MÖWE - Maximal ökoeffiziente Wing Entwicklung
Für die Flügelschalen der nächsten Generation von Kurz- und Mittel-streckenflugzeugen werden derzeit neue Fertigungstechnologien und –prozesse betrachtet. Entgegen des derzeitigen industriellen Einsatzes von vorimprägnierten Fasern (Prepregs), sollen bebinderte Trockenfasern auf einem Formwerkzeug abgelegt und der fertige Preform in einem nachgeschalteten Prozess mit Harz infiltriert werden. Daraus ergeben sich zusätzliche technologische und wirtschaftliche Möglichkeiten und Fragestellungen, die im Rahmen des Vorhabens behandelt werden sollen. Die vom DLR im Verbund geleistete Arbeit dient dem Ziel, die Leistungsfähigkeit des deutschen Standortes zu erhalten und weiter auszubauen. Das DLR trägt im Verbund bei, Fertigungskonzepte für Faserverbundstrukturen für eine nachhaltige Luftfahrt zu entwickeln, bewertbar zu machen und zu demonstrieren. Durch die ganzheitliche Betrachtung werden fokussiert die Preformfertigung sowie die Nachhaltigkeitsbewertung und -optimierung adressiert.
Mit dem vom DLR geleisteten Beitrag werden die industriellen Partner unterstützt, ihre Position am Markt zu etablieren bzw. speziell für Faserverbundstrukturen ihre Position zu stärken, damit auch für die Zukunft relevante Bauweisen durch die hiesige Industrie abgebildet werden können und damit Wertschöpfung in Deutschland generiert werden kann.
Das DLR erarbeitet innerhalb des Verbundvorhabens MÖWE insbesondere effiziente Technologien zum DFP-Preforming und integriert diese gemeinsam mit dem Projektpartner Broetje in eine industrialisierbare Endeffektortechnologie. Darüber hinaus werden Methoden erarbeitet, die eine Energieprädiktion von DFP-Prozessen in der virtuellen Fertigung ermöglicht. Diese Informationen werden zusammen mit Stoffströmen und weiteren Prozessinformationen in eine Nachhaltigkeitsbewertung überführt. Im Wesentlichen werden innerhalb dieses Vorhabens die folgenden Ziele angestrebt:
- Schaffung einer empirischen Datenbasis szenariobasierter Energieverbräuche für DFP-Prozesse sowie Modellierung der Szenarien
- Schaffung einer Methodik zur KI-basierten Prädiktion von Energieverbräuchen für roboterbasierte DFP-Prozesse
- Erarbeitung einer Methodik um ökologische Treiber in die Kostenmodellierung von Prozessketten zu integrieren
- Erarbeitung einer Schnittstelle zur ökonomischen Prozesskettenmodellierung
- Bestimmung von Entformungskräften von FVK-Komponenten unter Verwendung von internen Trennmitteln und Ableitung erforderlicher Mindestmengen bei gleichzeitiger stabiler Prozessführung
- Weiterentwicklung der CoRe HeaT Technologie um 2“ Multitow-Ablage zu ermöglichen
- Integration der Technologie in einen industriellen Endeffektor der Firma Broetje sowie gemeinsame Validierung der Entwicklungen bei einer repräsentativen Preformfertigung
Beteiligte Projektpartner
Fördergeber
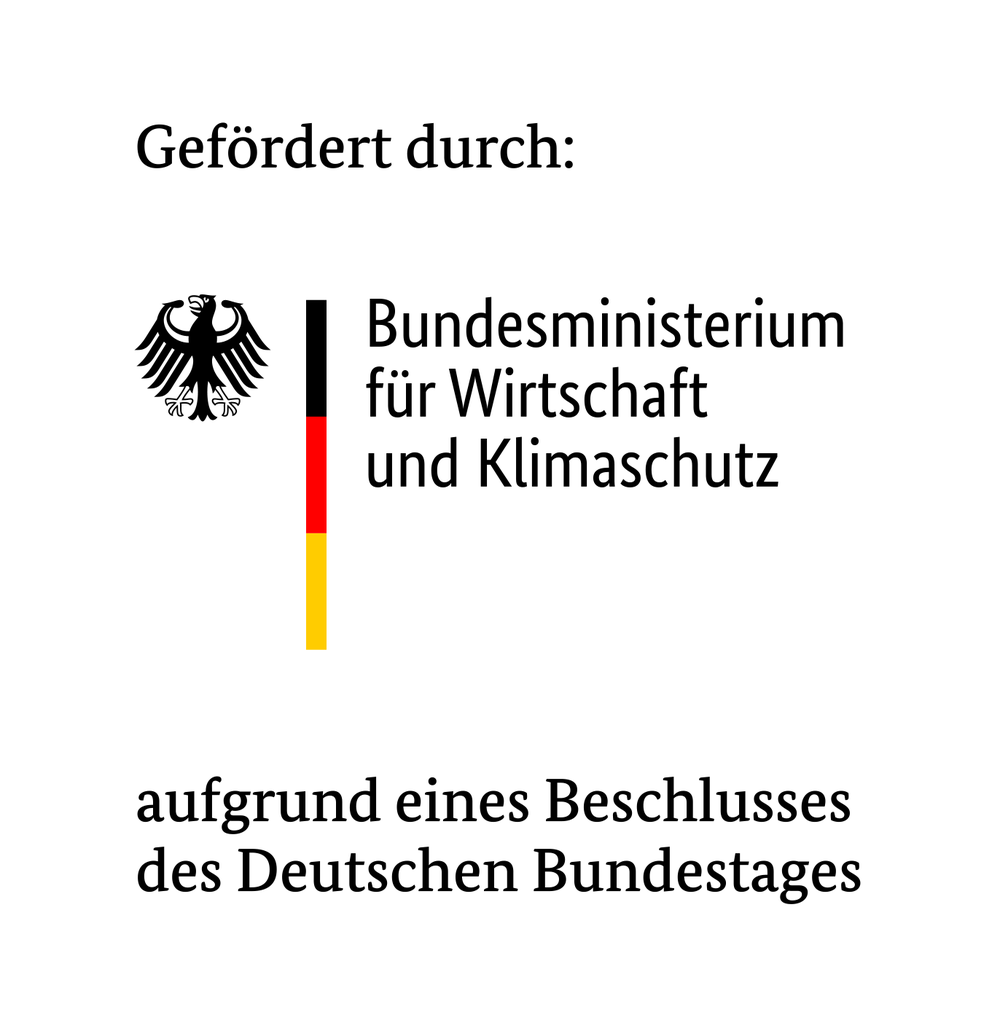