beziehungsweise zu minimieren gilt. Durch den Kontakt mit der kalten Umgebungsluft bilden sich Kondensstreifen wie bei herkömmlichem Flugzeugtreibstoff.
Gibt es innerhalb des DLR Synergien zwischen der Antriebstechnik und anderen Instituten bei den Wasserstoffverbrennungsversuchen?
Willert: Auf jeden Fall! Was die technischen Verbrennungsinhalte und die Verbrennungsdiagnostik angeht, kooperieren wir mit dem Institut für Verbrennungstechnik in Stuttgart. Und wir sind mit den Kolleginnen und Kollegen des Instituts für Aerodynamik und Strömungstechnik in Göttingen in engem Austausch bei Messverfahren für hohe Strömungsgeschwindigkeiten. Aufgrund der Nutzung von Wasserstoff in Raketentriebwerken gibt es auch Überschneidungen mit den „Raumfahrern“ in Lampoldshausen, was die Entwicklung von optischer Messtechnik angeht.
Wasserstofftestanlagen des DLR-Instituts für Antriebstechnik in Köln
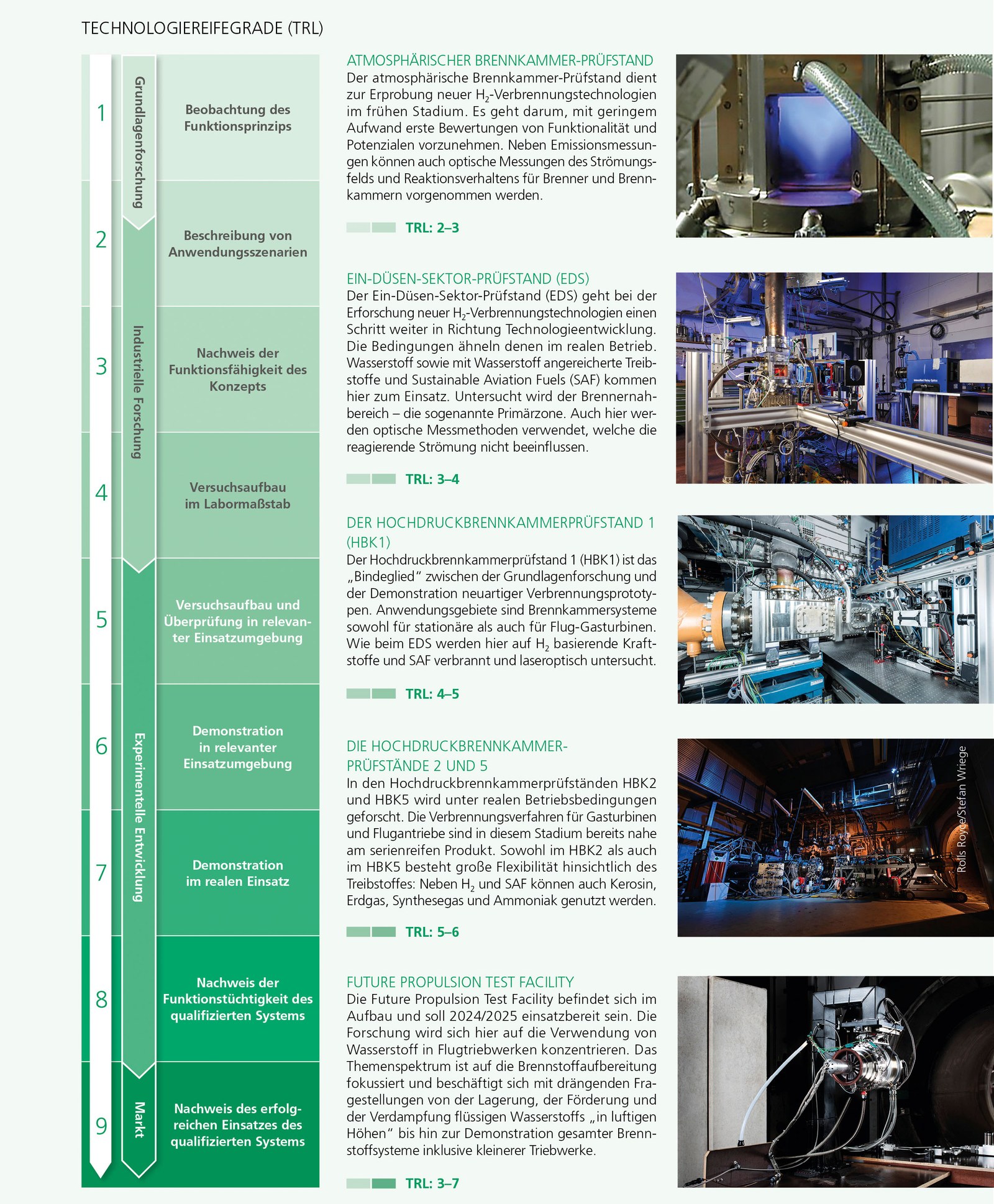
Die Fragen stellte Michael Müller. Er ist Redakteur in der DLR-Kommunikation. Ein Beitrag aus dem DLRmagazin 174.